LSH-Laser Surface Hardening Kalıp ve Makine Parçalarının Sertleştirilmesinde Yüksek-Güçlü Diyot Lazer
Yüzeyin mekanik özelliklerini değiştirmek için en etkin lazer ışın kaynağıdır.
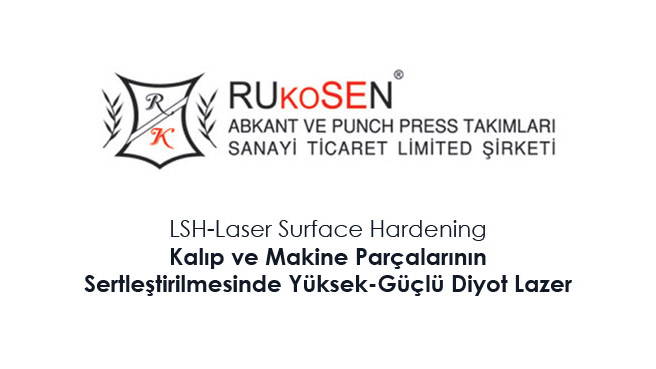
Yüzeyin mekanik özelliklerini değiştirmek için en etkin lazer ışın kaynağıdır.
Yüzeyin mekanik özelliklerini değiştirmek için en etkin lazer ışın kaynağıdır.
Malzemelerin yüzeyinin mekanik özelliklerini değiştirmek için sertleştirme sektöründe en yaygın kullanılan yöntemdir. Yüzey sertleştirme ısıl işlemi ile sürtünmeler sonucu oluşan veya yüksek basınç altında çalışmayla ortaya çıkan aşınmalara karşı korunmak için aşınma direncinde artış, sürtünme katsayısında düşüş sağlanmaktadır. Geleneksel yüzey sertleştirme prosesleri alevle sertleştirme ve indüksiyonla sertleştirmedir. Yüksek Güçlü Diyot lazer ile sertleştirme farklı bir proses olmasıyla birlikte geleneksel yöntemlere kıyasla çeşitli avantajlar sağlayan bir lazer teknolojisidir.
Bununla birlikte, tanımlanmış bir sıcaklık aşınmaya dayanıklı bir yüzey için zaman profili, gerçekleştirilmek istenen sertleştirme sonucuna uygun seçilmelidir. Bahsedilen sıcaklık - zaman profili üç ayrı evreden oluşmaktadır.
•Isıtma zamanı
•Bekletme zamanı
•Soğutma zamanı
Isıtma zamanı içersinde istenilen östenitleme sıcaklığına çıkılmalıdır. Bu sıcaklıkta oluşan faz yapısında kiristal kafes dönüşümleri KHM KYM oluşmaktadır. Bu zaman içersinde östenik fazindaki kafes (KYM) yapısının on kat karbon absorblayabilecek şekilde mümkün olan en düşük östenitleme sıcaklığında olmalıdır. Diğer taraftan karbon absorblama değeri karbon konsantrasyonuna ve ısıtma hızına bağlıdır. Malzeme kritik sıcaklığın üzerine hızlı bir şekilde ısıtılmalıdır. Bu dönüşümler “zaman-sıcaklık- östenitleme” diyagramları ile açıklanmaktadır. Tüm farklı malzemeler bu diyagrama bağlı olarak temsil edilmektedir. (Şekil1)
Bekleme zamanı içersinde karbon atomları demir kafesinin içersine difüzyonla girer. Bekleme zamanında sertleşme istenilen tüm bölgede homojen östenit elde edilmesi açısından dikkatli bir şekilde ayarlanması gerekmektedir. Bu sıcaklıkta bekleme süresi yaklaşık olarak 0,001 sn ile 10 sn arasındadır. Bu evrede bekleme sıcaklığı belirlenmiş östenitleme sıcaklığından büyük seçilmelidir.
Soğutma zamanı da önemli bir parametredir. Eğer malzemenin soğutulması gereğinden çok yavaş gerçekleşirse karbon atomu difüzyona uğrayabilecek yeterli zamanı bulacak orijinal pozisyonuna dönecek, böylece istenilen sertleşme gerçekleşmeyecektir. Bu nedenle malzeme yeteri kadar hızlı bir şekilde soğutulmasıyla karbon atomu difüzyona uğrayabilecek zamanı bulamayacak orijinal pozisyonuna dönemeyecektir. Sonuç olarak karbon atomu demir atomunun kafes yapısında kilitlenip kalacaktır. (Şekil2) Bu yeni oluşan malzeme fazına martensit denmektedir. Bu yapıda karbon, demir atomları ile sarılıdır. Bu martensit fazı lazer sertleştirmede hedeflenen bir yapıdır. Bu yapı orijinal malzeme yüzey sertliğine kıyasla çok serttir. Ulaşılan sertlik malzemenin karbon kütle oranına bağlıdır ve değer 0,22% C oranından büyük olmalı ki makul sertlik artışı gerçekleşsin.
Lazer Sertleştirme
Yüzey sertleştirme prosesinde Yüksek Güçlü - Diyot lazer kullanılması halinde, prensip olarak belirlenen sıcaklık değerine çıkılması geleneksel yöntemlerde alev ve indükatör ile sağlanırken burada lazer işin kaynağı ile sağlanmaktadır.
Bununla birlikte lazer işin kaynağı ile sertleştirme yapmanın bazı karakteristik farkları vardır. Endüstride çok ilginç ve benzersiz spesifik uygulamaları vardır. Fonksiyonel parça dizaynın da Yüksek Güçlü- Diyot lazerle parça sertleştirme yeni olanaklar yaratmaktadır. Lazer setleştirme yönteminde sadece sertleştirilmek istenen bölgeler lazer ışınının bu bölgeyi taramasıyla sertleştirir. Isıl işlem yapılan parçanın diğer bölgelerinin mekanik özelliklerinde herhangi bir değişim olmaz. (Şekil 3)
Yüzey sertleştirme prosesinde Yüksek Güçlü-Diyot lazer yönteminin kullanılmasının birçok avantajı vardır. Bunlar geçici ısı girişleri ve lokal bölgelerde kontrol edilen ısı girişleridir. Sıcaklık artış hızı çok yüksektir. Yüksek Güçlü-Diyot lazer ısıl işlemi prosesinde sıcaklık artış hızı 1000K/s olarak gerçekleşmektedir. Yüksek ısıtma hızları, yüksek östenitleme sıcaklıkları sağlanmaktadır. Çok kısa sürelerde malzeme yüzeyi çok yüksek sıcaklıklara ulaşmaktadır. Parça yüzeyinde 900-1400 C° sıcaklık kontrolü, geçici ve lokal olarak belirlenen ısı girişleri sağlanır. Sonuç olarak düşük stres ve distorsiyon olmayan parçalar üretilmektedir. Çünkü Yüksek Güçlü-Diyot lazer ile sertleştirme de kontrol edilen lokal ısı girişleri, malzemenin ısı iletim katsayısına bağlı olarak malzeme gövdesine doğru gerçekleşen yeterli soğuma ile sertleşmenin sağlanması için gerekli soğuma zamanı oluşmaktadır. Bu nedenle ne suyla soğutma ne de yağla soğutma sistemlerine ihtiyaç yoktur. Gerekli olan ısı transferi malzeme bünyesinde sağlanmakta ve sertleşmenin gerçekleşmesi için üst kritik soğuma hızından daha yüksek hızda soğuma gerçekleşmektedir. Sonuç olarak bu bölgelerde homojen sertliklere erişilmektedir. Boyutu tanımlanan lazer ışık huzmesi parçaya odaklanmakta ve belirlenen hat boyunca oluşmaktadır. Lazer ışık huzmesinin odaklanması ve bu ışının tanımlanan belli bir hat boyunca ilerlemesi sonucunda ısıdan etkilenmiş lokal bir bölge oluşur. (Şekil 4) Isıdan etkilenmiş bu lokal bölgenin çevresindeki bölgeler lazer sertleştirme prosesinden etkilenmeyecektir. Bu proses teknik parçalarda benzersiz avantajlar ve olanaklar sağlamaktadır. Yeniden işleme ve ekstra temizlik gibi proseslere gerek kalmayacaktır. Isıl işlem yapılan alan boyunca hassas ve fonksiyonel yüksek sertlikler oluşacaktır.
Prosesin avantajları
•Isıl işlem hattı boyunca değişmeyen enerji yoğunluğu
•Hassas ve kısmi yüzey sertleştirme
•İdeal kristal yapı küçük tane boyutu ve homojen mikroyapı
•Kontrolü kolay proses
•Stabil proses
•Maliyeti yüksek soğutma sistemlerine ihtiyaç olmaması
•Minimum deformasyon ve az çekme payı
•Yüksek kalitede homojen sertlik
•Parça yüzeyinde sıcaklık kontrolü
•Erime tamamen ortadan kaldırılır.
Yüksek-Güçlü Diyot Lazer ile Sertleştirme Kontrolü Kolay Parametreler İçerir
Yüksek-Güçlü Diyot lazer bir lazer işin kaynağıdır. Yüzey sertleştirme prosesi için benzersiz kalitedir. Enerjinin malzemeye absorbe edilmesi açısından en verimli lazer kaynağıdır. Çelik malzeme yüzeylerinde bu enerji çok iyi absorbe olabilmektedir. Diyot lazer mükemmel takımlar için yüksek kapasitede güç değişimlerini yüksek hızlarda gerçekleştirmektedir. Bu özelliği ile et kalınlıkları farklı olan, keskin köşeler içeren parçalarda östenitleme sıcaklıklarının sabit kalabilmesi büyük avantaj sağlamaktadır.
Diyot lazerin elektro optik verimliliği diğer lazer kaynaklarına CO2 lazer ve Nd: YAG lazer kıyasla %35 fazladır. Diğer lazer kaynaklarına göre metal malzeme yüzeyinde absorblanma derecesi açısından yüksek değerler içerir. Bu değer yaklaşık olarak %40 ve CO2 lazere kıyasla çok iyidir. Şekil 5’de değişik lazer ışın kaynaklarının absorbe olma derecesinin karşılaştırmasını görmekteyiz.[4] D
Diyotlarda üretilen lazer ışını orantılı olarak kullanılabilmektedir. Eğer diyot güç sağlayıcısını ani olarak değiştirirseniz lazer çıkış gücüde aynı hızla değişecektir. Bunun gerçekleşmesi sisteme entegre edilen termal kamara yardımıyla sağlanmaktadır. Termal kamara parça yüzeyinde tanımlanmış olan östenitleme sıcaklığını çok hassas toleranslarda kontrol etmekte ve bu östenitleme sıcaklık değerini toleranslar mertebesinde de sabit tutmaktadır. Bu belirlenen östenitleme sıcaklık değerinin sabit kalmasını güç değişimiyle sağlamaktadır. Tanımlanmış hat boyunca diyotlardan uygulanması gereken güç değeri sertlik hattının genişliğine ve östenitleme sıcaklık değerine bağlıdır. (Şekil 6). Bir önemli durumda sertleştirme gerçekleştirilen alan boyunca oluşan oksit tabakasıdır. Bu oksit yüksek östenitleme sıcaklıklarında meydana gelmektedir. Bunun önlenmesi mümkündür.
Eğer sertleştirme sürecinde hat boyunca oksitlenmeyi engellemek için nitrojen veya argon gazıyla atmosfer teması kesilmelidir. Bu oksit tabakasının malzemenin sertlik kalitesine olumlu veya olumsuz bir etkisi yoktur. İstenirse zahmetsiz bir şekilde giderilebilir.
Önemli bir avantajı ise oluşan oksit tabakasının homojenliği oluşan sertlik tabakasının kalitesi konusunda bize bilgi vermesidir. (Şekil 7)
Kaynakça [1] V.I. Konov, S.V Garnov, O.M. Tzakova: Laser beam absorption of metals at process temparature. Moskov: General Physics Institute. [2] www.rofin.com [3] www.alotec.de [4] DILAS Dıodenlaser GmbH, S. Reinl: Thesis on ‘’ Surface HardeŞekil
. . .
İçerik sadece atıfta bulunularak yayınlanabilir: Sivas İş Dünyası. Editöryal görüş, yazarın görüşüne aykırı olabilir.