Farklı Kireç Besleme Yöntemlerinin Elektrik Ark Ocağında Enerji ve Süreye Etkisinin İncelenmesi
Bu çalışmada farklı kireç besleme yöntemlerinin Elektrik Ark Ocağında enerji ve süreye etkisi araştırılmıştır.
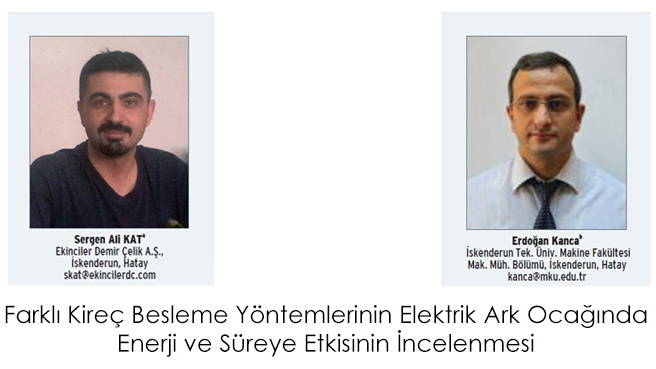
Bu çalışmada farklı kireç besleme yöntemlerinin Elektrik Ark Ocağında enerji ve süreye etkisi araştırılmıştır.
Bu çalışmada farklı kireç besleme yöntemlerinin Elektrik Ark Ocağı’nda enerji ve süreye etkisi araştırılmıştır. Bu amaçla 3 döküm hurda sepetiyle, 3 döküm de konveyör sistemle ocak kapağından beslenerek; üretim süreçleri tamamlanıp dökümler devrilmiştir. Aynı kalitede hurda, oksijen, doğalgaz, karbon ve kireç kullanılarak yapılan deneylerde; kireç farklı miktarlarda olmak üzere her iki yöntemle de ocağa beslenerek, izabe sürecinde alınan prova sonuçlarına göre gerektiğinde ilaveler yapılmış ve üretim süreçleri tamamlanmıştır. Üretim değerleri karşılaştırıldığında, kapaktan kireç besleme yönteminin enerjiyi ve enerjili süreyi düşürdüğü görülmüştür.
Anahtar kelimeler:
Elektrik Ark Ocağı, Kireç Besleme, Enerji, Enerjili Süre
Abstract
In this study, it is investigated that the effects of different lime feeding methods on energy and time in the electric arc furnace. For this purpose, the lime was feeded into the eletcric arc furnace three casting in a scrap basket and three casting with a conveyor system on the furnace roof. In experiments in which were used same quality of scrap, oxygen, natural gas, carbon and lime different quantity of lime was feeded in two methods and for taking of samples in smelting process lime was added to the eletric arc furnace and production processes were completed. Comparing of production datas, it was seen that the lime feeding method on the furnace roof was reduced; energy, and power on time.
Keywords:
Electric Arc Furnace, Lime Feed Methods, Energy, Power On Time
Hurdanın çeliğe geri dönüşümü için günümüzde kullanılan proses, Elektrik Ark Ocağı (EAO) prosesidir. Gelişen teknolojiler ile birlikte, ilk yatırım maliyetlerinin çok düşük ve daha basit bir isletme prosesine sahip olmalarından dolayı EAO’ları dünya çelik üretiminde %30’lara ulaşan bir pay elde etmiştir. Türkiye’ de ise bu oran %70’lerin üzerindedir. [1]
Kullanımından bu yana mini çelik tesislerinde izabe amacıyla çalıştırılan elektrik ark ocakları teknolojik prensibi değişmemesine rağmen gerek boyut gerek fırın dizaynı, gerekse çalışma sekli açısından zamanımıza kadar önemli değişikliklere uğramıştır. Son yıllarda bu değişikliklerden en önemlileri, alternatif akim (AC) yerine doğru akım (DC) kullanılması, oksitleyici gaz üflenmesi, kati sıvı veya gaz seklinde ilave yakıt enjeksiyonu, refrakterlerdeki iyileştirmeler ve izabenin otomasyona bağlanması ve cürufsuz döküm alma (EBT) teknikleridir. Bu yenilikler sayesinde 30 dakikaya varan sürelerde fosfor giderme de dahil döküm alınabilmektedir. [2]
Hurda ve demir cevherine kıyasla daha düşük miktarlarda da olsa, çelik üretim prosesinde başka metaller ve alaşım elementleri de kullanılmaktadır. Bu girdilerin kullanılmasındaki amaç, üretilen çeliğin kimyasal özelliklerinin güçlendirilmesi veya ürünler üzerindeki empüritelerin giderilmesidir. [3]
Empüritelerin giderilmesinde kullanılan malzemelere cüruf yapıcılar denilmektedir. Elektrik Ark Ocağı’nda kullanılan en önemli cüruf yapıcı kireçtir. Kireç, Elektrik Ark Ocağı’nda Fosforun(%P) giderilmesinde kullanılmaktadır. CaO, fırına yanmış kireç veya dolomit olarak hurda ile birlikte yada izabe esnasında direk beslenir. Birden çok hurda sepeti şarjının fırında erimesinden sonra dekarbürizasyon ve defosforizasyon gerçekleşir. [4]
Kullanılan kireç taşının saflık derecesi ve kireç fırınlarında optimal şartlarda kalsine edilmesi ark ocaklarındaki kullanım performansı yani çelikteki kükürt ve fosfor gibi safsızlıklarla en hızlı ve en etkili bir biçimde reaksiyona girme kabiliyeti açısından çok önemlidir. [5]
Kirecin normal kalsinasyon sıcaklığından daha yüksek sıcaklıklarda (Ör: 1200 oC ve üzeri) pişirilmesi durumunda kireç, sinterleşerek gözenekleri kapanır, reaksiyon yüzeyi azalır, küçülür ve ağırlaşır. Çekirdekteki kireçleşmemiş kısmın (CO2=kızdırma kaybı) çok azalmış, dolayısıyla serbest CaO miktarının çok yüksek bulunmasına rağmen kirecin ark ocağında cürufla reaksiyona girebilme (reaktivite) kabiliyeti düşer, kireç sarfiyatı ve tüketilen elektrik enerjisi miktarı artar. Aşırı pişmiş bu kirece sert kireç denir. Kirecin normal kalsinasyon sıcaklığından daha düşük sıcaklıklarda (Ör: 900 oC’ den düşük) pişirilmesinde ise, kireç taşı kirece tam dönüşemediğinden çekirdek kısmında %10’dan daha büyük oranlarda CaCO3 kalır(yüksek kızdırma kaybı). Böyle iyi pişmemiş bir kirecin çelik üretiminde kullanılması sırasında ark ocağında öncelikle çekirdeğin kireçleşme prosesi yaşanacağından elektrik sarfiyatı artar ve cüruf-eriyik reaksiyonları gecikir veya daha fazla kireç tüketilir. [5]
Hurdayla birlikte ocağa şarj edilen kireç (1 ton çelik için 30-60 kg kireç) reaksiyon kabiliyeti yüksek bazik bir cüruf oluşumunu sağlar. Cürufta çözünen kireç, eriyikteki safsızlıklarla reaksiyona girerek seri bir defosforizasyon prosesi gerçekleştirir. [5]
Defosforizasyon prosesi, eriyikte demir oksitle birleşik halde bulunan fosforun sönmemiş kireçle reaksiyonu sonucunda gerçekleşir:
2[P] + 5(FeO) + n(CaO) n(CaO.P2O5) + 5[Fe] (1.1) (Eriyik) (Cüruf) (Çözünmüş halde cürufta) (Cüruf) (Eriyki) Bu reaksiyonun kısa zamanda gerçekleşmesi için reaksiyon denge sabitini arttıran CaO ’ın aktivitesinin mümkün olduğu kadar yüksek olması gerekir. Başka bir deyişle kireç, eriyik içinde mümkün olduğu kadar kısa sürede çözünmeli yani reaktivitesi yüksek olmalıdır. Aksi takdirde düşük kaliteli bir kireç, cüruf kalınlığını arttırdığı gibi ısı transferini de olumsuz yönde etki eder ve cüruf-eriyik reaksiyonunu frenler. Yani kirecin çözünme hızı defosforizasyon hızını belirler. [5] Yani, fosforun metalden cürufa geçmesi EAO prosesini çelik üretimi konusunda önemli bir fonksiyon haline getirmektedir. [6]
Fosfor, çeliğin mekanik özelliklerini olumsuz yönde etkileyen (uzama ve darbe mukavemeti, soğuk çekilebilirlik vs.) bir elementtir. Çelik içinde %0,015-0,050 değerleri arasında bulunması kabul edilebilinir. [7]
EAO’ nın şarjı hareketli kapak sistemi sayesinde üstten yapılabilmektedir. Büyük miktarda şarj malzemesi vinçler yardımıyla fırın kapağının yan tarafa alınmasıyla üstten fırına şarj edilir. [8] Fırına hurda şarjı yapılırken fırın refrakterlerine ve elektrodlara zarar gelmemesi için dikkatli çalışılmalıdır. Bunun için şarj yapılacak sepet altına hafif hurda yerleştirilmelidir ve yukarıya doğru hafiften ağıra yer almalıdır. Hurda şarjı ile birlikte fırına cüruf yapıcılarda şarj edilir. Flakslardan kireç taşının; ark bölgesine gelmeyecek şekilde şarjı yapılmalıdır, aksi takdirde elektrodların kırılmasına neden olabilmektedirler. [9]
Şarj işlemi tamamlandıktan sonra transformatör bir volt değerine ayarlanıp, yükleme esnasında açık olan akım anahtarı kapatılır. Böylece transformatörden ve elektrodların bağlı olduğu sekonder devreden akım geçer. Elektrodlar şarj seviyesine kadar indirilir. Ark oluşması ile birlikte ana kontrol düğmesi otomatik duruma getirilir. [7]
Yapılan literatür araştırmasında Erensoy K. tarafından, Elektrik Ark Ocaklarında Enerji Maliyetlerinin Araştırılması [1]. Lokman L, Sönmemiş Kirecin Ark Ocağı Çeliğinde Safsızlık Arıtma Kimyasalı Olarak Kullanılması [4].
Çalışmaları incelenmiş; Farklı Kireç Besleme Yöntemlerinin Elektrik Ark Ocağında Enerji ve Süreye Etkisi ile ilgili çalışmaya rastlanmamıştır. Dolayısıyla çalışmada; bu amaçla 3 döküm hurda sepetiyle, 3 döküm de konveyör sistemle ocak kapağından beslenerek; üretim süreçleri tamamlanıp dökümler devrilmiştir. Aynı kalitede hurda, oksijen, doğalgaz, karbon ve kireç kullanılarak yapılan deneylerde; kireç farklı miktarlarda olmak üzere her iki yöntemle de ocağa beslenerek, izabe sürecinde alınan prova sonuçlarına göre gerektiğinde ilaveler yapılmış ve üretim süreçleri tamamlanmıştır.
2.1 Çalışmada kullanılan hurdalar
Çalışmada kullanılan tüm hurdalar İngiliz menşeilidir. Hurda sahasından Bonus (Kirlilik oranı %0,5) ve HSM1 (Kirlilik oranı %2) (Ortalama Kirlilik Oranı: %1,57) özelliklerine sahip hurdalar polip vinçler yardımı ile hurda sepetlerine boşaltılmıştır.
A3 Hurdası: Demir dışı metallerin mevcudiyeti istenmez. Alaşımlı hurda ve Karbonlu hurdanın karışmaması gibi tek kalite ve tek gruptan oluşmalıdır. Bu tür bir karışım olursa %5’i geçmemelidir. Yanıcı, asit v.b. korozifler içermemelidir. [10]
HMS 1’i daha ziyade otomotiv şase ve jantları, kalın boru ve profiller, iş makinesi parçaları, silindirler ve miller, kazan bozmaları, inşaat demiri parçaları v.b. oluşturmaktadır. Bu parçaların et kalınlığı 4 mm’ den büyüktür. [10]
Deneysel çalışmalarda, kireç beslenecek birinci yöntem hurda sepeti olarak belirlenmiştir. İkinci yöntem olarak konveyör ile kapaktaki hollerden (kapak açılmadan) besleme yöntemi kullanılmıştır.
Sepet ile kireç besleme yönteminde EAO’ na yapılacak ilk şarj ön ısıtmaya girdiğinden dolayı kireç besleme ocağa ikinci şarj ile birlikte yapılmıştır. Kirecin üstte kalması durumunda elektrodların ark oluşturmama riski bulunmaktadır.
Kireç; bir kasa yardımı ile (Resim 1) tartıldıktan sonra, hurda sepetinin ortasına boşaltılarak, üstüne tekrar hurda konulmuştur. (Resim 2)
Çalışmada ortalama 41000 Kg Bonus, ortalama 61000 Kg HSM1 olmak üzere Ortalama döküm başına 102066,7 Kg. hurda kullanılmıştır.
2.2 Çalışmada kullanılan kireç
Çalışmada kullanılan kireç Nur Kireç firmasına ait olup, yapılan analiz sonucu Tablo 1’de verilmiştir.
Tablo 1: Kireç Analizi
Kriter %
Aktif CaO 91,32
PasifCaO + %MgO + %SiO2 + %Al2O3 8,68
Kızdırma Kaybı 1,45 Reaktivite 36,30
Deneysel çalışmalarda kullanılan kireç Resim 3’ te görülmektedir.
2.3 Çalışmada kullanılan test ve ölçü cihazları
Kasaya konulan kireç ve hurda sepetlerinin tartımları için yer ve araba kantarları kullanılmıştır. Kireç analizleri için;
Öğütme cihazı, Analitik hassas terazi, nem ve sıcaklık ölçer kullanılmıştır. Kimyasal analizler için; Bant zımpara makinesi, Numune parlatma cihazı, Spektral analiz cihazı(Marka: ARL) kullanılmıştır. Cüruf analizleri için; Öğütme Cihazı, Hammadde presleme cihazı, XRF cihazı Mekanik testler için; Mekanik ve dijital kumpas, Master blok set, Mekanik Test Cihazı ve Nervürlü çubuklar için ekstensometre kullanılmıştır.
2.4 Deneylerin yapılışı
Sepetten kireç besleme yöntemi ile 3, konveyör yardımıyla kapak hollerinden kireç besleme yöntemi ile de 3 olmak üzere toplamda 6 döküm için deneme yapılmıştır.
Üretimin başlamasına müteakip alınan ikinci döküm çalışmamızın ilk deneyi olmuştur. 501879 (1A) numaralı döküm için; 1. Hurda Şarjı: 52500kg, 2. Hurda Şarjı: 49600 kg (40500 kg Bonus, 60900 kg HMS1) olmak üzere toplamda: 101650 kg hurda şarj olmuştur. 2. Şarj ile birlikte sepetten kireç besleme yöntemi ile 3500 kg kireç hurda şarjı ile birlikte ocağa verilmiştir. Sonrasında çalışmaya başlandığı anda 3 numaralı faz kirece denk geldiğinden limit görmeyip, elektrotun kırılmasına sebep olmuştur (Resim 4-5). Kırılan elektrotun değiştirilmesi ve tekrar çalışmaya başlanması 25 dakikalık duruş olarak ölçülmüştür. (Duruş anında EAO’ nda harcanan enerji: 10790,8 kWh okunmuştur. Enerjili süre: 10,7 dakika) Duruş süresince ocak kapağı kapalı olacak şekilde lans ve brülörler çalıştırılarak enerji kaybı minimize edilmiştir.
İzabe süreci başlaması itibari ile kimyasal analiz için prova (Resim 6) ve cüruf numunesi alınıp, uygunluğu kontrol edilmiştir. %P değerinin uygunluğunun kontrol altına alınmasının ardından dökümün devrilmiştir. Döküm devirme sıcaklığı 1605 ºC. EAO’ nda harcanan enerji: 29890 kWh, enerjili süre: 29,5 dakika, döküm süresi(TTT) 62 dakika olarak kayıt edilmiştir.
Döküm devrildikten sonra Pota Ocağı’na(PO) geldiği anda prova alınıp; prova sonucuna göre gerekli alyaj ilaveleri yapılmış ve istenen kalite değerleri göz önünde bulundurularak sürekli döküm platformuna gönderilmiştir. 150x150 kare kütük olarak dökülen çelik, Ekinciler Demir ve Çelik A.Ş.’ ne ait haddehanede Ø12 mm nervürlü inşaat çeliği olarak mamul haline gelmiştir. Ürünlere yapılan mekanik testlerin de standart gereklerini yerine getirdiği görülmüştür.
501880 (2A) numaralı döküm için; 1. Hurda Şarjı: 52750 kg, 2. Hurda Şarjı: 48900 kg (41150 kg Bonus, 60200 kg HMS1) olmak üzere toplamda: 101650 kg hurda şarj olmuştur. Şarj ile birlikte sepetten kireç besleme yöntemi ile 2750 kg kireç 2. hurda şarjı ile birlikte ocağa verilmiştir. İzabe sürecinde cüruf numunesi alınmıştır, alınan ilk provada %P değeri yüksek olduğundan, ocak kapağı kaldırılarak 400 kg kireç vinç yardımı ile şarj edilmiştir. (Duruş süresi: 1,20 dakika olarak ölçülmüştür. Duruşa kadar EAO’ nda harcanan enerji: 25480,1 kWh okunmuştur. Enerjili süre: 23,6 dakika) (Toplam beslenen kireç: 3150 kg) ilave sonrasında tekrar çalışılarak ikinci prova alınmıştır, %P değerinin düşmesinin ardından döküm devrilmiştir. (EAO’ nda harcanan enerji: 29960,1 kWh okunmuştur. Enerjili süre: 27,8 dakika, Döküm Süresi(TTT): 35 dakika) Döküm devirme sıcaklığı 1611 ºC. Pota Ocağı ve Haddehane süreçleri 501879 numaralı döküm ile aynı şekilde işlemiştir. 501881 (3A) numaralı döküm için; 1. Hurda Şarjı: 51050 kg, 2. Hurda Şarjı: 49550 kg (39200 kg Bonus, 61150 kg HMS1) olmak üzere toplamda: 100600 kg hurda şarj olmuştur. 2. Şarj ile birlikte sepetten kireç besleme yöntemi ile 2750 kg kireç 2. hurda şarjı ile birlikte ocağa verilmiştir. İzabe sürecinde cüruf numunesi alınmıştır, alınan ilk provada %P değerini iyileştirilmek amacıyla, ocak kapağı kaldırılarak 600 kg kireç vinç yardımı ile şarj edilmiştir. (Toplam 3350 kg kireç) Duruş süresi: 1,30 dakika olarak ölçülmüştür. Duruş anında EAO’ nda harcanan enerji: 24700,9 kWh, Enerjili süre: 23,9 dakika okunmuştur. İlave sonrasında tekrar çalışılarak ikinci prova alınmış ve %P değerinin düşmesinin ardından döküm devrilmiştir. Döküm devirme sıcaklığı 1598 ºC. (EAO’ nda harcanan enerji: 30560 kWh okunmuştur. Enerjili süre: 29,6 dakika, Döküm Süresi(TTT): 37 dakika) Pota Ocağı ve Haddehane süreçleri 501879 numaralı döküm ile aynı şekilde işlemiştir.
501884 (1B) numaralı döküm için; 1. Hurda Şarjı: 50500kg, 2. Hurda Şarjı: 52200 kg (40850 kg Bonus, 61550 kg HMS1) olmak üzere toplamda: 102700 kg hurda şarj olmuştur. Bu dökümde de kireç ocağa konveyör yardımı ile kapakta bulunan iki adet holden verilmiştir. Ocağın kapağı açılmadan yapılan beslemede; 1. Hurda şarjından sonra çalışılmaya başlanmış ve 5-10 dakika sonra ocağa ilk kireç şarjı 1765 kg olarak yapılmıştır.
2. Hurda şarjı yapıldıktan 5 dakika sonra 2. Kireç şarjı 1735 kg olarak yapılmıştır. (Toplam 3500 kg kireç) İzabe sürecinde cüruf numunesi alınmıştır, iki adet prova alınmıştır. İlk provada %P değeri yeterli seviyelere düştüğü görülmüştür. Döküm devirme sıcaklığı 1604 ºC. (EAO’ nda harcanan enerji: 26770 kWh okunmuştur. Enerjili süre: 27,6 dakika, döküm Süresi (TTT): 41 dakika) Pota Ocağı ve haddehane süreçleri 501879 numaralı döküm ile aynı şekilde işlemiştir.
501883 (2B) numaralı döküm için; 1. Hurda Şarjı: 51050kg, 2. Hurda Şarjı: 52550 kg (42250 kg Bonus, 61100 kg HMS1) olmak üzere toplamda: 103600 kg hurda şarj olmuştur. Bu dökümde kireç ocağa konveyör yardımı ile holden verilmiştir. Böylece daha homojen bir besleme yapılmıştır. Ocağın kapağı açılmadan yapılan bu beslemede; 1. Hurda şarjından sonra çalışılmaya başlanmış ve 5-10 dakika sonra ocağa ilk kireç şarjı 1750 kg olarak yapılmıştır. 2. Hurda şarjı yapıldıktan 5 dakika sonra 2. Kireç şarjı 1400 kg olarak yapılmıştır. (Toplam 3150 kg kireç) İzabe sürecinde cüruf numunesi alınmıştır, iki adet prova alınmıştır. İlk provada %P değeri yeterli seviyelere düştüğü görülmüştür. Döküm devirmeden önce alınan ikinci provada bu değerin daha da iyileştiği gözlenmiştir. Döküm devirme sıcaklığı 1606 ºC. (EAO’ nda harcanan enerji: 28929,9 kWh okunmuştur. Enerjili süre: 27,7 dakika, Döküm Süresi(TTT): 35 dakika) Pota Ocağı ve haddehane süreçleri 501879 numaralı döküm ile aynı şekilde işlemiştir.
501882 (3B) numaralı döküm için; 1. Hurda Şarjı: 50100kg, 2. Hurda Şarjı: 52100 kg (41800 kg Bonus, 60100 kg HMS1) olmak üzere toplamda: 102200 kg hurda şarj olmuştur. Bu dökümde kireç ocağa konveyör yardımı ile kapakta bulunan iki adet holden verilmiştir. Kireç besleme yönteminin değişmesi ile birlikte ocağa yapılacak her iki hurda şarjı için ayrı ayrı kireç besleyebilme imkânı doğmuştur. Böylece daha homojen bir besleme yapılmıştır.
Ocağın kapağı açılmadan yapılan beslemede; 1. Hurda şarjından sonra çalışılmaya başlanmış ve 5-10 dakika sonra ocağa ilk kireç şarjı 1745 kg olarak yapılmıştır. 2. Hurda şarjı yapıldıktan 5 dakika sonra 2. Kireç şarjı 1025 kg olarak yapılmıştır. İzabe sürecinde cüruf numunesi alınmıştır, alınan ilk prova sonucu da göz önünde bulundurularak %P değerini iyileştirilmek amacıyla, yaklaşık olarak 24. Enerjili süre zamanında ocağa 580 kg daha kireç beslenmiştir. (Toplam 3350 kg kireç) %P değerinin düşmesinin ardından döküm devrilmiştir. Döküm devirme sıcaklığı 1602 ºC. (EAO’ nda harcanan enerji: 29050 kWh okunmuştur. Enerjili süre: 29,4 dakika, Döküm Süresi (TTT): 38 dakika) Pota Ocağı ve Haddehane süreçleri 501879 numaralı döküm ile aynı şekilde işlemiştir. Yapılan deneyler toplamda altı adet (3 döküm hurda sepetiyle, 3 döküm de konveyör sistemle ocak kapağından beslenerek) olmaktadır. Sadece kireç besleme yönteminin ve miktarının değiştiği diğer etkenlerin sabit tutulduğu bir çalışma yapılmıştır.
2.5 Deney verilerinin karşılaştırılması
Değerlendirme yapılırken farklı yöntemler ile aynı miktarda kireç beslenen dökümlere ait enerji ve enerjili süre verilerinden yararlanılmıştır.
1) 501879 (1A) numaralı döküme sepet ile 3500 kg kireç beslenmiştir. 501884 (1B) numaralı döküme konveyör yardımı ile ocak kapağındaki hollerden 3500 kg kireç beslenmiştir.
2) 501880(2A) numaralı döküme sepet ile 3150 Kg kireç beslenmiştir. 501883 (2B) numaralı döküme konveyör yardımı ile ocak kapağındaki hollerden 3150 Kg kireç beslenmiştir.
3) 501881(3A) numaralı döküme sepet ile 3350 Kg kireç beslenmiştir. 501882 (3B) numaralı döküme konveyör yardımı ile ocak kapağındaki hollerden 3350 Kg kireç beslenmiştir.
Yapılan karşılaştırmalar sonrasında oluşan grafikler aşağıdaki gibidir. Grafik 1‘de görüldüğü üzere 10.7’nci enerjili süre(dk) sonrasında elektrod kırılması ile başlayan enerji sarfiyatı döküm sonunda dakikada 501779 (1A) için: 1013,22 kwh, 501884 (1B) için: 969,93 kWh olarak görülmektedir.
Grafik 2’de görüldüğü üzere 23,6’ncı enerjili süre(dk) sonrasında; kireç ilavesi sırasında kaybedilen enerji, enerjili sürenin uzamasına ve daha yüksek enerji çekilmesine sebep olmuştur. Enerji sarfiyatı döküm sonunda dakikada 501880 (2A) için: 1077,7 kWh, 501883(2B) için: 1044,4 kWh olarak görülmektedir.
Grafik 3’de görüldüğü üzere 23,9’ncu enerjili süre(dk) sonrasında; kireç ilavesi sırasında kaybedilen enerji, enerjili sürenin uzamasına ve daha yüksek enerji çekilmesine sebep olmuştur. Enerji sarfiyatı döküm sonunda dakikada 501881(3A) için: 1032,4 kWh, 501882(3B) için: 988,1 kWh olarak görülmektedir.
Her iki yöntem ile yapılan üretimlerin ortalama enerjili süre karşılaştırma grafikleri sırasıyla aşağıda verilmiştir.
Grafik 4’de görüldüğü üzere kapaktan kireç beslenerek yapılan üretimlerde enerjili süre; 501282(3B), 501283(2B), 501284(1B) nolu dökümler için ortalama olarak 28,23 dakika olarak hesaplanmıştır. Aynı şekilde hurda sepetinden kireç beslenerek yapılan üretimlerde enerjili süre; 501279(1A), 501280(2A), 501281(3A) nolu dökümler için ortalama olarak 28,97 dakika olarak hesaplanmıştır. Kapaktan kireç besleme yöntemi ile yapılan üretimlerin, hurda sepetinden kireç besleme yöntemi ile yapılan üretimlere göre enerjili süre bakımından 0,64 dakika daha az olduğu görülmektedir.
Grafik 5’e göre; kapaktan kireç beslenerek yapılan üretimlerde (501282(3B), 501283(2B), 501284(1B)) ortalama sarf edilen enerji: 28249,98 kWh, hurda sepetinden kireç beslenerek yapılan üretimlerde ortalama (501279(1A), 501280(2A), 501281(3A) nolu dökümler için) olarak sarf edilen enerji: 30136,68 kWh olduğu görülmektedir. Kapaktan kireç besleme yöntemi ile yapılan üretimlerin, hurda sepetinden kireç besleme yöntemi ile yapılan üretimlere göre EAO’nda sarf edilen enerji bakımından 1886,7 kWh daha az olduğu görülmektedir.
Kapaktan kireç beslenerek yapılan üretimlerde ortalama (501282(3B), 501283(2B), 501284(1B) nolu dökümler için) olarak ton başına sarf edilen enerji 297,83 kWh/t, hurda sepetinden kireç beslenerek yapılan üretimlerde ise ortalama (501279(1A), 501280(2A), 501281(3A) nolu dökümler için) olarak ton başına sarf edilen enerji: 328,93 kWh/t olduğu görülmektedir (Grafik 6). Kapaktan kireç besleme yöntemi ile yapılan üretimlerin, hurda sepetinden kireç besleme yöntemi ile yapılan üretimlere göre ton başına sarf edilen enerji bakımından 31,1 kWh/t daha az olduğu görülmektedir.
Yapılan deneylerden elde edilen sonuçlar ve yapılan karşılaştırmalara göre; hurda sepetinden kireç belseme yöntemi ile yapılan üretimlerin, ocak kapağından kireç besleme yöntemi ile yapılan üretimlere göre enerjili süre ve EAO enerji tüketimi bakımından daha yüksek değerlere sahip olduğu görülmüştür. Hurda sepetinden kireç besleme yönteminde; beslenen kirecin, hurda ocak içerisine şarj olunurken kontrollü olarak konumlandırılamıyor olması sebebiyle elektrod kırılması gibi problemlere yol açabildiği; dolayısıyla bu durumun hem enerji, hem döküm süresi, hem de elektrod kayıplarına neden olabileceği görülmektedir.
Ocak kapağından kireç besleme yönteminde; besleme hollerinin açıları, elektrod-hurda temas bölgesine denk gelmeyecek şekilde konumlandırılabiliyor olması sebebiyle elektrodların kirece denk gelme olasılığının azaldığı, kırılma riskinin ve dolayısıyla; enerji, döküm süresi ve elektrod kayıplarının minimize edildiği görülmüştür.
[1] Erensoy, K., Elektrik Ark Ocaklarında Enerji Maliyetlerinin Araştırılması, Antakya, 2007
[2] Ozaksoy, M.G., İkincil Çelik Üretiminde Kükürt Giderimi ve Çelik Kalitesi, İstanbul, 2004
[3] T.C. Kalkınma Bakanlığı, Onuncu Kalkınma Planı, Demir Çelik Çalışma Grubu Raporu, S.19, Aralık, 2014
[4] Yildirim, İ.Z., Prezzi, M., Chemical, Mineralogical and Morphological Properties Of Steel Slag, USA, July, 2011
[5] Lokman L., Sönmemiş Kirecin Ark Ocağı Çeliğinde Safsızlık Arıtma Kimyasalı Olarak Kullanılması, Anonim
[6] Pretorius E., Oltmann, H. LWB Refractories, Process & Technology Group, EAF Fundamentals, P. 39-40
[7] Kat, S.A., Geçmişten Günümüze Demir-Çelik Üretim Yöntemleri ve Teknolojik Gelişmeler, Haziran, 2010
[8] The University of Liverpool, Electric Ark Furnace Simulation User Guide Version 1, P. 5 - 9, 2006
[9] Jones J.A.T, Bowman B., Lefrank P.A., Electric Furnace Steelmaking, Steelmaking and Refining Volume, P.623, 1998
[10] Ezer, İ. Hurda El Kitabı, Ekinciler Demir ve Çelik A.Ş., 2010
. . .
İçerik sadece atıfta bulunularak yayınlanabilir: Sivas İş Dünyası. Editöryal görüş, yazarın görüşüne aykırı olabilir.