Elektrik Ark Fırınlarında Kullanılan Hurdaya Alternatif Hammaddeşer
Türkiyede 2006 yılında 23,3 milyon ton çelik üretilmiş olup bu üretimin yaklaşık 16,5 milyon tonu elektrik ark fırınlı tesislerde gerçekleştirilmiştir
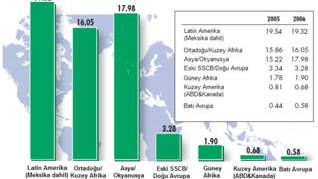
Türkiyede 2006 yılında 23,3 milyon ton çelik üretilmiş olup bu üretimin yaklaşık 16,5 milyon tonu elektrik ark fırınlı tesislerde gerçekleştirilmiştir
Türkiye’de 2006 yılında 23,3 milyon ton çelik üretilmiş olup bu üretimin yaklaşık 16,5 milyon tonu elektrik ark fırınlı tesislerde gerçekleştirilmiştir. Ülkemiz hurda kaynaklarının yetersiz olması nedeni ile gerekli hurda büyük oranda ithalat yolu ile karşılanmaktadır. Ülkemizin 2006 yılındaki hurda ithalatı 14,77 milyon ton olarak gerçekleşmiştir. Bu ithalatın parasal karşılığı ise 3,83 milyar dolardır. Günümüzde elektrik ark fırınlarında çelik üretiminde hurda yerine kullanılabilecek alternatif hammaddelere olan ilgi giderek artmakta ve sünger demir kullanımı cazip hale gelmektedir.
Dünya sünger demir üretimi son yıllarda büyük artış göstermiş ve 2006 yılında 59,8 milyon ton olarak gerçekleşmiştir. Bu üretimin 19,7’si katı redükleyici, 80,3’ü gaz redükleyici kullanılan yöntemlere aittir. Bu çalışmada, 1970’li yıllarda üretimine başlanan sünger demir üretiminin bugünkü durumu, üretim yöntemleri, proseslere ve bölgelere göre dağılımı irdelenmiştir. Klasik sünger demir üretim yöntemlerinin yanı sıra, döner hazneli fırın prosesleri olan Fastmet, ITmk3 yöntemleri tanıtılmıştır.
Anahtar sözcükler: Sünger Demir, Elektrik Ark Fırını, Hurda, Metalik Demir Taneleri
1. GİRİŞ
Günümüzde 1,244 milyar ton olan dünya sıvı ham çelik üretiminin 65,5’i entegre tesislerde, 32’si ise elektrik ark fırınlarında gerçekleştirilmektedir [1]. Türk demir çelik sektörü 2006 yılında, her birinin yıllık kapasitesi 200 bin ton ile 3,5 milyon ton arasında değişen üç adet entegre tesis ve 17 adet elektrik ark fırınlı tesiste gerçekleştirdiği, 23,3 milyon ton ham çelik üretimi ile dünya çelik üretiminde 11. Avrupa’da ise 3. sırada yer almıştır. Bu üretim rakamları ile Türkiye, 2005 yılına göre 11,2 oranında bir artışla, 2006 yılında çelik üretimini en çok artıran 15 ülke arasında, Çin’den sonra 2. sırada yer almıştır. Yıllara göre ülkemiz ham çelik üretimi incelendiğinde entegre tesislerin toplam üretimdeki payının 1990 yılından itibaren düşüş gösterdiği, elektrik ark fırını ile çalışan tesislerin toplam üretimdeki payının ise hızlı bir şekilde arttığı görülmektedir. Ülkemiz ham çelik üretim kapasitesi 27,6 milyon ton olup bu kapasitenin 76,5’una karşılık gelen 21,1 milyon tonu 17 adet elektrik ark fırınlı tesise aittir. 2006 yılında, ülkemiz çelik üretiminde elektrik ark fırınlarının payı ise 70,8 olup, üretimin 16,496 milyon tonu elektrik ark fırınlı tesislerde gerçekleştirilmiştir [2].
2000 yılında 366,9 milyon ton olan dünya hurda tüketimi ark fırınlı tesislerin üretimdeki payının artmasına paralel olarak artış göstermiş ve 2005 yılında 441,5 milyon ton seviyelerine ulaşmıştır. En büyük hurda tüketimi gerçekleştiren ülkeler incelendiğinde bu ülkelerin dünya çelik üretiminde üst sıralarda bulunan ülkeler olup başlıca; Çin, ABD, Japonya, Güney Kore, İtalya, Almanya ve Türkiye’den oluştuğu görülmektedir [1-3].
2000 yılında 7,4 milyon tonluk toplam hurda ithalatı gerçekleştiren Türkiye, 2006 yılında, 14,77 milyon tonluk kısmını ithalat yoluyla karşılayarak dünyada en büyük hurda ithalatçısı konumunda yer almıştır. Ülkemiz demir çelik sektörü hurda ihtiyacının 75’ini dış ülkelerden karşılamaktadır. 2000 yılında toplam hurda tüketiminin yaklaşık 17’sini (5,1 milyon ton) ithalat yoluyla karşılayan Çin’in günümüzde toplam hurda tüketiminde ithalatın payında herhangi bir değişme olmamasına karşın, 2002 yılından itibaren ham çelik üretimini hızlı bir şekilde arttırması sonucunda hurda ithalatını 10,1 milyon tona çıkararak en çok hurda ithal eden ikinci ülke konumunda yer almıştır. Türkiye ve Çin’i takiben diğer büyük hurda ithalatçısı ülkelere bakıldığında Belçika’nın 2005 yılında 7,7 milyon ton hurda ithalatı gerçekleştirdiği, İspanya’nın dış alımının günümüzde 7,0 milyon ton seviyelerinde olduğu görülmektedir. Güney Kore’nin 2005 yılında toplam hurda ithalatı önceki yıllara oranla önemli bir değişiklik göstermemiş ve 6,8 milyon tonluk ithalat değeri ile İtalya (5,4 milyon ton) ve Almanya (5 milyon ton) gibi ülkelerle birlikte en çok hurda dış alımı yapan ülkeler arasında yer almıştır [1-3].
Günümüzde elektrik ark fırınlarında çelik üretiminde hurda yerine kullanılabilecek alternatif hammaddelere olan ilgi giderek artmaktadır. Yüksek fırınlarda kullanılamayan cevherler ve koklaşamayan kömürleri değerlendirmek amacıyla bugüne kadar çok sayıda proje geliştirilmiştir. Bu projeler arasında üzerinde en çok çalışılan teknoloji; Doğrudan İndirgenmiş Demir cevheri (Direct Reduced Iron - DRI) teknolojisidir. Geleneksel entegre demir - çelik tesislerinin uzun kuruluş süresi ve büyük yatırım gerektirmesi, kok üretimine elverişli kömürlerin miktarı ve kalitesinin azalması ayrıca fiyatlarının yükselmesi, hurda kalitesinin gittikçe düşmesi; buna karşılık hurda fiyatlarında görülen artış, yeterli miktarda hurda bulamama sorunu, kaliteli çeliğe olan ihtiyaç sonucu yüksek mukavemetli çeliklerin üretilmesiyle beraber hurda geri dönüş süresinin uzaması, sünger demir ürününün kara ve deniz ulaşımı ile kolay ve zarar görmeden taşınabilmesi, gibi etkenler sebebiyle sünger demir üretimi ve kullanımı günümüzde oldukça cazip hale gelmektedir [4].
Türkiye açısından konunun önemi ise, günümüzde ve gelecekte çelik üretiminin büyük oranda hurdaya dayalı olarak gerçekleştirilecek olması ve günümüzde gerekli hurdanın büyük oranlarda ithalat yolu ile karşılanmasından açıkça görülmektedir. Dünya hurda piyasasının en önemli müşterilerinin başında gelen ülkemizde yerli kaynaklar kullanılarak sünger demir üretimi büyük önem arz etmektedir. Mevcut demir cevheri ve linyit kömürü yatakları kullanılarak, ülkemizde sünger demir üretiminin gerçekleştirilmesi mümkündür. Kurulacak bir sünger demir tesisi, çelik üretim fırınlarına kaliteli şarj maddeleri sunacak ve aynı zamanda hurdada dışa bağımlılığı azaltacaktır.
Bu çalışmada ülkemiz açısından büyük önem arz eden sünger demir üretiminin bugünkü durumu, üretim yöntemleri, proseslere ve bölgelere göre dağılımı incelenmiştir. Ülkemiz hammadde kaynaklarını ve demir-çelik tesislerinden açığa çıkan demir içerikli katı atıkları değerlendirmek için uygun olan döner hazneli fırın prosesleri (Fastmet, ITmk3) tanıtılmıştır.
2. DÜNYA SÜNGER DEMİR ÜRETİMİ
Sünger demir, demir cevheri veya peletlerin katı veya gaz redükleyici kullanarak ergime olmaksızın metalik demire redüklenmesi sonucu elde edilen üründür. Yüksek metalizasyon derecesine sahip bu ürün, gözenekli yapıda olup, kararlı bir bileşime sahiptir. Kullanılan hammaddeye bağlı olarak belli bir miktar gang ihtiva eden sünger demir, bünyesinde iz elementlerinin düşük olması nedeni ile kaliteli hurdanın yerine alternatif hammadde olarak elektrik ark fırınlarında ve ayrıca bazik oksijen fırınlarında şarj malzemesi olarak kullanılmaktadır.
Dünya sünger demir üretiminin 1970 – 2006 yılları arasındaki gelişimi Şekil 1’de gösterilmektedir.
Şekil 1: Yıllara Göre Dünya Sünger Demir Üretimi [5]
Şekil 1’de görüldüğü gibi dünya sünger demir üretimi yıllara göre düzenli bir artış göstermektedir. 1993 yılında 23,65 milyon ton olan sünger demir üretimi 2000’li yıllara gelindiğinde iki katına çıkarak 40 milyon tonluk rakamlara ulaşmış günümüzde ise 60 milyon ton sınırına dayanmıştır.
Katı redükleyici proses kullanılarak üretilen sünger demirin 75’i Hindistan’da, 16’sı Güney Afrika’da, geri kalanı da Brezilya, Mısır ve İran gibi ülkelerde üretilmektedir. Hindistan sünger demir üretiminde başı çekerken, gün geçtikçe geliştirdiği üretim miktarlarının en önemli sebeplerinden biri zengin kömür ve demir cevheri rezervlerine sahip olmasıdır. Bu nedenle Hindistan katı redükleyici proses tercihiyle kendi linyit ve demir cevheri rezervlerini kullanarak sünger demir üretimi gerçekleştirmektedir.
Hindistan’ın sünger demir üretimi 2001 yılında 5,6 milyon tonun altındayken son beş yıl içinde büyük bir artışla 14,74 milyon tona ulaşmıştır. Latin Amerika ülkelerinden Venezuela ve Meksika sünger demir üretiminde başı çeken diğer ülkeler olup 2006 yılında sırasıyla 8,61 ve 6,17 milyon tonluk üretim gerçekleştirmişlerdir. Bu ülkelerde doğalgaz rezervlerinin fazlalığı göze çarpmakta ve bu nedenle redükleyici olarak doğalgaz kullanan proseslerle sünger demir üretiminde bu ülkelerin ilk sıraları aldıkları görülmektedir [6]. Dünya sünger demir üretiminin bölgelere göre dağılımı Şekil 2’de verilmiştir.
Şekil 2: Bölgelere göre 2006 yılı sünger demir üretimi (Mt) [5]
Şekil 2’de dünya sünger demir üretiminin özellikle bol ve ucuz enerji kaynağına sahip olan bölgelerde yoğunlaştığı görülmektedir. Latin Amerika ülkeleri zengin doğalgaz kaynaklarına sahip olduğu için sünger demir üretim kapasitesi diğer bölgelere kıyasla çok daha fazladır. En büyük sünger demir üretici ülkeler sırasıyla; Hindistan, Venezuela, İran, Meksika, Suudi Arabistan, Rusya ve Mısır’dan oluşmaktadır.
59,8 milyon ton olan 2006 yılı dünya toplam sünger demir üretiminin 59,7’sini gaz redükleyici kullanan Midrex prosesi oluştururken, katı redükleyici prosesler 19,7’lik oranı ile ikinci sırada, diğer bir gaz redükleyici kullanan HyL prosesleri ise 18,4 payla üçüncü sırada yer almaktadır. Geri kalan 2,2’lik oran ise Finmet ve diğer gaz redükleyici kullanan proseslere aittir. 2006 yılı itibari ile sünger demir üretiminin proseslere göre dağılımı Şekil 3’te gösterilmiştir.
Şekil 3: 2006 Proseslere göre dünya sünger demir üretimi [5]
Tablo 1’de 2000 – 2006 yılları arasında dünya sünger demir üretiminin yöntemlere göre üretim rakamları verilmiştir. Tablo 1’de görüldüğü gibi dünya sünger demir üretiminin çok büyük bir kısmı gaz redükleyici kullanılan yöntemler tarafından gerçekleştirilmektedir. Günümüzde sünger demir üretiminde kullanılan yöntemler; ACCAR, ARMCO, CIRCORED, CODIR, DAV, DRC, FINMET, FIOR, GHAEM, HYL III, IRON CARBIDE, IRON DYNAMICS, JINDAL, KINGLOR-METOR, MIDREX, NSC, OSIL, PLASMARED, PUROFER, SIIL, SL/RN, TISCO olup bu yöntemlerin başında ise Midrex, HyL-III ve SL/RN yöntemleri gelmektedir.
Tablo 1: Proseslere göre dünya sünger demir üretimi (Mt) [5]
Katı redükleyici kullanılan yöntemlerin en önemlisi SL/RN yöntemidir. 2005 yılından 2006 yılına gelindiğinde dünya sünger demir üretiminde meydana gelen artışın temel nedeninin katı redükleyici kullanılan yöntemlerle gerçekleştirilen üretimdeki artıştan kaynaklandığı görülmektedir [4].
3. SÜNGER DEMİR ÜRETİM YÖNTEMLERİ
Sünger demir üretim yöntemleri kullanılan redükleyici türüne göre iki ana gruba ayrılır;
1. Gaz redükleyici kullanılan yöntemler
2. Katı redükleyici kullanılan yöntemler
Dünyada mevcut sünger demir üretim yöntemleri ve bu yöntemlerde kullanılan fırın, redükleyici ve cevher türü Tablo 2’de özetlenmektedir.
Tablo 2: Sünger demir üretim yöntemleri [7]
Redükleyici Yöntem Fırın Türü Cevher Türü
Gaz HYL-III, Midrex Düşey Fırın
Pelet ve Parça Cevher
Fior Akışkan Yatak
Kömür SL/RN, CODIR, DRC Döner Fırın
Fastmet/Fastmelt Döner Hazneli Fırın Parça Cevher ve Atık
3.1 Gaz Redükleyici Kullanılan Yöntemler
Gaz redükleyicilerin kullanıldığı yöntemler ile dünya sünger demir üretiminin 80,3’ü gerçekleştirilmektedir. Yöntemin kolay kontrol edilmesi, proseslerin verimli gerçekleşmesi ve oluşan ürünün yüksek kalitede (karbon oranı 1–3 ve düşük kükürt 0,005) olmasından dolayı gaz esaslı yöntemler daha çok tercih edilmektedir. Gaz redükleyici kullanılan yöntemler arasında en yaygın olanları Midrex ve HyL-III yöntemleridir. Bu yöntemlerde, redüklenme ters akım prensibine göre tasarlanmış düşey şaft fırını kullanılarak yapılmaktadır. Fırının üstünden şarj edilen demir oksitli hammadde aşağı inerken yukarı doğru çıkan H2 ve CO içeren gazlarla aşağı iniş sırasında ısıtılır ve redüklenir. İndirgenmiş sıcak ürün fırının alt bölgesindeki soğutma sistemine alınır.
3.2 Katı Redükleyici Kullanılan Yöntemler
Kömür ve türevleri katı redükleyicilerin kullanıldığı yöntemlerle 2006 yılı verilerine göre 59,79 milyon tonluk dünya sünger demir üretiminin, 11,7 milyon tonluk kısmı yani toplam üretimin 19,7’si gerçekleştirilmiştir [8]. Katı redükleyici ile döner fırında sünger demir üretilen yöntemlerden en önemlisi SL/RN (Stelco – Lurgi/ Republic Steel – National Lead) prosesidir. Bu yöntemde, demir cevheri, kömür ve dolomit yükleme ucundan fırına şarj edilir ve ilk aşamada bir ön ısıtma işlemine tabi tutularak şarj kurutulur. Şarjın kurutulup redüksiyon sıcaklığına ulaşması sağlandığında demir oksitler, oluşan karbon monoksit gazı ile redüklenir. Son 10 yıl içinde gelişme kaydeden diğer bir yöntem döner hazneli fırın teknolojisi kullanan Fastmet yöntemidir. Kurulum ve işletme maliyetleri döner fırınlı sistemlere göre daha düşük olan döner hazneli fırınlar son yıllarda giderek yaygınlaşmaktadır. Bunlardan Fastmet yöntemi ile sünger demir üretimi gerçekleştirilirken, ITmk3 yöntemi ile metalik demir taneleri adı verilen ve özellikleri itibari ile pik demire benzeyen bir ürün açığa çıkmaktadır. Her iki yöntem ülkemiz yerli kaynaklarını değerlendirmek açısından önemli olduğu için aşağıda detaylandırılacaktır.
3.2.1 Fastmet Yöntemi
Fastmet yöntemi esas olarak çelik fabrikalarından açığa çıkan atıkları değerlendirmek amacıyla Midrex tarafından geliştirilmiştir. Bu proses reaktör olarak döner hazneli fırın ve redükleyici olarak katı yakıt kullanmaktadır. Şekil 4’te Fastmet prosesinin akım şeması verilmiştir.
Fastmet prosesinde kullanılan hammaddeler incelendiğinde demirli malzeme olarak yüksek fırın baca tozu, bazik oksijen fırını baca tozu, elektrik ark fırını baca tozu gibi demirli artıkların; redükleyici olarak ise atıklarla beraber gelen karbon, kömür, odun kömürü ve kok kullanılabildiği görülmektedir.
Fastmet prosesinde demirli atıklar, redükleyici ve bağlayıcı malzeme ile karıştırıldıktan sonra peletlenir veya briketlenir. Peletleme işleminden geçen şarj malzemeleri 160 – 180 °C’de kurutulurken, briketleme işlemine tabi tutulan şarj malzemeleri kurutulmadan döner hazneli fırına şarj edilir. Şarj malzemesinin fırın içerisinde kalma süresi 6 – 12 dakika arasındadır. Bu süre zarfında 85 – 95 demir oksit, metalik demire redüklenir. Döner hazneli fırında elde edilen sıcak sünger demirin oksitlenmesini önlemek amacıyla ürün soğutucu tanklara alınıp soğutulabilir, briketlenebilir veya sıvı ham demir üretimi için özel olarak tasarlanmış fırına (Fastmelt prosesi) şarj edilebilir [8].
Fastmet yönteminde elde edilen sünger demirin metalizasyon derecesi 90’ın üzerindedir. Ürünün karbon içeriği ise 3 seviyelerindedir [10].
3.2.2 ITmk3 Yöntemi
ITmk3 yöntemi, Fastmet yöntemi gibi Midrex tarafından geliştirilen bir proses olup, Fastmet yönteminde kullanılan döner hazneli fırına benzer bir fırın üzerine bina edilmiştir. Fırında demir cevheri, kömür ve bağlayıcılardan oluşan kuru ham peletler sıcak metalik demir taneleri (iron nugget) üretmek için redüklenirler. Karıştırma, peletleme ve besleme adımları Fastmet prosesiyle aynı olup döner hazneli fırının son bölgesinde sıcaklık 1350 oC seviyelerine ulaşarak redüklenen cevherin ergimesi ve gangdan kolayca ayrılması sağlanır. Elde edilen metalik demir taneleri fiziksel ve kimyasal açıdan yüksek fırından elde edilen pik demirle benzerlik göstermektedir.
ITmk3 Prosesi hem düşük tenörlü cevherleri, hem konsantreleri, hem de demirli atıkları değerlendirerek sünger demirden daha kullanışlı bir ürün olan metalik demir taneleri haline dönüştürebilmektedir.
Kullanılacak demirli hammadde ve redükleyici konusunda proses oldukça esnektir. Cevher tipinde herhangi bir sınırlama yoktur; cevherler (manyetit ve hematit) veya demirli atıklar (baca tozları, skal ve çamurlar) peletlenerek kullanılabilirler. Peletlerin şaft fırınlarındaki kadar mukavemetli olması gerekmez. Bunun yanı sıra çok çeşitli özellikte kömürler kullanılabilmektedir. İstenen özellikler ise düşük kül ve kükürt içeriğidir. Proseste kömür, kok ve petrol kokuna ilaveten sıvı ve gaz redükleyiciler de ( 10 kül, en az 50 sabit karbon içeren) kullanılabilir [8].
ITmk3 yönteminde elde edilen metalik demir tanelerinin bileşimi incelendiğinde metalik demir içeriğinin 96 – 97 seviyelerinde olduğu, ürünün FeO içeriğinin ise 2’den daha az olduğu görülmektedir. Ürünün karbon içeriği 2,5 – 3,5 arasında değişmekte olup kükürt içeriği ise 0,05 mertebelerindedir [8].
ITmk3 prosesinin konvansiyonel sıvı ham demir üretim teknolojilerine göre çeşitli avantajları vardır. Redüksiyon ve cüruf ayırımı tek kademede oluştuğundan daha az redükleme süresine ihtiyaç duyulur. Çok yüksek proses sıcaklıklara ihtiyaç duyulmaz. Düşük yatırım ve üretim maliyeti gerektirir. Cüruf metal ayrımı iyi olduğundan ürün gang içermez. Ayrıca, cürufta FeO içeriği çok düşük olduğu için refrakter korozyonu azdır.
4. SONUÇ
Üretiminin 71’ini ark fırınlı tesislerle gerçekleştiren ve 85 oranında uzun ürün üreten ülkemiz demir çelik üretim tesisleri gelecekte katma değeri yüksek ürünlere yöneldiğinde seçilmiş hammaddeler kullanmak zorunda kalacaktır. Bu durumda kaliteli hurdaya alternatif olan sünger demir kullanımı bir zorunluluk olacaktır.
Bu nedenle yerli kaynaklarımızı kullanarak sünger demir üretimi ülkemiz açısından çok büyük önem taşımaktadır. Türkiye’de yerli demir cevherleri ve linyit kömürü yatakları kullanılarak sünger demir üretiminin gerçekleştirilmesi mümkün gözükmektedir. Kurulacak bir sünger demir tesisi, çelik üretim fırınlarına kaliteli şarj maddeleri sunacak ve aynı zamanda hurdada dışa bağımlılığı azaltacaktır. Demir çelik üretim tesislerinin bir sorunu olan ancak içerdiği demiroksit nedeni ile ekonomik değere sahip katı atıkların değerlendirilmesi amacı ile Fastmet prosesinin iyi incelenmesi gerekmektedir. Hem geniş rezervlere sahip düşük tenörlü cevherleri, hem konsantreleri, hem de çelik fabrikalarından açığa çıkan atıkları değerlendirerek sünger demirden daha kullanışlı bir ürün olan metalik demir taneleri haline dönüştürebilen ITmk3 prosesinin ülkemiz yerli kaynaklarını değerlendirmek açısından uygun bir proses olduğu görülmektedir.
Bölümümüzde, yerli kaynaklardan yararlanarak sünger demir üretimi konusunda uzun süredir araştırmalar yapılmaktadır. DPT projesi kapsamında sünger demir konusunda yapılan çalışmalarda, Sivas Divriği peletleme fabrikasından elde edilen demir oksit peletlerin farklı kömür tipleri kullanılarak sünger demir üretim koşulları incelenmiştir. Ayrıca kömür tipi sabit tutularak yapılan çalışmalarda geniş rezervlere sahip yerli demir cevherlerimizi değerlendirmek amaçlı olarak Sivas Divriği B Kafa ve Malatya Hekimhan Hasançelebi yöresi yüksek, orta ve düşük tenörlü demir cevherlerinin sünger demir üretimine uygunlukları araştırılmıştır. Soğuk bağlı pelet yöntemi kullanılarak düşük tenörlü cevherlerimizi değerlendirmek amacıyla metalik demir tanelerinin üretilmesi konusunda yapılan çalışmalar ise devam etmektedir.
5. KAYNAKLAR
[1] http://www.worldsteel.org, World Steel in Figures, 2007
[2] Demir Çelik Üreticileri Derneği 2006 Yılı Raporu, 2007
[3] IISI 2002 Edition World Steel in Figures
[4] A.E. Ersundu, “Yerli Demir Cevherlerinin Sünger Demir
Üretimine Uygunluğunun Araştırılması” Yüksek Lisans Tezi,
İ.T.Ü Fen Bilimleri Enstitüsü, 2007
[5] Midrex Technologies Inc., 2006 World Direct Reduction Statics, 2007
[6] Erdemir, “Yerli Cevherlerin Kullanımının Geliştirilmesi Entegre Projesine Yönelik Hindistan’a Yapılan İnceleme Gezisi Raporu”, Kdz. Ereğli, Zonguldak. 2004
[7] S. Aydın, “Dünya sünger demir üretiminin bugünkü durumu”
Metalurji Dergisi, Sayı 6768, 1990, s-41-46
[8] http://www.midrex.com
[9] G. Hoffman, “Waste Recycling with Fasmet and Fastmelt” Direct From Midrex, 2000
[10] J.M. McClelland, E. and Jr.P, “Fastmet: Proven Process for Steel Mill Waste Recovery” 2006
. . .
İçerik sadece atıfta bulunularak yayınlanabilir: Sivas İş Dünyası. Editöryal görüş, yazarın görüşüne aykırı olabilir.