Aşırı Plastik Deformasyon Yöntemiyle Nano -Yapılı Ve Yüksek Dayanımlı Üretimi
Günümüz dünyasındaki global yarış, malzeme mühendisliği alanında yeni teknolojileri
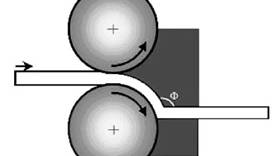
Günümüz dünyasındaki global yarış, malzeme mühendisliği alanında yeni teknolojileri
Günümüz dünyasındaki global yarış, malzeme mühendisliği alanında yeni teknolojileri ve üretim yöntemlerini de beraberinde getirmektedir. Öte yandan, teknolojik alandaki hızlı gelişme ve bunu getirdiği rekabet, müşterilerin artan istek ve düşüncelerinin üst düzeyde karşılanmasını gerektirmektedir.
Bu nedenle geleneksel malzeme gruplarındaki ürünlerin kullanıcı sektörlerin talepleri doğrultusunda çeşitlendirilmesi, diğer taraftan bu alanlardan ileri malzeme alanlarına doğru açılım yapılması gerekmektedir. Bu açıdan çelik şirketleri de, en son teknolojiyle üretim yapmak ve ürünlerini sürekli geliştirmek zorunda kalmaktadır.
Çelik endüstrisinde bu son teknolojinin getirdiği ürünlerden birisi de IF-çeliği (Interstitial-Free steel (IF-steel)) dir. Modern üretim teknolojisi kullanılarak düşük karbonlu çeliğin C ve N gibi arayer elementleri Ti ve/veya Nb gibi elementlerle üretim sırasında stabilize edilmekte ve özellikle karbon oranları 0.010’un altına düşürülmektedir.
Bu sayede mükemmel şekillendirilebilirlik özelliği kazanan söz konusu çelikler, özellikle otomobil ve beyaz eşya üreticilerinin gözdesi haline gelmektedir. IF-çeliği, karmaşık yapıya sahip sac parçaların derin çekilmesinde, gererek veya dövülerek şekillendirilmesinde geleneksel yapıdaki çeliklere göre çok daha üstün özellikler sergilemektedir. IF-çeliği günümüzde sadece sıcak ve soğuk sac hadde ürünü olarak değil aynı zamanda çinko ve başka elementlerle de kaplanarak özellikle gelişmiş ülkelerde otomotiv endüstrilerinde kullanılmaya başlanmıştır. Bunun sonucunda özellikle sanayileşmiş ülkelerde IF-çeliğinin üretimi ve kullanımı her geçen yıl katlanarak artmaktadır.
Öte yandan, son yıllarda otomotiv endüstrisinde artan yakıt fiyatları nedeniyle yeni karoseri tasarımı ve yeni malzeme türlerine yönelik araştırma çalışmalarında hızlı bir artış göze çarpmaktadır. Bu çalışmalarda, otomotiv gövdesi ve diğer yapısal parçaların üretiminde daha hafif, özgül mukavemeti yüksek, şekillendirilebilirliği mükemmel ve güvenilir malzemelerin üretimi ve uygulamaya aktarılması konusunda yoğun araştırma çalışmaları devam etmektedir.
Bilindiği gibi IF-çeliğinin akma (yaklaşık 150 MPa) ve çekme mukavemetleri (yaklaşık 300 MPa) geleneksel çelik malzemelere göre oldukça düşüktür. Bu durum, şekillendirme açısından (daha az şekillendirme kuvvetine ihtiyaç göstermesi) bir avantaj olarak gözükmesine karşın, mukavemetin ön plana çıktığı uygulamalarda (otomobilde yük taşıyıcı parçalar ve dış kuvvet etkisine maruz kalan paneller gibi) bir yetersizlik olarak ortaya çıkmaktadır. Bu durumda belli bir mukavemet değerine ulaşmak için nispeten daha kalın kesitli ağır yapılar ortaya çıkmaktadır. Bu da özellikle otomotiv sektöründe yakıt tüketimini artırıcı bir etken olarak değerlendirilmektedir. Bu nedenle son yıllarda sanayileşmiş ülkelerde yüksek dayanımlı IF-çeliği üretimi konusunda yoğun araştırma çalışmaları başlatılmıştır. Yüksek dayanımlı IF-çeliğinin üretilmesiyle beraber mevcut uygulamalar için daha hafif yapıların oluşturulması özellikle otomotiv endüstrisinde bir avantaj olacaktır.
Bu arada, yüksek dayanımlı hale getirilirken, söz konusu çelikte şekillendirmeyi engelleyici tarzda süneklik düşümünün de oluşmaması gerekmektedir. Bu nedenle daha hafif yapıların oluşturulabilmesi, IF-çeliklerinin mukavemet değerlerinin, şekillendirilebilirlik özelliklerini azaltmadan artırılmasını zorunlu kılmaktadır. Geleneksel mukavemet artırma yöntemleri IF-çeliklerinde bu anlamda istenilen özellikleri sağlayamamaktadır. Ayrıca geleneksel yöntemler mukavemet artışıyla beraber büyük oranda süneklik düşümüne de neden olmaktadırlar. Bu da söz konusu çeliklerin şekillendirilmesinde önemli bir problem olarak karşımıza çıkmaktadır. Bu nedenle IF-çeliği günümüzde daha çok yük taşıyıcı olmayan koruyucu sac malzemesi olarak kullanılmaktadır.
Geleneksel yöntemlerin yetersiz kalışı, IF-çeliğinin mekanik özelliklerinin iyileştirilmesinde geleneksel olmayan yöntemlerin de denenmesini zorunlu hale getirmektedir. Son 10 yıl içerisinde üretim sonrası uygulanan çeşitli proses yöntemleriyle kütlesel formda ultrakristalin veya nanoyapılı malzemelerin üretilebilme imkânlarının ortaya çıkması ve bu yeni nesil malzemelerin geleneksel malzemelerde mevcut olmayan bir çok üstünlükleri üzerinde toplaması gözleri bu alana çevirmiştir. Aşırı Plastik Deformasyon (APD) (Severe Plastic Deformation-SPD) yöntemleri de bu amaçla geliştirilmiş olup, söz konusu yöntemlerin uygulandığı mühendislik malzemelerinde çok olumlu sonuçlar elde edilmiştir.
Özellikle APD yöntemlerinden biri olan “Eş Kanalda Açısal Ekstrüzyon (EKAE)” (Equal-Channel Angular Extrusion-ECAE) ile kütlesel formda ve mühendislik uygulamalarında kullanılabilecek boyutlarda ultrakristalin yapılı (100-1000 nm arasında tane boyutuna sahip) malzemeler üretilebilir hale gelmiştir. Bu yöntem deformasyonu zor olan gevrek yapılı birçok malzemeye bile başarıyla uygulanabilmekte ve bu malzemelere yüksek mukavemet ve süneklik özellikleri kazandırılabilmektedir. Ayrıca, proses sonrası bir çok malzeme grubunun yorulma ve darbe dayanımları, darbe ve ses sönümleme kapasiteleri ve şekillendirilebilirlik özelliklerinde büyük oranlarda iyileşmeler sağlanmıştır.
Literatür çalışmalarına bakıldığında, bu yöntemin değişik amaçlar için pek çok mühendislik malzemelerine uygulandığı ve bir çok malzeme grubundan da oldukça başarılı sonuçlar alındığı görülmektedir. Bu yöntemde dikkati çeken en önemli özelliklerden biri, tane yapıları inceltilen (<1 m) malzemelerin hem mukavemet hem de süneklik değerlerinin bir arada artırılabilmesidir [1-3]. Bu sayede, özellikle deformasyonu zor olan gevrek yapılı malzemelerin şekillendirilebilirlik özellikleri de artırılabilmektedir.
Nitekim, Ti ve Mg alaşımları bu yöntemle proses edildiklerinde mukavemet değerleri önemli ölçüde artarken, süneklik değerlerinde de çok önemli iyileşmelere elde edilmiştir [4-6]. Ayrıca, bu yöntemin malzemelerin; yorulma dayanımlarını [7-10], darbe ve ses sönümleme kapasitelerini [11] ve süperplastiklik özelliklerini [12-13] büyük oranda artırdığı belirlenmiştir. Bugüne kadar söz konusu yöntemin uygulandığı belli başlı malzeme grupları; saf Al ve alaşımları [14-17], Ti ve Mg alaşımları [18-21], saf Cu ve alaşımları [22-25], bazı kompozit malzemeler [26], paslanmaz çelikler [27], şekil hafızalı metaller [28, 29], intermetalikler [30], toz metalurjisi ile üretilmiş malzemeler [31,25] olarak sıralanabilir. Ayrıca söz konusu yöntem demir ve çelik grubu bir çok alaşıma da uygulanmış ve çok olumlu sonuçlar alınmıştır.
Yukarıda verilen bilgiler ışığında bu çalışmanın amacı, yeni bir APD yöntemi olan EKAE metodunun temel prensiplerini ortaya koymak ve bu yöntemin gerek bilet formunda ve gerekse saç formunda IF-çeliğine uygulanma potansiyelini tartışmaktır. Ayrıca, tarafımızdan yapılan ön çalışmalardan elde edilen bazı sonuçlar da verilecektir.
2. Önerilen yöntem: “Eş kanalda açısal ekstrüzyon (EKAE)”
EKAE proses tekniği ilk olarak 1980’li yıllarda SPD yöntemi olarak V.M. Segal ve arkadaşları [32] tarafından geliştirilmiştir. 1990’lı yıllardan sonra ise söz konusu yöntem üzerine bir çok araştırma grubu tarafından yoğun çalışmalar başlatılmış ve bu yöntemin kütlesel formda ultrakristalin veya nanoyapılı malzeme üretiminde kullanılabileceği ortaya çıkmıştır. Özellikle Valiev ve arkadaşları [33] tarafından başlatılan ve ardından dünyanın birçok ülkesindeki araştırma grupları tarafından yürütülen çalışmalar, bu yöntemle ilgili geliştirmelere baş döndürücü bir hız kazandırmıştır. Daha çok laboratuar ölçekli gerçekleştirilen çalışmalar ışığında söz konusu yöntemin endüstriyel uygulama alanları araştırılmaya başlanmış ve belli merkezlerde prototip aşamasında da olsa uygulama çalışmaları ortaya çıkmıştır. EKAE yönteminin diğer APD yöntemlerine göre pek çok üstünlükleri vardır. Bunlar; proses sonrası homojen içyapıların elde edilmesi, tane morfolojisinin ve tekstür oluşumunun kontrol edilebilmesi ve proses işleminin kolaylıkla gerçekleştirilmesi sayılabilir. Ayrıca, bu yöntemle çok daha büyük boyutlarda ve kütlesel formda ultrakristalin yapılı malzemelerin üretilmesi ve üretilen malzemelerin mühendislik uygulamalarında kullanılabilir ebatlarda olması da bu yöntemin diğer yöntemlere göre önemli bir üstünlüğüdür.
EKAE yöntem basitçe; eş kesitli iki kanaldan katı durumdaki malzemenin geçirilmesi ve arakesitten geçiş sırasında malzemenin iç yapısında basit kayma mekanizması ile aşırı oranda plastik deformasyon oluşturup tane boyutunun inceltilmesi esasına dayanmaktadır [34-35]. Bu yöntemde kullanılan klasik bir kalıp ve deformasyon modeli Şekil 1’de verilmiştir. Bu şekilden görüldüğü gibi; dikey kanala yerleştirilen malzeme (bilet) bir itici (zımba) ile yatay kanala doğru itilmektedir. Bu sırada örnek iki kanal arakesitinden geçerken basit kayma mekanizmasıyla plastik deformasyona uğratılmaktadır. Proses sırasında numune içerisinde oluşturulan birim şekil değiştirme miktarı (strain) kalıp geometrisi ve paso sayısına bağlı olarak değişmektedir. (Kalıp içerisinde oluşan deformasyon prosesi oldukça karmaşık bir yapıya sahip olup, bu konuda geniş bilgi [3,4,5, 35] referanslarında bulunabilir).
Giriş ve çıkış kanallarının kesit alanlarında önemli bir farkın olmaması ve kanal içerisinde açısal bir dönüşün meydana getirilmesi bu yöntemi geleneksel ekstrüzyon yöntemlerinden ayıran en önemli özelliktir. Bu sayede aynı numune (ya da parça) ardı ardına teorik olarak sonsuz sayıda EKAE işlemine tabi tutularak aşırı oranda deformasyona uğratılabilmektedir. Böylece, malzeme içyapısında oluşturulan deformasyon oranı ve dolayısıyla da yapısal incelme miktarı istenen seviyelere kadar çekilebilmektedir. Bu yöntemin diğer bir avantajı da, birbiri peşine yapılan proseslerde numunenin kanala giriş rotasının değiştirilerek yapısal dönüşümlerde ve dolayısıyla elde edilmesi hedeflenen özelliklerde değişkenlik sağlanabilmesidir. Şekil 2’de, bu güne kadar literatüre geçmiş olan 4 temel EKAE rotası verilmiştir [1]. Rota A’da numune her pasoda aynı pozisyonda kanala girerken, rota BC’de +90°, rota BA’da 90 ve rota C’de +180° çevrilerek kanala sokulmaktadır. Ayrıca son zamanlarda, bu rotaların kombinasyonu şeklinde uygulan yeni rotalar üzerine de çalışmalar devam etmektedir [36].
EKAE yönteminin endüstriyel alanda kullanılabilmesi ve özellikle seri üretime uygun hale getirilmesi, bu yöntemin geleceği acısından çok önemli görülmektedir. Bu nedenle, bu konudaki çalışmalar da artarak devam etmektedir. Bu çalışmalardan ikisi; sürekli ve döner kalıplı EKAE yöntemleridir. Şekil 3’de sac malzemeler için geliştirilmiş olan sürekli EKAE yöntemi verilmiştir. Bu yöntemde, yassı malzemenin kalıba girişi ve sürekli beslenmesi bir merdane sistemiyle sağlanmaktadır. Bu sistemde aynı zamanda istenirse malzeme kalıba girmeden önce haddelenebilmektedir. Bu yöntemin özellikle çelik sac ve diğer yassı mamullere uygulanabileceği düşünülmektedir. Dönel kalıplı EKAE yönteminde (Şekil 4) ise proses edilecek numune kalıptan çıkarılmadan ardı ardına çok sayıda EKAE pasosuna tabi tutulabilmektedir. Bu sayede, özellikle endüstriyel uygulamalarda zaman tasarrufu sağlanmaktadır. Bu iki yöntem üzerindeki çalışmalar devam etmekte olup, söz konusu yöntemlerin olumsuz tarafları düzeltilerek uygulanabilir hale sokulmaya çalışılmaktadır.
Şekil 3. Sac malzemelerin prosesinde kullanılabilecek sürekli beslemeli EKAE yönteminin şematik gösterimi [37].
Şekil 4. Dönel kalıplı EKAE yönteminin şematik resmi [38].
3. EKAE yönteminin IF-çeliklerine uygulanışı ile ilgili literatür bilgileri ve elde edilen sonuçlar
EKAE yöntemiyle IF-çeliğinin prosesi konusunda literatüre geçmiş az sayıda çalışma mevcuttur. Elde edilebilen literatür bilgilerine bakıldığında, bu konudaki ilk çalışma 2000 yılında yapılmıştır [39]. Bu çalışmada IF-çeliği model malzeme olarak seçilmiş ve EKAE prosesi sonrası söz konusu çeliğin tane boyutu 1 µm’nin (submicron) altına indirilebilmiştir. Daha sonra IF-çeliklerinin proses sırasındaki deformasyon davranışı ve tekstür oluşumu, Taylor yaklaşımı ve FEM simülasyonu kullanılarak incelenmiştir [40]. Bu başlangıç çalışmalarından sonra, bu yöntemin ticari anlamda IF-çeliğinin düşük olan mukavemet değerleriyle yorulma dayanımlarının artırılabileceği fikri ortaya çıkmış ve bu yönde çalışmalar başlamıştır. Bu konudaki ilk çalışma Han ve Yue [37] ve Gazder [38] tarafından gerçekleştirilmiştir. Bu çalışmalarda, EKAE yöntemiyle proses edilen IF-çeliklerinin yapısal ve mekanik özelliklerinde meydana gelen değişimler incelenmiştir. Özellikle Gazder [38] tarafından yapılan çalışmada, proses sonrası IF-çeliklerinin mukavemet değerlerinin önemli oranda arttığı gözlenmiştir. Bundan sonra gerçekleştirilen iki çalışmada [39-40], IF-çeliğinin haddeleme+EKAE kalıbından geçirme işlemleri birleştirilmiş (continuous confined strip shearing) ve proses sonrası oluşan yapısal değişimler incelenmiştir. Bu çalışmalar, özellikle otomobil paneli üretimi için IF-çeliğinin sürekli üretimine izin verebilecek bir kompozisyon olarak görülmektedir. Bu sayede IF-çeliğinin haddelenirken aynı zamanda EKAE prosesinden de geçirilecek ve böylece ultrakristalin yapılı hale getirilmiş üstün mukavemetli sac malzemeler elde edilebilecektir. Bu çalışmaların birinde [39] EKAE prosesi öncesi 282 MPa çekme dayanımı, proses sonrası 442 MPa değerine çıkarılmıştır. Öte yandan proses edilen IF-çeliği 26 oranında kopma uzaması sergilemiştir. Bu konudaki çalışmalara son iki yılda da devam edilmiştir. Messemaeker ve arkadaşları [41] tarafından yapılan bir çalışmada, IF-çeliğinin mukavemet artışına neden olan ince tane yapısı ve tane sınırlarının durumu (küçük ve büyük açılı tane sınırlarının mukavemete katkısı) araştırılmıştır. Aynı zamanda bu çalışmada, proses sonrası termal kararlılık durumu da araştırılmış ve çalışma şartlarında önemli bir tane irileşmesinin oluşmadığı gözlenmiştir. 2005 yılı içerisinde gerçekleştirilen iki çalışmada [42-43] ise, EKAE rotalarının IF-çeliğinde tekstür oluşumu ve tane incelmesi üzerindeki etkileri araştırılmış ve en uygun rota belirlenmeye çalışılmıştır.
Bu alışmalardan elde edilen ilk sonuçlar, IF-çeliği için çok önemli olup bu çeliğin yakın gelecekte başta otomobil endüstrisi olmak üzere pek çok sektör için önemli bir girdi malzemesi olacağını göstermektedir. Ayrıca, üstün mukavemet ve süneklik değerleri gerektiren gelişmiş uygulamalar için de vazgeçilmez bir malzeme olma ihtimali vardır. Çünkü mukavemetin artması, özgül mukavemet değerinin de artmasına neden olacağı için bu malzeme ile çok daha hafif yapıların gerçekleştirilmesi mümkün olabilecektir. Bu ise özellikle otomobil sektörü için çok önemli bir gelişme olup, söz konusu malzeme kullanılarak yüksek dayanımlı ve karmaşık şekilli hafif parçalar üretilebilecektir.
4. Yapılan ön çalışmalar ve elde edilen sonuçlar
I. Karaman tarından IF-çeliğinin EKAE ile proses edilmesi konusunda bir ön çalışma gerçekleştirilmiştir. Bu çalışmada, IF-çeliğinin proses öncesi ve sonrası, yapısal ve mekanik özellikleri karşılaştırmalı olarak incelenmiştir. Bu çalışmadan elde edilen bazı sonuçlar aşağıdaki şekillerde verilmiştir. Şekil 5’de, IF-çeliğinin EKAE prosesi ile içyapısında meydana gelen değişimler gösterilmiştir. Bu şekilden görüldüğü gibi, proses öncesi mikroyapı (Şekil 5(a)), düşük dislokasyon yoğunluğuna sahip iri ferrit tanelerinden (70µm) oluşmaktadır. Tane yapısı EKAE kalıbı kullanılarak gerçekleştirilen birinci pasodan sonra incelmektedir (Şekil 5(b)). Sonraki pasolar mikroyapının daha homojen hale gelmesini sağlamakta ve 8 paso sonrası yönlenmiş tanelerden oluşan ultrakristalin yapı ortaya çıkmaktadır (Şekil 5(c-d)).
Söz konusu çalışmada, IF-çeliğinin mekanik özellikleri de incelenmiş olup, elde edilen gerçek gerilme-gerçek birim uzama eğrileri Şekil 6’da verilmiştir. Bu şekil incelendiğinde, IF-çeliğinin çekme mukavemetinin EKAE prosesiyle hızlı bir şekilde artarak 8 paso sonrası başlangıç değerinin yaklaşık 2.5 kıtana ulaştığı gözükmektedir. Ayrıca, gerçek uzama değerinin ise fazla değişmediği gözlenmektedir. Bu durum, yüksek mukavemetli ve şekillendirilebilir IF-çeliği üretimi için önemli bir sonuçtur. Bu güne kadar IF-çelikleri üzerine yapılan çalışmalarda süneklik değerlerini düşürmeden mukavemet değerlerinde bu oranda bir artış elde edilememiştir. Bu sonuç, özellikle otomobillerde kullanılan yapısal parçalarda ve panel imalatında IF-çeliği kullanılarak daha dayanıklı ve daha hafif yapıların oluşturulabileceğini göstermektedir. Bu ise otomobillerde daha az yakıt tüketimi ve enerji tasarrufu anlamına gelmektedir.
Öte yandan, mühendislik uygulamalarında kullanılan malzemelerin yorulma davranışları da çok önemli bir parametre olarak karşımıza çıkmaktadır. Bu nedenle, yapılan ön çalışmalarda IF-çeliğinin kısa ömürlü yorulma davranışı da incelenmiş olup, elde edilen sonuçlardan bazıları Şekil 7’de verilmiştir. Bu şekilden görüldüğü gibi, IF-çeliğinin yorulma ömrü mukavemet değerlerinde olduğu gibi ECAE prosesi sonrası artmış ve rota Bc’de gerçekleştirilen 8 pasoluk ECAE prosesi sonrası yaklaşık iki katına çıkmıştır. Basit bir prosesle mukavemet ve yorulma değerlerinde elde edilen bu olağan üstü artışlar, IF-çeliğinin sadece panel tipi koruyucu sac (otomobillerde gövde sacları gibi) malzemesi olarak değil, aynı zamanda yapısal parçaların (yük taşıyıcı parçalar) imalatında da kullanılabileceğini göstermiştir.
Şekil 5. ECAE yöntemiyle proses edilen IF-çeliğinin iç yapısında meydana gelen değişimleri gösteren TEM fotoğrafları. (a) Proses öncesi iri ferrit tanelerinden oluşan içyapı, (b) ilk paso sonrası elde edilen içyapı, (c) ikinci ve (d) 8. paso sonrası meydana gelen uzamış ultrakristalin tanelerden oluşan içyapı.
Şekil 6. EKAE yöntemiyle proses edilen IF-çeliğinin proses öncesi ve sonrası gerçek gerilme-gerçek birim uzama eğrilerini gösteren diyagram. (1A: numune döndürmeden bir paso yapılmış; 2B: numene proses arasında 180 çevrilerek 2 paso gerçekleştirilmiş; 8C: pasolar arasında numune 180 çevrilerek 8 paso gerçekleştirilmiş; 8E:C ve B rotaları birleştirilerek numuneye 8 paso uygulanmış).
Şekil 7. EKAE yöntemiyle ultrakristalin yapılı hale getirilen IF-çeliğinin farklı rota ve paso sayılarındaki gerilme-çevrim sayısı eğrileri (t/2=0.3 ve deformasyon hızı= 6x10-3 s-1).
1. Sonuçlar
1. APD yöntemlerinden biri olan EKAE metodu kütlesel formda ultrakristalin yapıya sahip malzemelerin üretilmesinde hızla gelişen bir yöntemdir.
2. Düşük mukavemet değerleri nedeniyle daha çok koruyucu saç malzemesi olarak kullanılan IF-çeliği, olumsuzluklarının giderilmesiyle yük taşıyıcı yapısal parçaların da imalatında kullanılabilir.
3. EKAE ile proses edilen IF-çelinin mukavemet değerleri iki katına varan oranlarda artırılabilmektedir.
4. EKAE yöntemi IF-çeliğinden üretilen saç malzemelere de uygulanmasıyla elde edilebilecek yüksek mukavemet ve süneklik değerlerine sahip saclar özellikle hafifliğin önemli olduğu uygulamalarda yaygın olarak kullanılabilir.
Teşekkür
Bu çalışma, TÜBİTAK Mühendislik Araştırma Grubu (MAG) tarafından 104M289 kod nolu proje kapsamında desteklenmiştir.
Yararlanılan Kaynaklar
[1]. M. Furukawa, Z. Horita, M. Nemoto and T.G. Langdon, “Review: Processing of metals by equal-channel angular pressing”, Journal of Materials Science, vol. 36, pp. 2835-2843, 2001.
[2]. L. Cisar, Y. Yoshida, S. Kamado, Y. Kojima and F. Watanabe, “Development of high strength and ductile magnesium alloys for automobile applications”, Materials Science Forum, vol. 419-422, pp. 249-254, 2003.
[3]. R.Z. Valiev, I.V. Alexandrov, Y.T. Zhu and T.C. Lowe, “Paradox of strength and ductility in metals processed by severe plastic deformation”, Journal of Materials Research, vol. 17, no. 1,pp. 5-8, 2002.
[4]. W.J. Kim, C.W. An, Y.S. Kim and S.I. Hong, “Mechanical properties and microstructures of an AZ61 Mg alloy produced by equal channel angular pressing”, Scripta Materialia, vol. 47, pp. 39-44, 2002.
[5]. V.V. Stolyarov, Y.T. Zhu, T.C. Lowe and R.Z. Valiev, “Microstructure and properties of pure Ti processed by ECAP and cold extrusion” , Materials Science and Engineering A, vol. 303A, pp. 82-89, 2001.
[6]. S.R. Agnew, J.A. Horton, T.M. Lillo and D.W. Brown, “Enhanced ductility in strongly textured magnesium produced by equal channel angular processing”, Scripta Materialia, vol. 50, pp. 377-381, 2004.
[7]. A.Vinogradov and S. Hashimoto, “Fatigue of severely deformed metals”, Advanced Engineering Materials, vol. 5, pp. 351-358, 2003.
[8]. H.-K. Kim, M.-I. Choi, C.-S. Chung and D. H. Shin, “Fatigue properties of ultrafine grained low carbon steel produced by equal channel angular pressing”, Material Science and Engineering A, vol. 340A, 243-250, 2003.
[9]. H.J.Maier, P.Gabor, N. Gupta, I. Karaman and M. Haouaoui, “Cyclic stress-strain response of ultrafine grained copper”, International Journal of Fatigue, 28 (2006) 243-250.
[10]. H. J. Maier, P. Gabor and I. Karaman, “Cyclic stress-strain response and low-cycle fatigue damage in ultrafine grained copper”, Materials Science and Engineering A, 410-411 (2005) 457-461.
[11]. R.R. Mulyukov and A.I. Pshenichnyuk, “Structure and damping of nanocrystalline metals and alloys prepared by high plastic deformation techniques”, Journal of Alloys and Compounds, vol. 355, pp. 26-30, 2003.
[12]. K. Matsubara, Y. Miyahara, Z. Horita and T.G. Langdon, “Developing superplasticity in a magnesium alloy through a combination of extrusion and ECAP”, Acta Materialia, vol. 51, pp. 3073-3084, 2003.
[13]. V.N.Perevezentsev, V.N Chuvil’deev, V.I. Kopylov, A.N. Sysoev and T.G. Langdon, “Developing high strain rate superplasticity in Al-Mg-Sc-Zr alloys using equal-channel angular pressing”, Ann. Chim. Sci. Mat., vol. 27, no. 3, pp. 99-109, 2002.
[14]. T.L. Tsai, P.L. Sun, P.W. Kao and C.P. Chang, “Microstructure and tensile properties of a commercial 5052 aluminum alloy processed by equal channel angular pressing”, Materials Science and Engineering A, vol. 342, pp. 144-151, 2003.
[15]. J.-Y. Chang and A. Shan, “Microstructure and mechanical properties of AlMgSi alloys after equal channel angular pressing at room temperature”, Materials Science and Engineering A, vol. 347, pp. 165-170, 2003.
[16]. M.A. Munoz-Morris, C.G. Oca and D.G. Morris, “Mechanical behaviour of dilute Al-Mg alloy processed by equal channel angular pressing”, Scripta Materialia, vol. 48, pp. 213-218, 2003.
[17]. O.V.Mishin, D.J. Jensen and N. Hansen, “Microstructure and boundary populations in materials produced by equal channel angular extrusion”, Materials Science and Engineering A, vol. 342A, pp. 320-328, 2003.
[18]. I. Kim, J. Kim, D.H. Shin, C.S. Lee and S.K. Hwang, “Effect of equal channel angular pressing temperature on deformation structure of pure Ti”, Materails Science and Engineering A, vol. 342, pp. 302-310, 2003.
[19]. D.H. Shin, I. Kim, J. Kim and Y.T. Zhu, “Shear strain accommodation during severe plastic deformation of titanium using equal channel angular pressing”, Materials Science and Engineering A, vol. 334A, pp. 239-245, 2002.
[20]. V.V. Stolyarov, Y.T. Zhu, T.C. Lowe and R.Z. Valiev, “Microstructure and properties of pure Ti processed by ECAP and cold extrusion”, Materials Science and Engineering A, vol. 303A, pp. 82-89, 2001.
[21]. W.J. Kim, C.W. An, Y.S. Kim and S.I. Hong, “Mechanical properties nad microstructures of an AZ61 Mg alloy produced by equal channel angular pressing”, Scripta Materialia, vol. 47, pp. 39-44, 2002.
[22]. A. Vinogradov, V. Patlan, Y. Suzuki, K. Kitagawa and V.I. Kopylov, “Structure and properties of ultra-fine grain Cu-Cr-Zr alloy processed by equal-channel angular pressing”, Acta Materialia, vol. 50, pp. 1639-1650, 2002.
[23]. T. Yamasaki, H. Miyamoto, T. Mimaki, A. Vinogradov and S. Hashimoto, “Stress corrosion cracking susceptibility of ultra-fine grain copper produced by equal-channel angular pressing”, Materials Science and Engineering A, vol. 318A, pp. 122-128, 2001.
[24]. K. Neishi, T. Uchida, A. Yamauchi, K. Nakamura, Z. Horita and T.G. Langdon, “Low-temperature superplasticity in a Cu-Zn-Sn alloy processed by severe plastic deformation”, Materials Science and Engineering A, vol. 307A, pp. 23-28, 2001.
[25]. M. Haouaoui, I. Karaman, H. J. Maier and K. T. Hardwig, “Microstructure evolution and mechanical behavior of bulk copper obtained by consolidation of micro-and nanopowders using equal channel angular extrusion”, Metallurgical and Materials Transactions A, 35A (2004) 1-15.
[26]. Y. Li and T.G. Langdon, “Equal-channel angular pressing of an Al-6061 metal matrix composite”, Journal of Materials Science, vol. 35, pp. 1201-1204, 2000.
[27]. G. G. Yapici, I. Karaman, Z.P. Luo, H. J. Maier and Y.I. Chumlyakov, “Microstructural refinement and deformation twinning during severe plastic deformation of 316L stainless steel at high temperatures”, Journal of Materials Research, 19(8) (2004) 2268-2278.
[28]. I. Karaman, A. V. Kulkarni and Z. P. Luo, ”Transformation behavior and unusual twinning in a NiTi shape memory alloy oustforming using equla channel angular extrusion”, Philosophical magazine, 85 (16) (2005) 1729-1745.
[29]. I. Karaman, H.E. Karaca, H.J. Maier and Z. P. Luo, “The effect of severe marforming on shape-memory characteristics of a Ti-rich NİTi alloy processed using equal-channel angular extrusion”, Metallurgical and Materials Transactions A , 34A (2003) 1-13.
[30]. S.M.L. Sastry and R.N. Mahapatra, “Grain refinement of intermetallics by severe plastic deformation”, Materials Science and Engineering A, vol. 329A-331A, pp. 872-87, 2001.
[31]. J. Robertson, J.T. Im, I. Karaman, K.T. Hartwig and I.E. Anderson, “Consolidation of amorphous copper based powder by equal channel angular extrusion”, Journal of Non-Crystalline Solids, vol. 317, pp. 144-151, 2003.
[32]. V.M. Segal, V.I. Reznikov, A.E. Dropyshevskiy, V.I. Kopylov, “Plastic working of metals by simple shear”, Russian Metalli., 1 (1981) 99-105.
[33]. R.Z. Valiev, R.K. Islamgaliev, I.V. Alexandrov, Bulk nanostructured materials from severe plastic deformation, Progress in Materials Science, 45 (2000) 103-189.
[34]. Y. Iwahashi, Z. Horita, M. Nemoto and T.G. Langdon, “The process of grain refinement in equal-channel angular pressing”, Acta Materialia, vol. 46, no. 9, pp. 3317-3331, 1998.
[35]. Y. Iwahashi, J. Wang, Z. Horita, M. Nemoto, T.G. Langdon, “Principles of equal-channel angular pressing for the processing ultra-fine grained materials, Scripta Materialia, 35 (1996) 143-146.
[36]. I. Karaman, J. Robertson, T.T. Im, S.N. Mathaudhu, Z.P. Luo and K.T. Hartwig, “The effect of temperature and extrusion speed on the consolidation of zirconium-based metallic glass powder using equal-channel angular extrusion”, Metallurgical and Materials Transactions A, vol. 35A, no.1, pp. 247-256, 2004.
[37]. B.Q.Han, S. Yue, “Processing of ultrafine ferrite steels” Journal of Materials processing Technology, 136 (2003) 100-104.
[38]. A.A. Gazder, I.B. Timokhina, E.V. Pereloma, “Microstructural and Mechanical Properties of IF steel subjected to ECAE”, Materials Science Forum, (2003) 2693-2698.
[39]. Y.Okamura, H. Utsunomiya, T. Sakai, Y. Saito, “Texture and microstructure of ultra-low carbon IF steel strip processed by conshearing”, Journal of the Iron and Steel Institute of Japan, 89(6) (2003) 666-672.
[40]. Y.H. Jim, M.Y. Huh, Y.H. Chung, “Evolution of texture and microstructures in IF-steel sheets during continuous confined strip shearing and subsequent recrystallization annealing”, Journal of Materials Science, 39 (2004) 5311-5314.
[41]. J.De Messemaeker, “On the strength in submicron IF steel”, Materials Letters, 58 (2004) 3782-3786.
[42]. J De Messemaeker, B. Verlinder, J.Van Humbeeck, , “Texture of IF steel after equal channel angular pressing”, Acta Materialia, 53(2005) 4245-4257.
[43]. S.Li, A.A. Gazder, I.J. Beyerlein, E.V.Perelome, C.H.J. Davies, “Effect of processing route on microstructure and texture development in equal channel angular extrusion of interstitial-free steel”, Acta materialia, (2005), in pres.
. . .
İçerik sadece atıfta bulunularak yayınlanabilir: Sivas İş Dünyası. Editöryal görüş, yazarın görüşüne aykırı olabilir.