4S “Sorun Giderme Metodolojisi” Sanayideki En Verimli Uygulamalar-I
Bu konuda, kendi çalışmalarında farklı endüstrilerin adapte ettikleri En Verimli Uygulamalar ile ilişkili yeni bir sayfa açmaktayız.
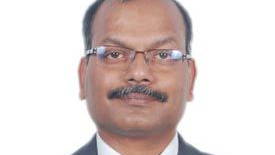
Bu konuda, kendi çalışmalarında farklı endüstrilerin adapte ettikleri En Verimli Uygulamalar ile ilişkili yeni bir sayfa açmaktayız.
Bu konuda, kendi çalışmalarında farklı endüstrilerin adapte ettikleri En Verimli Uygulamalar ile ilişkili yeni bir sayfa açmaktayız. Bu yeni sayfa, IIMA’da ileri düzey kalite yönetim sistemleri ve Altı Sigma Siyah Kuşak Metodolojisinde, Makine Mühendisliği eğitimi deneyimi sahibi, Indo-MIM Bangalore’nin Genel Müdür Vekili R Sai Krishna Rayalu tarafından hazırlanacaktır.
Günümüzün sürekli yenilenen sanayi dünyasında, sorun çözümünün ciddi önem taşıdığı güçlükler yaratan durumlar yaşamaktayız. Çeşitli sorunların giderilmesi için harcanan zaman katma değersiz zamandır ve en aza indirgenmelidir. Sonuç olarak, Sistematik Sorun Giderme Metodolojisi önemli destek sağlamaktadır.
Indo-MIM’de sorun çözümü ile ilgili emsalsiz bir yaklaşımı etkin bir şekilde hayata geçirmekteyiz ve diğer sanayi kolları için metodoloji prosedürü ile birlikte bir formatta formüle edebilirsek çok verimli bir araç olacağını düşünmekteyiz.
Ayrıca, bu yöntemin olumlu sonuçlar yaratabilmek için bu tekniğin başarı ile uygulandığı alanlara ilişkin örnek olay çalışmaları uygulamayı planlamaktayız.
4-S yaklaşımı basit bir 4 aşamalı sorun çözme yöntemidir ve şu dört en güçlü aracı kullanır: SAPTA, SORUNA ODAKLAN, SORUNU BUL & SONUÇLANDIR.
Kuram işleme mekanizmasına dayanmaktadır. Herhangi bir müşteri şikayeti, bu dört basit evrede işlenir.
Yaklaşım temel olarak 8D’den türetilir ve dört ekibe pay edilir ve işlemi daha başarı ile tamamlayabilmek için her ekip kendi ilgili alanlarına odaklanır.
Her bir evre (SAPTA, SORUNA ODAKLAN, SORUNU BUL & SONUÇLANDIR) bir liderden oluşur ve bu aşamayı aşmak ve sonraki evreye aktarmak zorundadır. SAPTA - Bu grubun üyeleri, telekonferans yolu ile müşteriye sorunu açıklayarak veya e-posta ile yanıtlayarak SAPTAR. Ayrıca, acil durum yanıtları ve geçici 3D kontrol amaçlı girişimler bu aşamada müşterinin korunması için uygulanır. SORUNA ODAKLANMA ekipleri, bu evrede kurulur ve ekip sorun kaynağı olan konulara odaklanır. Bu aşamada, “Beyin jimnastiği” ve “sebep & sonuç analizi” uygulanan temel faktörlerdir. SORUNU BUL - Bu evrede son temel sebepler bu aşamada sorun saptanır ve düzeltici işlemler başlatılır. “3 x 5 Neden analizi” bu aşamadaki temel uygulamadır. SONUÇLANDIR - Bu son evredir ve süregelen bir aşamadır. Burada düzeltici uygulamalar uygulanır, doğrulanır ve onaylanır. Aynı zamanda, 8D düzeltici uygulama raporları hazırlanır ve müşterilere yollanır.
Örnek Olay
Müşteri: Kompresör imalatçısı
Sorun: Bu müşteri için supap yuvaları tedarik etmekteyiz. Müşteri, makine yüzeyi üzerinde çentik izleri ve girintiler olduğundan şikayet etmektedir. Bu yüzey, üzerinde lazer kaynaklama yapıldığı için çok önem taşır.
Güçlükler: Bizimle ilişkili zorluklar aşağıda tanımlanmaktadır:
• 24 Saat içerisinde sorunun ele alınması gereklidir.
• Bu şekilde çok fazla ürünün olması ve müdahalelerde gecikmeler, müşteri montaj hattının kapanmasına yol açabilir.
• Arızalı olan gerçek ürün, müşterinin deniz aşırı bölgeden olmasından dolayı bizden çok uzaklardaydı bu yüzden sorunu tam olarak anlamakta güçlük çektik.
• Üretim aşamasındaki ürünler ve üretilmiş olan ürünlerde bu arızaların hiçbirisi görülmemişti, bu yüzden sorunun tanımını kavramak daha yüksek önem kazanmıştı.
Uygulamalar: Bu güçlükleri gidermek için bu şikayeti bize özel “4S yaklaşımı” kapsamına aldık.
Faz 1: 1S - Sapta
• 1S lider eğer müşteri ile sorunun daha net olarak kavranılması için bir telefon görüşmesi yapması.
• Temel veri ve bilgilerin toplanması.
• İmalatın farklı evrelerinde, uygun ürünler ile ilgili bilgi toplama amaçlı üretim mühendisleri ve planlama departmanı ile ortak çalışmak.
• Geçici girişimlerin geliştirilmesi.
• Geçici 8D düzeltici faaliyet raporu göndererek müşteriye geri yanıt vermek.
• Plana göre bütün 1S girişimlerinin yapıldığını ispat edebilmek için bir kontrol listesi kullanıldı.
Faz 2 & 3: 2S - Soruna Odaklanma & 3S - Sorunu Bulma
• 2S lider faz 1’den gerekli olan bilgileri edinip faz 2’ye (Odaklanma) geçer.
• İlgili bireyler ve yöntem bilgisine sahip bireyleri bir araya getirerek fikir üretmektedir.
• “Sebep & sonuç analizi” aracını uygulayarak temel sorun yaratan hususları tanımlamaktadır.
• İmalat & nakliyatın bütün aşamalarında, malzeme, işleme hususları, malzemeler yumuşak yapılı ve kolaylıkla bozulup, çizilebileceği için önemli bir sebep olarak değerlendirildi.
Faz 4: 4S - Sonuçlandır
• 4S lider, faz 1, 2 & 3’deki veriler ile faz 4 (Sonuçlandırma) uygulamalarına geçmektedir.
• Düzeltici işlem planı hayata geçirildi “Ürünler üzerinde gelip geçen şokların etkilerini ortadan kaldırmaya yönelik modifiye edilen ambalajlama tasarımları”.
• Uygulamaların verimliliği yeni sorun yaratmamalarından emin olabilmek için denetlenmiştir.
• Sistematik uygulamalar, aynı zamanda uygulandı ve gözlemlendi “SOP projelerin başlarında ambalajların doğru tasarlanması için geliştirildi”.
• Belgeler uygun şekilde güncellendi.
• Bütün 4S uygulamaların planlarda kullanıldığından emin olabilmek için kontrol listesi hazırlandı.
• Müşteriye son bir onay e-postası, düzeltici uygulamayı hayata geçirdikten sonra parçalar ile ilgili geri bildirim alabilmek için gönderildi.
• Düzeltici işlem verimliliği ile birlikte tamamlanmış 8D müşteriye gönderildi.
Sonuçlar: Uygulamalarımız aşağıdaki sonuçları sağlamıştır:
• Müşteriler, Indo-MIM personeli kendileri ile hemen irtibata geçtiği için bundan çok fazla memnuniyet duymuşlardı.
• Müşteri yakınlığının kurulması.
• Net sorun çözümü, sorunların hızla çözümünü sağlayan müşterinin açıklamaları net olarak anlaşıldı.
• 8D Düzeltici faaliyetlerini tamamlama amaçlı hedeflenen tarihin tutturulması.
• 8D’nin başarılı ve verimli şekilde sonlandırılması.
• Sorun çözümünde TFC ekibinin başarılı uygulamaları.
• İş sahibinin kendisine aktarılan her safhada planlanan faaliyetlerin verimli şekilde uygulanması.
Sorun çözümünde 8D’nin bütün temel elementlerinin yerine getirilmesinin sağlanması
• Sorunlar daha sonra 3S ve 4S liderleri ile ortaklaşa analiz edildi.
• Temel sebep “Neden-Niçin analizi” aracı vasıtasıyla çözümlendi
• Temel sebep, temel sebebin sorunun yeniden doğmasına yol açabileceğinin irdelenebilmesi için onaylandı.
• “Taşınma esnasında alınan darbelerin zararlarının önlenmesinde ambalaj tasarımının yeterli olmadığı” anlaşıldı.
• Bütün 2S & 3S uygulamalarının plana uygun yürütüldüğünün anlaşılması için kontrol listesi yapıldı.
• Ana sebebi kapsayan son 8D & önleyici uygulama planı şikayetin alınmasından sonraki 9. günde gönderildi.
Bu faaliyet 8 iş gününde tamamlandı.
Yazar R Sai Krishna Rayalu, Indo-MIM’de Kalite departmanında Genel Müdür Vekili olarak çalışmaktadır. Indo-MIM firmasında firmanın kurulduğu tarihten itibaren bulunmaktadır ve ABD’de MIM üzerinde ilk eğitim alanların başındadır.
İlk olarak tasarım departmanında uzun süreli ve daha sonra ise proses departmanında çalışmıştır. Bu görevleri esnasında, Altı sigma siyah kuşak metodolojisi üzerinde eğitim almıştır. Makine Mühendisliği üzerinde yüksek Lisans yapmış, geçtiğimiz yıldan bu yana Indo-MIM’de Kalite Kontrolden sorumludur. Ayrıca, IIMA’da ileri kalite kontrol eğitimi almıştır.
. . .
İçerik sadece atıfta bulunularak yayınlanabilir: Sivas İş Dünyası. Editöryal görüş, yazarın görüşüne aykırı olabilir.