AISI 304-AISI 430 Paslanmaz Çeliklerin Direnç Kaynak Kalitesine Soğuk Deformasyonun Etkisi
Bu çalışmada nokta direnç kaynak yöntemi ile birleştirilen AISI 304 ostenitik ve AISI 430 ferritik farklı paslanmaz çelik
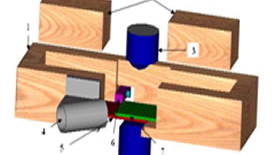
Bu çalışmada nokta direnç kaynak yöntemi ile birleştirilen AISI 304 ostenitik ve AISI 430 ferritik farklı paslanmaz çelik
AISI 304-AISI 430 PASLANMAZ ÇELİKLERİN DİRENÇ KAYNAK KALİTESİNE SOĞUK DEFORMASYONUN ETKİSİ
Ramazan KAÇAR1, Süleyman GÜNDÜZ2,
1 Karabük Üniversitesi Tek. Eğt. Fak. Metal Eğt. Böl. Yüzüncü yıl / Karabük 03704338200 [email protected]
2 Karabük Üniversitesi Tek. Eğt. Fak. Metal Eğt.Yüzüncü yıl/ Karabük-03704338200 [email protected]
ÖZET
Bu çalışmada nokta direnç kaynak yöntemi ile birleştirilen AISI 304 ostenitik ve AISI 430 ferritik farklı paslanmaz çelik sacların kaynaklı birleştirmelerinin kalitesine, malzemenin kaynak öncesi farklı oranlarda maruz kaldığı soğuk deformasyonun etkisinin belirlenmesi amaçlanmıştır. Farklı paslanmaz çelik çifti temin edildiği halde ve farklı oranlarda ( 5, 10 ve 15) soğuk deformasyona uğratıldıktan sonra 7 kA akım şiddetinde 35 çevrim kaynak zamanında, 7 bar elektrot baskı kuvveti uygulanarak birleştirilmiştir. Kaynak kalitesini değerlendirmek için birleştirmenin mikroyapısı incelenerek, çekme makaslama yükü taşıma kapasitesi ve sertlik profili belirlenmiştir. Birleştirmenin mekanik özelliklerinin birleştirilen malzemenin şekil alabilirliğine bağlı olduğu bulunmuştur.
Anahtar Sözcükler: Direnç kaynağı, Soğuk deformasyon, Ostenitik ve ferritik paslanmaz çelik,
1. GİRİŞ
Çeliklere paslanmazlık özelliği veren ana alaşım elamanı kromdur. Paslanmaz çeliklerin kimyasal bileşimlerinde yaklaşık olarak 11-30 arasında krom bulunur. Bu çeliklerde iç yapıyı belirleyen en önemli alaşım elemanları kromun yanı sıra nikel, molibden ve mangandır. Yalnızca krom ihtiva eden ferritik paslanmaz çelikler ısıl işlemle sertleştirilemezler ancak birçok kaynak yöntemi ile birleştirilebilirler. Fakat tane irileşmesi sebebiyle tokluktaki azalmadan dolayı şekillendirilebilirliğin önemli olduğu yerlerde ferritik paslanmaz çeliklerin kaynaklı birleştirilmesi çok istenilen bir durum değildir [1-3]. Kimyasal bileşimlerinde kromun yanı sıra nikelde bulunan, ısıl işlemle sertleştirilemeyen, kaynak edilebilirlikleri iyi olan ve endüstride en geniş kullanım alanına sahip çelikler ise ostenitik paslanmaz çeliklerdir. Taneler arası korozyona karşı hassaslaşma ostenitik paslanmaz çeliklerin kaynaklı birleştirmelerinde karşılaşılan önemli bir sorundur [1-3].
Endüstride geniş kullanım alanına sahip paslanmaz çelikler üretim sırasında ticari olarak temin edildikleri halde kullanılabildikleri gibi bazen fabrikasyon uygulamalarında soğuk plastik şekillendirmeye maruz kalırlar. Soğuk plastik şekillendirme malzemenin dayanımını ve sertliğini arttırır. Çalışma sertleşmesi olarak bilinen bu olay dayanım arttırma mekanizmalarından birisidir. Ancak çeliklerin kırılmaya karşı dayanımının önemli ölçüm parametrelerinden olan şekillendirilebilirlik çalışma sertleşmesinden olumsuz etkilenir [4,5].
Soğuk şekillendirme ile kazanılan mukavemet ve sertlik artışı termal süreçlerden olumsuz etkilenir. Kaynaklı birleştirmelerde termal süreç içerdiği için, birleştirmenin ergitmenin oluşmadığı ancak malzemenin mikroyapısının ve özelliklerinin önemli derecede değiştiği sıcaklık aralıklarında çalışma sertleşmesi ile kazanılan özelliklerde bir değişim olması kaçınılmazdır [6-8]. Bu durum kaynaklı birleştirmelerinin yeniden kristalleşmenin ve tane büyümesinin oluştuğu ısı tesiri altındaki bölgesinin (ITAB) ana metalden daha zayıf oluşmasına sebep olmaktadır.
Örneğin mutfak eşyalarından ostenitik paslanmaz çelik tencereler extrüzyon işlemine tabi tutularak üretilmektedirler. Deformasyona uğramış gövdelere ferritik paslanmaz çelik sap ve tutamaçların birleştirilmesi zaruri ihtiyaç olarak çıkmaktadır. Diğer bir ifadeyle soğuk deformasyona uğrayan farklı paslanmaz çelik saçların birbirleri ile birleştirilmesi endüstride sıkça rastlanan bir durumdur. Günümüzde sac levhaların birleştirilmesinde en yaygın kullanım alanına sahip olan yöntem direnç kaynağıdır. İlave metal kullanılmaması sağladığı hafiflik, yüksek kaynak mukavemeti, estetiklik, özel beceri gerektirmemesi ve kaynak hızının yüksek oluşu direnç kaynak yönteminin önemli avantajlarındandır [9-12]. Kaynak işlemindeki termal sürecin derecesine bağlı olarak ticari olarak temin edildiği halde veya soğuk deformasyonla dayanım kazandırıldıktan sonra birleştirilen farklı paslanmaz çeliklerin ısı tesiri altındaki bölgesinde ve kaynak bölgesinde yapısal başarısızlıklar ortaya çıkabilir.
Bu çalışmada AISI304-AISI430 farklı paslanmaz çeliklere kaynak öncesi uygulanan soğuk deformasyonun nokta direnç kaynak kalitesine etkisi araştırılmıştır. Kaynak kalitesine etki eden parametrelerden dayanım, nüfuziyet, kaynak çekirdeği boyutu, mikro kusurlar metalografik incelemelerle ve mekanik test ölçüm yöntemleri kullanılarak belirlenmiştir.
2. DENEYSEL YÖNTEM
2.1. Deney Numunelerinin Hazırlanması
Çalışmada kimyasal bileşimleri Tablo 1’de verilen AISI304 ostenitik ve AISI430 kalite ferritik paslanmaz çelik saclar kullanılmıştır.
Numuneler 2x30x200mm boyutlarında kesilerek yüzeylerindeki atıklardan temizlenmiştir. Malzemenin ticari olarak temin edildiği halde kaynaklı birleştirmesinin özelliklerini tespit edebilmek amacıyla her bir kaynak zamanı için beş çift numune oluşacak şekilde 2x30x100 mm boyutlarında birleştirme için hazır hale getirilmiştir.
Soğuk deformasyonun birleştirmenin özellikleri üzerinde etkisini tespit edebilmek amacıyla 2x30x200mm boyutunda kesilen malzemeler her bir deformasyon oranı için (5, 10 ve 15) 5 adet olmak üzere toplam 15 adet numune SHIMADZU marka çekme cihazında çenelerin hareketi doğrultusunda deformasyona uğratılmıştır. Şekil 1’de deforme edilmiş numunelerin çekme uzama grafikleri gösterilmiştir.
Şekil 1 (a).Deforme edilmiş malzemelerin çekme uzama grafikleri
Deformasyondan sonra numuneler test cihazının çeneler arasında kalan kısmının tam ortasından kesildikten sonra uzama sonrası değişen boyutu çeneler arasında hasara uğrayan bölümünden oluşmayacak şekilde 100mm boyutunda kesilerek kaynak için hazır hale getirilmiştir.
2.2. Deney Numunelerinin Birleştirilmesi
Deneylerde elektronik akım ve zaman kontrollü, pnömatik basma donanımlı AC nokta direnç kaynak makinesi ve uç çapı 8mm olan su soğutmalı kesik konik uçlu Cu-Cr elektrotlar kullanılmıştır. Numunelerini standart olarak birleştirebilmek, numunelerinin eksenlerinden kaymasını önlemek amacıyla ahşaptan tutucu bir kalıp hazırlanmıştır (Şekil 2a). Ayrıca Şekil 2’ (b) de birleştirme için hazırlanmış numunelerin boyutları ve kaynak pozisyonu gösterilmiştir.
a)
b)
Şekil 2. (a) Ahşap tutucu kalıp, Şekil 2.(b) Deney numunesi boyutları ve kaynak pozisyonu.
Kaynak parametresi olarak; kaynak süresi (35 çevrim) ve kaynak sonrası bekleme zamanı (30 çevrim), seçilmiştir. 1 çevrim 0,02 saniyedir. Elektrot baskı kuvveti 7 bar olarak ayarlanmıştır. Numuneler 7kA akım şiddetinde birleştirilmiştir (Şekil.3).
Şekil 3. (a) Ticari olarak temin edildiği gibi, farklı oranlarda deforme edildikten sonra 35 çevrim kaynak zamanında birleştirilen numuneler.
2.3. Metalografik İnceleme
Klasik metalografi teknikleri ile hazırlanan numuneleri incelemek için 100ml saf su içerisinde 10g oxalik asit bulunan çözeltide hazırlanarak 12V gerilim altında 2A akım şiddetinde 45 saniyelik elektrolitik dağlama uygulanmıştır. Joel 6060LV marka taramalı elektron mikroskobu kullanılarak bağlantının mikroyapısı incelenmiştir. Mikroskoba bağlı XRF ünitesi ile EDS sistemi kullanılarak noktasal element analizi yapılmıştır. Çalışmada ayrıca makroyapı incelemeleri ve çekme makaslama deneyinde ayrılma yüzeylerinin incelenmesinde dijital kamaradan yararlanılmıştır.
2.4. Mekanik Testler
Birleştirmelerden her bir şart için hazırlanan 3’er adet deney numunesi SHIMADZU marka çekme makinesinde 5 mm/dak çekme hızında teste tabi tutulmuştur.
Deformasyonun paslanmaz çelik kaynaklı birleştirmelerinin şekillendirilebilirliğine etkisini tespit etmek amacıyla numunelerin Vickers mikrosertlik ölçüm cihazında sertlikleri ölçülmüştür. 5 ölçüm ortalaması sertlik değeri olarak kabul edilmiştir. Deney işlemi sırasında elmas piramit uca 200 gr yük uygulanmıştır.
3. SONUÇLAR VE İRDELEME
Direnç kaynak kalitesine etki eden en önemli faktörler yüzey görünüşü, dayanım, şekillendirilebilirlik, kaynak çekirdek boyutu, kaynak nufuziyeti, malzeme ayrılma biçimi ve iç kusurlardır [13].
3.1. Soğuk Deformasyonun Mikroyapı Üzerinde Etkisi
Şekil 4’de mukayese yapabilmek amacıyla ostenitik ve ferritik paslanmaz çelik malzemelerin soğuk deformasyona uğradıktan sonra ana malzemenin ve kaynaklı birleştirmesinin mikroyapı görüntüleri görülmektedir. Şekil 4a’de ana malzemelerin soğuk deforme olduktan sonra mikroyapı görüntüleri Şekil 4b’de ise ana malzeme üzerinde tane sınırlarında karbür çökeltileri, Şekil 4c’ ITAB’da yeniden kristalleşen taneler, Şekil 4d’ ITAB’da ergime sınırına yakın kabalaşan taneler ve Şekil 4e’ kaynak çekirdek mikro yapısı görülmektedir.
Şekil 4a’dan görüldüğü gibi ferritik paslanmaz çelik malzemenin mikroyapısı eşeksensel ferrit tanelerinden oluşmaktadır. Ancak. tane içlerinde deformasyonun etkisi olan kayma bantlarının izleri net olarak görülmektedir. Bu kayma bantları yeniden kristalleşen tanelerin oluşması için çekirdeklenme vazifesi görmektedir [6]. Ostenitik ana malzemenin yapısı ise deformasyon doğrultusunda uzamış tanelerden meydana gelmiştir. Bazı taneler içerisinde ikizlenmeler görülmektedir. Şekil 4b’de ise soğuk deformasyona uğradıktan sonra ana malzemenin maruz kaldığı termal sürece bağlı olarak, kaynak çekirdeğinden uzak bölgelerde toparlanma sıcaklığına ulaşılan bölümlerde ana malzeme üzerinde tane sınırlarında karbür çökelmeleri görülmektedir. Bu karbür çökeltileri ferritik paslanmaz ana malzeme ve tane sınırlarında daha fazla olmak kaydıyla, ostenitik ana malzeme üzerinde tane sınırlarında yoğunlaşmaktadır. Toparlanma ile birlikte soğuk deformasyon sırasında kaybedilen elektrik iletkenliğinde bir iyileşmede beklenir.
Şekil 4. Kaynaklı bağlantı mikroyapı profili
Şekil 4c’den görüldüğü soğuk deforme olmuş ferritik ana malzeme üzerinde ITAB’da yeniden kristalleşmiş taneler oluşmuştur. Belirli oranların üzerinde soğuk deformasyona uğrayan metalik malzemelerde termal bir çevrime maruz kalındığında mikroyapıdaki deforme olmuş tanelerde yeni gerilimden arınmış tanelerin kristalleşmesi beklenir. Deformasyon sırasında depolanan gerinim enerjisi yeniden kristalleşme için itici bir güç oluşturmaktadır. Genellikle yeniden kristalleşme sıcaklığı o metalin oK cinsinden ergime katılaşma sıcaklığının 40-50’ne tekabül eder. Yeniden kristalleşme bölgesi artan sıcaklığa, bu sıcaklıkta bekleme zamanına ve soğuk deformasyonun derecesine bağlıdır [6]. Ostenitik ana malzemenin üzerinde ITAB’da yeniden kristalleşme ancak ergime sınırına yakın bir bölgede oluşmuştur. Şekil 4d’den görüldüğü ferritik paslanmaz çelik ana malzemenin ergime sınırına yakın bölgede ITAB’da kabalaşmış taneler görülmektedir. Yeniden kristalleşmenin tamamlanmasıyla taneler büyümeğe başlar. Tane büyümesi için itici güç yüzey enerjisidir. Ancak sistemin yüzey enerjisi toplam tane sınırı azalmasıyla yani diğer bir ifadeyle tanelerin kabalaşması ile mümkündür. Yeniden kristalleşmede olduğu gibi kaynaklı bağlantıda tane irileşmiş bölgenin genişliği üzerinde ulaşılan sıcaklık ve bu sıcaklıkta bekleme süresi önemlidir. Tane büyüklüğü ergime sınırına yaklaştıkça artar. Karbür ve nitrür çökeltileri tane sınırı hareketini engelleyerek tane büyümesini engelleyebilir [6]. Eğer kaynak işlemi sırasında bu çökeltiler çözünmedi ise ITAB’da tane irileşmesine engelleme eğilimi oluşturur. Kaynaklı birleştirmenin ostenitik paslanmaz çelik tarafında ise kaynak çekirdeğine yakın bölgede ise tane irileşmesi gözlemlenmez iken deformasyon sonucu ısıl etkileşim ile yeniden kristalleşme ile tene incelmesi görülmektedir.
Şekil 4e’de olduğu gibi kaynak çekirdeğinde lokal ergimeden dolayı kaba kolonsal taneler oluşmuştur. Ergime bölgesindeki tanelerin kabalaşmasının sebebi ITAB’da iri taneler üzerindeki epitaxial büyümedir. Kaynak çekirdeğinde ise Widmanstatten tipi levhalı bir morfoloji oluşmuştur.
Kaynaklı birleştirmenin mikroyapısı SEM mikroskobu ile incelenerek Şekil 5’de gösterilmiştir.
Şekil 5. Kaynaklı birleştirme mikroyapısı
Şekil 5’den görüldüğü gibi birleştirmenin ITAB’ının ferritik paslanmaz tarafının kaynak çekirdeğine yakın olan bölümlerde ITAB’da tane irileşmesi belirgin olarak görülürken ostenitik paslanmaz tarafında tane irileşmesinden daha ziyade yeniden kristalleşme ile tane incelmesi görülmektedir. Kaynaklı birleştirmelerin çekme makaslama testlerinde ayrılmanın tamamen ferritik paslanmaz tarafında kaba taneli bölümden oluşmasının ana sebebi budur. Ostenitik paslanmaz tarafının kaynak çekirdek boyutları ferritik ile mukayese edildiğinde daha geniş bulunmuştur. Ferritik paslanmaz çeliklerin ısı iletim katsayısının yüksek olması sebebiyle ısı daha hızlı transfer olduğu için daha küçük çekirdek boyutu elde edilmenin sebebi olarak düşünülebilir.
Kaynak çekirdeğinde ise farklı iki paslanmaz çelik çiftinin birleştirilmesi sebebiyle bir lokal ergimenin ve difüzyonun oluştuğu kaynak çekirdeğinde Şekil 5’deki 1 ve 2 nolu bölgelerden yapılan EDS nokta analizleri yapılmıştır. Sonuçlar Şekil 6’ (a) ve (b) de gösterilmiştir.
(a)
(b)
Şekil 6 (a) Şekil 5 deki 1 nolu bölgeden EDS analizi, Şekil 6 (b) Şekil 5 deki 2 nolu bölgeden EDS analizi
Şekil 6 daki EDS analiz sonuçları ostenitik ve ferritik paslanmaz çelik birleştirmelerinin kaynak çekirdeğinde lokal bir ergimenin oluşması sebebiyle feritik-ostenitik dubleks paslanmaz çelik kimyasal bileşimine yakın bir yapı meydana gelmiştir. Kaynak çekirdeğinin ferritik paslanmaz çelik tarafındaki analizde tespit edilen nikel bunun göstergesidir. Bu yapı kaynaklı birleştirmenin dayanımını arttırmaktadır. Nikel miktarı ostenitik paslanmaz çelik tarafına doğruda bir miktar artış göstermektedir. Burada verilmese de ana malzeme üzerinde yapılan EDS analizlerinde fertitik paslanmaz çelik tarafında nikele rastlanmamıştır.
Yüzey görünüşü kaynak kalitesine etki eden parametrelerden biridir. Çalışmada düzgün yuvarlak görünümlü bir yüzey görüntüsü olan birleştirmeler elde edilmiştir. Birleştirme yüzeyinde elektrotların bıraktığı iz kabul edilebilir bulunması homojen uygulanan elektrot baskı kuvvetine atfedilebilir. Çünkü elektrot baskı kuvveti kaynağın görünüşünü etkiler. İyi sonuç almak için elektroda baskı kuvveti paslanmazlar için sade karbonlu çelikler için uygulananın 2–3 katı daha fazla uygulanması önerilir [14].
Birleştirme ayrılma biçimleri kaynak kalitesine etki eden parametrelerden biridir. Çekme makaslama deneyi sonucunda birleştirmelerin ayrılma (kırılma) biçimleri de incelenerek Şekil 7’ de gösterilmiştir.
Şekil 7. Farklı oranlarda deforme edilmiş ve farklı kaynak zamanlarında birleştirilmiş çekme makaslama numunelerinin ayrılma biçimleri
Şekil 7’de görüldüğü gibi, numunelerin genelinde yırtılma şeklinde ayrılma görülmüştür. Yırtılma başlangıcı ferritik paslanmaz çelik tarafında ITAB’da aşırı tane büyümesinin olduğu bölgeden olmuştur. Birleştirmelerin en zayıf bölgesinin burasıdır. Şekil 5 deki mikroyapı görüntüsü de aşırı tane büyümesinin bu bölgede meydana geldiğini göstermektedir. Yırtılma başlangıcının neden bu bölgede meydana geldiğinin kanıtıdır.
3.2. Soğuk Deformasyonun Mekanik Özellikler Üzerindeki Etkisi
Birleştirme kalitesine etki eden parametrelerden mukavemet, çekme makaslama testi uygulanarak belirlenmiştir. Ticari olarak temin edildiği halde ve deformasyona uğradıktan sonra birleştirilen numunelerin çekme makaslama dayanımları grafiksel olarak Şekil 8’ de gösterilmiştir. Grafikte her bir şart için test edilen üç numunenin ortalaması kullanılmıştır.
Şekil 8. AISI304-AISI430 birleştirmelerin çekme makaslama kuvveti sonuçları.
Ticari olarak temin edildiği halde birleştirilen numunelerin çekme makaslama yükü ile mukayese edildiğinde artan deformasyon miktarına bağlı olarak deforme edilmiş numunelerin çekme makaslama yükü taşıma kapasitelerinin bir miktar arttığı bulunmuştur. Bunun kaynak nufuziyeti ile ilgili olduğu düşünülmektedir. Artan deformasyon miktarına bağlı olarak orijinal numune boyutlarında kesitte bir daralma olduğu için sabit ısı girdisi kullanılsa bile daha ince kesitteki malzeme daha fazla ısı girdisine maruz kaldığından daha fazla nufuziyet elde edilmiştir. Makroskopik gözlemler bu sonucu desteklemektedir.
Metalografik inceleme ve EDS sonuçları kaynak çekirdek mikroyapısının dubleks paslanmaz çelik yapısının meydana geldiğini göstermektedir. Dubleks paslanmaz çeliklerin en önemli özellikleri ise dayanımlarının ostenitik ve ferritik paslanmaz çeliklere göre daha yüksek olmasıdır [15]. Çekme makaslama yükü taşıma kapasitelerindeki artışın sebeplerinden biride bu olabilir.
Kaynak kalitesine etki eden unsurlardan biride kaynak çekirdek boyutudur. Deformasyon ile çekirdek boyutu arasındaki ilişki araştırılmıştır. Çalışmada sabit bir ısı girdisi kullanıldığı için kaynak çekirdek boyutlarında deformasyon miktarına bağlı belirgin bir farklılık bulunmamıştır. Kaynak kalitesi ve dayanımı kaynak çekirdek boyutu ve kaynak nufuziyeti ölçerek tahmin edilmeğe çalışılır [14]. Normalde kabul ve tekrar edilebilir bir nokta direnç kaynak birleştirmesi için minimum çekirdek boyutu birleştirilen en ince parçanın 3,5-4 kalınlığında olması istenir [13]. Çalışmada kaynak çekirdek boyutları yaklaşık olarak birleştirilen en ince parçanın 4 katı olarak elde edildiği için kabul edilebilir olarak bulunmuştur. Çalışmada nufuziyet ise malzeme kalınlığının 20-80 arasında tüm birleştirmeler için kabul edilebilir değerlerde bulunmuştur.
Direnç kaynaklı birleştirme kalitesine etki eden parametrelerden şekillendirilebilirlik sertlik ölçümü yapılarak belirlenmiştir. Şekil 9’(a)da ticari olarak temin edildiği halde birleştirilen numunenin sertlik profili Şekil 9’(b)de 15 deforme edildikten sonra birleştirilen numunenin sertlik profili grafiksel olarak gösterilmiştir.
(a)
(b)
Şekil 9. Birleştirmelerin sertlik profili.
Şekil 9’dan görüldüğü gibi, ticari olarak temin edildiği halde birleştirilen numunelerin kaynak çekirdeğinin sertliği ferritik paslanmaz çelik tarafında ostenitik paslanmaz çelik tarafına göre bir miktar yüksek bulunmuştur. 15 deforme edildikten sonra birleştirilen numunenin kaynak çekirdek sertliği ise ostenitik paslanmaz tarafının ferritik paslanmaz tarafına oranla daha yüksek bulunmuştur.
Birleştirmelerin ITAB bölgesinde ise deforme olmamış numunelerde her iki çelik tarafı için düşme görülürken deforme olmuş numunenin ostenitik paslanmaz çelik tarafında da düşüş fakat ferritik paslanmaz çelik tarafında kayda değer bir artış bulunmuştur. Ostenitik paslanmaz çelik tarafındaki sertlik düşüşü tamamen yeniden kristalleşme ile meydana gelen ince taneli yapıyla alakalıdır. Şekil 5’deki metalografik görüntüler bunu desteklemektedir.
Ferritik paslanmaz çelik tarafındaki artış sebeplerinden birincisi ferritik paslanmaz çeliklerin genel karakteristikleri olarak yapılarında karbür çökeltileri bulunması sebebiyle kaynak işlemi sırasında bu karbürlerin daha da büyüyerek ITAB’ da sertliği arttırmış olabilir.
Ferritik yapılarda deformasyonla birlikte dislokasyon yoğunluğunun artması ostenitik yapılara göre daha fazla olması ikinci sebep olarak gösterilebilir. Bu dislokasyon yoğunluğu kendini sertlik olarak gösterecektir. Deforme olmuş ferritik paslanmaz çelik kaynak işlemi sırasında ısı iletim katsayısı daha yüksek olduğu için yeniden kristalleşmeye uğramadan ITAB’da tane irileşmesi meydana geldiği böylece dislokasyon yoğunluğu yüksek kaba tanelerin oluştuğu düşünülmektedir. Bu dislokasyon yoğunluğu fazla tanelerin sertliğinin yüksek olması doğal bir sonuçtur. Deforme olmamış numunede bu durum ITAB’da sertlik düşüşü şeklinde bulunması bu sonucu doğrulamaktadır.
Deforme olmuş ana malzemelerin sertliği deforme olmamışa oranla daha yüksek bulunmuştur. Bu durum soğuk deformasyonun malzemede sağladığı sertlik artışı ile alakalıdır.
4. SONUÇ VE ÖNERİLER
Bu çalışmada yapılan araştırma neticesinde aşağıdaki sonuçlar özetlenebilir;
• Ticari olarak temin edildiği gibi birleştirilen numunelerin çekme makaslama yükü taşıma kapasitesine göre artan deformasyon miktarına bağlı olarak deforme olmuş numunelerin çekme makaslama yükü taşıma kapasitelerinin arttığı bulunmuştur.
• Çekme makaslama numunelerinin numunelerin genelinde yırtılma şeklinde ayrılma görülmüştür. Yırtılma başlangıcı ferritik paslanmaz çelik tarafında ITAB’da aşırı tane büyümesinin olduğu bölgeden olmuştur. Birleştirmelerin en zayıf bölgesinin burasıdır.
• Ticari olarak temin edildiği halde birleştirilen numunelerin kaynak çekirdeğinin sertliği ferritik paslanmaz çelik tarafında ostenitik paslanmaz çelik tarafına göre bir miktar yüksek bulunmuştur. Deforme edildikten sonra birleştirilen numunenin kaynak çekirdek sertliği ise ostenitik paslanmaz tarafının, ferritik paslanmaz tarafına oranla daha yüksek bulunmuştur.
• Birleştirmelerin ITAB bölgesinde ise deforme olmamış numunelerde her iki çelik tarafı için sertlikte düşme görülürken deforme olmuş numunenin ostenitik paslanmaz çelik tarafında da düşüş fakat ferritik paslanmaz çelik tarafında sertlikte kayda değer bir artış bulunmuştur.
• Deforme olmuş ana malzemelerin sertliği deforme olmamışa oranla daha yüksek bulunmuştur. Bu durum soğuk deformasyonun malzemede sağladığı sertlik artışı ile alakalıdır.
• Çalışmada kaynak çekirdek boyutları yaklaşık olarak birleştirilen en ince parçanın 4 katı olarak elde edildiği için kabul edilebilir olarak bulunmuştur. Birleştirmede nufuziyet ise malzeme kalınlığının 20-80 arasında tüm birleştirmeler için kabul edilebilir değerlerde bulunmuştur.
• Mikroyapı incelendiğinde birleştirmenin ITAB’ının ferritik paslanmaz tarafının kaynak çekirdeğine yakın olan bölümlerde ITAB’da tane irileşmesi belirgin olarak görülürken ostenitik paslanmaz tarafında tane irileşmesinden daha ziyade yeniden kristalleşme ile tane incelmesi görülmektedir.
• Kaynak çekirdeği mikroyapı ve EDS analiz sonuçları ostenitik ve ferritik paslanmaz çelik birleştirmelerinin kaynak çekirdeğinde lokal bir ergimenin oluşması sebebiyle ferritik-ostenitik dubleks paslanmaz çelik kimyasal bileşimine yakın bir yapı meydana gelmiştir.
Bütün bu değerlendirmeler ışığında feritik ve ostenitik farklı paslanmaz çelikler endüstride belirli soğuk deformasyon işlemine tabi tutulduktan sonra direnç kaynaklı işlemlere maruz kalacaksa uygun ısı girdisi sağlayan kaynak çevrimi yada akım şiddetiyle birleştirilmesi önerilir. Kaynak çekirdeğinin dayanımı ile ilgili bir sorun olmasa da ferritik paslanmaz çelik tarafındaki bilhassa ITAB’da tane irileşmesi hususunun göz önünde bulundurulmalıdır.
5. TEŞEKKÜR
Çalışmada Zonguldak Karaelmas Üniversitesi Bilimsel Araştırma Geliştirme Projeleri kapsamındaki 2006-70-01-01 nolu proje imkanlarından yararlanılmıştır.
6. KAYNAKLAR
[1] K.G. Bricker, J.D. Defilippi, in: D. Peckner, I.M. Bernstein (Eds.), “Handbook of Stainless Steel”, Mc Graw-Hill Publishing, New York, 1977, pp. 25–31.
[2] R.A. Lula, J.G. Parr, A. Hanson, in: American Society for Metals, “Stainless Steel”, ASM, OH, Metals Park, 1986, pp. 60–69.
[3] A. Aran, M.A Temel, Paslanmaz çelik yassı mamuller, Sarıtaş Teknik Yayın, No:1, Ekim 2003, ISBN975-92326-0-X.
[4] W. S. Lee, C. F. Lin, C. Y. Liu, C. W. Chenga, “Effects of strain rate and welding current mode on microstructural properties of SUS 304L PAW welds”, Journal of Materials Processing Technology, 183 (2007) pp.183–193.
[5] W. S. Lee, J. I. Chenga, C. F. Lin, “Deformation and failure response of 304L stainless steel SMAW joint under dynamic shear loading” Materials Science and Engineering A 381, 2004, pp.206–215.
[6] S. Kou, “Welding Metallurgy”, Second edition, A Wiley-Interscience publication. ISBN 0-471-43491-4, 2003.
[7] H. Qiu, H. Mori, M. Enoki, T. Kishi, “Effect of welding thermal cycle and cold working on the ductility of SN490 steel under low and high-speed loading”, Materials Science and Engineering A316 2001, pp.217–223.
[8] T. S. Byun, N. Hashimoto, K. Farrell, “Temperature dependence of strain hardening and plastic instability behaviors in austenitic stainless steels”, Acta Materialia 52, 2004, pp. 3889–389.
[9] L. Jeffus, H. V. Johnson, “Welding Principles and Applications”, Delmar Publishers Inc, Second Edition, New York, 1988, pp.330-333.
[10] B. Bouyousfi, T.Sahraoui, S. Guessasma, K. T. Chaouch, “Effect of process parameters on the physical
characteristics of spot weld joints”, Materials & Design, Volume , Issue , 2005, in press.
[11] R. J. Madsen, “Welding Fundamentals”, American Technical Publishers Inc, USA, 1982, pp. 258-259.
[12] D. A. Althouse, C. H. Turnguist, W. A. Bowditch, K. E. Bowditch, “Modern Welding”, The Goodheart-Willcox Company Inc. 1988, pp. 439-455.
[13] H, W. Kearns, “Welding Processes”, AWS Welding Handbook, 7th edition. Vol.3, American Welding Society, Published by Macmillan Press Ltd, London, England,1982.
[14] H, W. Kearns, “Metals and Their Weldability”, AWS Welding Handbook, 7th edition. Vol.3, American Welding Society, Printed in the USA, 1982.
[15].R. Kacar, Hydrogen measurement in duplex stainless steel, PhD thesis, University of Leeds, UK. 1997.
7. ÖZGEÇMİŞ
Doç. Dr. Ramazan Kaçar 1969 yılında İznik–Bursa da doğmuştur. Yüksek öğrenimini Gazi Üniversitesi Teknik Eğitim Fakültesi Metal Eğitimi Bölümünde 1992 yılında tamamlamıştır. 1993 yılında YÖK bursu ile Lisans üstü eğitimini yapmak üzere İngiltere Leeds Üniversitesi Malzeme Okuluna gönderilmiştir.‘Dubleks paslanmaz çeliklerin kaynağında hidrojen’ konulu doktora çalışmasını tamamlayarak 1998 yılında Zonguldak Karaelmas Üniversitesi Karabük Teknik Eğitim Fakültesi Metal Eğitimi Bölümüne dönmüştür. Kaynak Eğitimi Anabilim dalında öğretim elemanı olarak hizmet veren Ramazan Kaçar, 2005 yılından itibaren Doc. Dr. olarak aynı anabilim dalında görev yapmaktadır. Uzmanlık alanı paslanmaz çelikler, kaynak metalürjisi, kaynaklı birleştirmelerdir
. . .
İçerik sadece atıfta bulunularak yayınlanabilir: Sivas İş Dünyası. Editöryal görüş, yazarın görüşüne aykırı olabilir.