Kusursuz Pedallar
Bisiklet meraklılarının ve endüstriye yakın olanların bileceği üzere, İsviçre’nin en ünlü bisiklet üreticisi BMC için geçtiğimiz on yıl heyecanlı olduğu kadar zaman zaman zorlu da geçti.
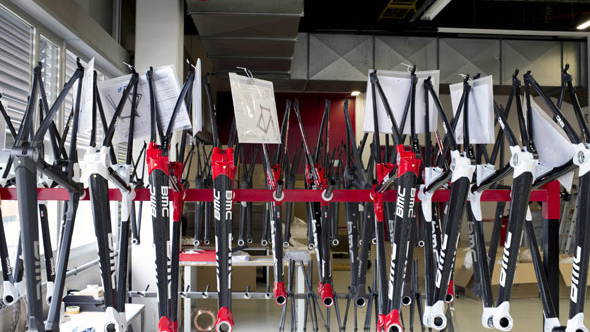
Bisiklet meraklılarının ve endüstriye yakın olanların bileceği üzere, İsviçre’nin en ünlü bisiklet üreticisi BMC için geçtiğimiz on yıl heyecanlı olduğu kadar zaman zaman zorlu da geçti.
İlk olarak Raleigh adı altında bisiklet yapan göçmen bir İngiliz tarafından kurulan şirket, 2001 yılında İsviçreli iş adamı Andy Rihs tarafından satın alındı. Bern yakınlarındaki Grenchen’de etkileyici yeni bir fabrika inşa eden Rihs’in basit ve net bir hedefi vardı: Tour de France’ı kazanacak kapasitede bir bisiklet ve takım yaratmak.
Beklenen zafer nihayet 2011’de Avustralyalı bisikletçi Cadel Evans’la geldi ve o zamandan bu yana, en çok talep gören, teknolojik olarak gelişmiş bisiklet üreticisi olarak BMC’nin adı daha da duyuldu. Fabrika artık takıma yaptığı üretimin yanı sıra profesyonel ve amatör yarışçılar ve zengin meraklılar için özel tasarım, el yapımı, karbon iskeletli bisikletler üretiyor.
Fiyat spektrumunun diğer ucunda BMC’nin popüler imalat iskeletleri Çin ve Tayvan’da yapılıyor. Burada üretilen bisikletler Avrupa’ya geri gönderilmeden önce bu ülkelerde temelli olarak yaşayan ve şirket onayından geçmiş mühendislerin titiz denetiminden geçiyor.
Grenchen fabrikasında görev yapan BMC Operasyon Direktörü Martin Känzig şöyle diyor “Bisikletler buraya geldiğinde %80 sürülmeye hazır halde oluyorlar. Tek yaptığımız tekerlekleri ve çatalları eklemek. Başından sonuna kadar bu impec fabrikasında yaptığımız opsiyonlu bisikletler yalnızca gerçekten en üst kalitede olan bisikletler.”
Özel yapım bisikletler sizi etkilemeye yetmediyse Grenchen’deki impec fabrikasına hakim olan ve Bay Känzig’in söylediğine göre dünyada bir eşi daha bulunmayan, multi milyon avroluk, üç aşamalı, karbon tüp tipi imalat süreci aklınızı başınızdan alacaktır. Şu anda bir BMC impec iskeletinin yapımına yaklaşık 4 km.lik karbon harcanıyor.
“BMC impec bisikletini diğerlerinden ayıran ve kritik öneme sahip bileşenler, kaynaksız karbon borulardır. İmalat süreci örgü işlemiyle başlar. Bu aşamada boruların her biri robota yüklenir ve silikon gövde üzerine merkezkaç gücüyle dört kat karbon fiber döküm yapılır.”
Robot borunun tipini algılar, ilgili programı yükler ve karbon fiber uygulama işlemine başlar; borunun uzunluğuna ve karmaşıklığına göre değişmekle birlikte operasyon yaklaşık 7 dakika sürer. İkinci işlem reçine enjeksiyonudur. Bu aşamada boruya şekil verilir ve işlemin adından da anlaşılacağı gibi reçine enjekte edilir ve sertleşmeye bırakılır. Son olarak borular altı eksenli bir robot ve elmaslı testereyle gereken boyuta getirilir. “Bu düzeni kullanarak şu anda yılda yaklaşık 1300 bisiklet yapıyoruz; ama aslında kapasitemiz 2500’ün üzerinde.”
Boru yapma makinelerinden daha küçük ve daha az göze batan, ancak imalat sürecinde en az bir o kadar öneme sahip, şirketin tek Haas VF4-SS Super Speed CNC işleme merkezi fabrikadaki yerini 2010'da almış.
“Haas tezgahını bağlama düzenekleri ve fikstürler yapmak ve ayrıca yeni bisikletler için ARGE ya da prototip parçalar üretmek için kullanıyoruz. İkinci amaç bağlamında bileşenleri 3D CAD kullanarak tasarlıyoruz ve sonra Haas’ta işliyoruz; bu yöntem bize 3D yazdırma gibi diğer teknolojilerden daha hızlı ve kolay geliyor. Ayrıca gerçek hayat koşullarında test edilmeye uygun, gerçek mekanik niteliklere sahip bir parça elde etmiş oluyorsunuz.”
BMC’de kullanılan Haas tezgahın gelecekteki imalat işleri için de tahsis edildiğini ekliyor Bay Känzig. “Yeni nesil ürünlerde, VF4-SS’i iskelet borularını frezelemek için kullanmayı düşünüyoruz. Böylece birbirlerine daha yakın konumda olabilecekler. Bu stratejiyi en etkin şekilde uygulayabilmemiz için bir tane daha VF4-SS almamız gerekeceğini düşünüyoruz. Hedefimiz şu anki bisikletlerden daha az parça kullanarak tamamıyla yeni bir bisiklet yapmak.”
BMC boru üretiminde geleneksel yuvarlak kesit yöntemini nadiren kullanıyor. Bay Känzig durumu şöyle açıklıyor “Bunu teknik avantajlar sağladığı için yapmıyoruz; bu daha çok markamızı yansıtan bir tasarım özelliği. Ama bu yolu seçtiğimizde gereken takımları yapmak zorlaştı." Şirketin Haas tezgahı satın almasının nedeni de buydu.
Şu an kullanılan üretim modeli 2010’da geliştirilme aşamasındayken BMC mühendisleri, prototipleme ve test süreçlerini bitirip imalata geçmek için baskı altındaydılar.
Bay Känzig anlatıyor “Hep zorlukla karşılaştığımız konulardan biri de bağlama düzeneği ve takım parçalarının dış tedarikçilerden zamanında ve bütçe dahilinde temin edilmesiydi. Sistemin çok pahalı ve çok zaman alıcı olduğuna karar verdik. Mühendislerimizden biri daha önce mekanik parçalar üreten bir firmada çalışmıştı. Kendisi Haas tezgahlarıyla ilgili deneyime sahipti ve bu tezgahlara çok hayranlık duyuyordu; yani VF4-SS’e yatırım yapma kararını almamız zor olmadı. Bu tezgahı, fikstürler ve bağlama düzeneklerinin yanı sıra bazı modellerde bulunan bazı küçük parçaların imalatı için de kullanıyoruz. Plastik parçaları da frezelemeye başladık; mesela boru mafsalları. Teknik tasarımda bazı geliştirmeler yapıldıktan sonra şekillerde biraz değişiklik oldu. Enjeksiyon kalıplarımızı çöpe atıp baştan yenilerini yapmak yerine –ki bu çok pahalıya gelirdi– parçaları Haas frezeyi kullanarak işlemenin daha iyi olacağına karar verdik.”
Şirketin Tour de France’da ve diğer büyük etkinliklerde kullanılan, üst düzey teknik özelliklere sahip yarış makineleri de Grenchen fabrikasında özel imal ediliyor. Örneğin iskeletin rengi bisikletçinin pozisyonunu yansıtacak şekilde değişiyor; puan lideri için yeşil (en tutarlı şekilde finiş gören bisikletçi), “Dağların Kralı” için kırmızı benekli beyaz ve genel yarış lideri için sarı. Bisikletçilere ve farklı yarışlara özel olarak yapılan bisikletlere değer biçmek neredeyse imkansız.
Bay Känzig şöyle diyor “En üst kalitedeki bisikletleri satın alan müşteriler çok özel bir şey istiyorlar. İmalat bisikletleri açısından en büyük pazarımız İsviçre. Diğer taraftan Almanya ve Fransa’da son zamanlarda güzel kazanç elde ettik ve İtalya’da da satışlar artıyor. ABD de Birleşik Krallık gibi büyüdüğümüz pazarlardan biri. Toplam olarak yılda 45.000 civarında imalat bisikleti yapıyoruz. BMC'yi örneğin Giant gibi yılda birkaç milyon bisiklet yapan üreticilerle karşılaştırmak mümkün değil. Ama onların bisiklet fiyatlarının ortalamasına baktığınızda, başka bir pazara hitap ettiklerini görürsünüz. İmpec bisikletler için müşterilerimiz yarışa özel veya performansa özel üretim (daha yüksek, daha güvenli ve daha güzel görünür) isteyebilirler. Tüm ürünlerimizde Shimano Di2 elektronik vites değiştiricileri kullandığımızı da belirtmek isterim. Tüm yol bisikletleri hesaba katıldığında şu anda dünyada en çok Di2 grup seti satın alan müşterilerden biriyiz.”
BMC için büyüyen küresel bisiklet talebi önemli, ancak bir zamanların küçük çaplı ve nispeten bilinmeyen markasını dünyanın en arzu edilen bisiklet markalarından biri haline getiren şüphesiz yüksek kaliteli, özel yapım modeller. Sahip olduğu esnek takımlar ve imalat süreçleri şirketin yeni ürün tasarımları denemesinin yanı sıra, en az bir o kadar önemli olarak, yeni iskeletler ve bileşenler için gereken bağlama düzeneklerini ve fikstürleri yapmasına olanak sağlıyor.
Martin Känzig sözlerini şöyle bitiriyor “Haas VF-4SS operasyonlarımızın çok önemli bir parçası olduğunu çoktan kanıtladı. Bu tezgahı şu anda %70-80 oranında kullanıyoruz ve her gün onunla yapacak yeni şeyler keşfediyoruz. Programlanması ve kullanılması çok kolay; ayrıca çok güvenilir.”
Yarış kazanan takımlar ve bisikletler yapabilmek için sorunları daha ortaya çıkmadan gidermek gerekir. Kusursuz fabrikasını kurarken Andy Rihs’in bunu düşündüğüne şüphe yok. Fabrikasındaki tek CNC Tezgahı olarak Haas’ı tercih etmiş olması tesadüf değil.
. . .
İçerik sadece atıfta bulunularak yayınlanabilir: Sivas İş Dünyası. Editöryal görüş, yazarın görüşüne aykırı olabilir.