Gaz Tungsten Ark Kaynak Yöntemiyle AISI 304 Paslanmaz Çelik Düzeyinde üretilen M7C3 Takviyeli Kompozit Kaplamaların Mikroyapısı
Kaplamalar 105, 115, 125, 135 ve 145 amperlik farklı akımlarda gerçeklestirildi.
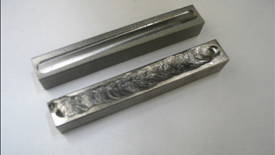
Kaplamalar 105, 115, 125, 135 ve 145 amperlik farklı akımlarda gerçeklestirildi.
Ayhan ORHAN ve Soner BUYTOZ
Fırat Üniversitesi, Teknik Egitim Fakültesi, Metal Egitimi Bölümü, 23119 Elazıg
[email protected]
Özet: Bu çalısmada; 66 Cr oranına sahip Fe-Cr-C tozu Gaz Tungsten Ark Kaynak yöntemi (GTA) ile 1,5 mm derinliginde AISI 304 Paslanmaz (ostenitik) çelik üzerine farklı islem parametreleri ile M7C3 karbür olusturulması incelendi.
Kaplamalar 105, 115, 125, 135 ve 145 amperlik farklı akımlarda gerçeklestirildi. Daha sonra kaplama-kaynak boncuklarına dik dogrultuda kesilerek metalografik incelemeler için numune hazırlandı. Numunelerin mikroyapıları, optik mikroskop ve taramalı elektron mikroskobu (SEM) ile incelenerek, faz ve karbürlerin tespiti için enerji dagılımlı spektograf (EDS) ve X ısını difraktogramından faydalanıldı. Yapılan incelemeler sonucunda; AISI 304 paslanmaz çelik üzerinde M7C3 karbürlerinin olustugu izlendi. Anahtar Kelimeler: AISI 304 Paslanmaz Çelik, FeCrC Tozu, M7C3 Karbür. Microstructure of M7C3 Reinforced Composite Coating Produced on the Surface AISI 304 Stainless Steel with Gas Tungsten Arc Welding Method
1. Giris
Ostenitik paslanmaz çelikler diger çeliklere nazaran korozyona ve oksidasyona karsı üstün bir direnç gösterdiklerinden, kimya ve petrokimya endüstrisinde genis bir uygulama alanına sahiplerdir. Ancak bu tür çeliklerin sertliklerinin ve asınmaya karsı performanslarının düsük olması nedeniyle bu tür çeliklerin yüzey özelliklerinin gelistirilmesi için yapılan yüzey islemleri günümüzde oldukça ilgi çekmektedir
[1,2,3]. Gaz tungsten ark yöntemiyle yapılan kaplama teknolojisi yeni bir yöntem degildir. Fakat yapılan islem bakımından, plazma, elektron ısın ve lazer kaynak yöntemlerine göre, üretimin çok daha kolay ve ucuz olması, istenilen bilesim ve oranlarda bir kaplama tabakasının elde edilebilmesi ve tabaka kalınlıgının daha fazla olması gibi birçok avantajlara sahiptir
[4]. Bu yöntemle elde edilen katmanların mikroyapılarında, ötektik ostenitik matrisinde çok yüksek sertlik degerlerine sahip M7C3 karbürleri, malzemeye olaganüstü bir dayanım verirler
[5]. Gaz tungsten ark yönteminde, kısa ara reaksiyon zamanında alt tabaka ve toza verilen yüksek enerji yogunluguyla hem toz partikülleri hem de alt tabaka malzemesinin yüzeyi ergitilir ve enerji yogunluguna baglı olarak, farklı soguma hızlarında katılasıp daha ince taneli mikroyapılar elde edilir
[6]. Kaplama tozunun tipi, boyutu, miktarıyla birlikte, alt tabakanın kimyasal bilesimleri de dikkate alınarak üst tabakanın makro yüzeyi daha pürüzsüz ve düzgün olabilir
[7,8]. Ergitme için uygulanan enerjiyle, alt tabakanın da yüzeyinin ergimesiyle, alt tabaka ile kaplama tabakası arasında metalurjik olarak kuvvetli bir bag olusur. Bu durum ise tamamıyla malzeme ve alasımların ıslatma özellikleriyle iliskilendirilmektedir
[9]. Yüksek Cr ( 15-26 Cr) oranına sahip alasımlar, sert ötektik öncesi ve/veya (östenit, martenzit, ferrit, perlit veya beynit gibi) daha yumusak bir demir matrisindeki ötektik M7C3 karbürleri genellikle yerinde kompozitler olarak isimlendirilir. Yüksek kromlu döküm alasımlarında gözlenen matris yapısı östenittir, fakat bu bazı ısıl islemler sonrası degisebilir. Buna ilaveten, bu alasımların yapısındaki karbürler tipik olarak M7C3 tipi (M=Fe,Cr) karbürlerdir
[10,11]. Bu yüzden, gaz tungsten ark ile yüzey kaplama yöntemi, malzemenin bölgesel olarak asınma ve korozyon direnci gibi özelliklerini iyilestirmek için tercih edilebilecek bir yöntemdir. Bu yöntemde, kaplama için esas malzeme ile bir tungsten elektrod arasında bir elektrik arkı olusturmak için gaz tungsten ark yöntemi kullanıldı. GTA yönteminde ark bölgesi argon asal gaz yardımıyla atmosferin ve çevrenin olumsuz etkilerinden korundu. Bu çalısmada da; FeCrC tozu, TIG kaynak yöntemiyle AISI 304 paslanmaz çelik yüzeyine farklı akımlarda kaplandı. Kaplama malzemesinden deney numuneleri elde edilerek mikroyapı özellikleri açısından kıyaslandı ve M7C3 tipi karbürlerin en uygun akımda yapılan kaplamada tespiti yapıldı.
2. Materyal ve Metot
Bu deneysel çalısmada, ortalama 60 μm tane boyutuna sahip yüksek kromlu ferrokrom karbon (FeCrC) tozuyla alt tabaka malzemesi olarak 100×14×14 mm ebatlarındaki AISI 304 ostenitik paslanmaz çeligi kullanıldı. Deneyde kullanılan FeCrC tozun ve ostenitik paslanmaz çeligin kimyasal bilesimleri Tablo 1’ de verilmistir. Kaplama öncesi toz partiküllerinin yüzeyde baglayıcı ile baglanarak karısımın homojen bir sekilde olusmasını saglamak için AISI 304 paslanmaz çeligine 1,5 mm derinliginde kanal açılmıstır (Sekil 1). Burada kaplama yapılan ve yapılmayan AISI 304 paslanmaz çelikler bir arada gösterilmistir. Mekanik temizleme islemlerinden sonra AISI 304 paslanmaz çeligin asetonla yüzeyleri yag ve kirden arındırılmıstır. Daha sonra Tablo 2’de belirtilen miktarlarda yüksek kromlu ferrokrom karbon tozu kanala verilerek kimyasal baglayıcı ile malzeme yüzeyine yapıstırılmıstır. Tungsten gazaltı kaynak yöntemi ile Tablo 2’de belirtilen parametreler dogrultusunda Sekil 2’de sematik resmi verilen mekanizma yardımıyla kaplamalar gaz tungsten ark kaynak torcuyla ergitilerek gerçeklestirilmistir. Kaplama sonrası malzeme yüzeylerinin makro görünüsleri Sekil 3’te gösterilmistir. Numunelerin daha kolay incelenmesi için deney numunelerine X1, X2, X3, X4 ve X5 adları verilmistir.
Tablo 1. Deneyde Kullanılan Malzemelerin Kimyasal Analizi
Malzeme Fe Cr C Si P S Mn Mo Cu Ni N
FeCrC 24,82 66,90 6,50 0,72 0,01 0,05 - - - - -
AISI 304 70,55 18,45 0,03 0,48 0,02 0,29 1,50 0,48 0,48 8,56 0,08
Gaz Tungsten Ark Kaynak Yöntemiyle AISI 304 Paslanmaz Çelik Yüzeyinde Üretilen M7C3 Takviyeli Kompozit Kaplamaların Mikroyapısı
Sekil 1. Kaplama Öncesi Alt Tabaka Malzemesinin Hazırlanmıs Durumdaki Numune Resmi
Tablo 2. Numunelerin Üretim Parametreleri
Numunenin X1 X2 X3 X4 X5
Toz Miktarı (gr) 3,432 3,655 3,360 3,715 3,498
Üretim Hızı (V) 56,497 60,014 68,113 66,153 69,252
Kaplama Boyu (mm) 80 83 85 86 78
Akım (amper) 105 115 125 135 145
Isı Girdisi (Q) 26,5 27,4 26,2 29,1 29,9
Islatma Oranı 87,05 82,99 82,05 79,87 70,70
Elektrod 2 toryumlu tungsten elektrod
Koruyucu gaz 99,9 saf Argon
Elektrod çapı 2,4 mm
Gaz akıs oranı 12 lt/dk
Islatma oranları asagıdaki formül yardımıyla hesaplanmıstır. Burada ölçümler optik mikroskobundan (A:Kaplamanın Yatay Mesafesi, B:Kaplamanın Düsey Mesafesi) tespit edilmistir. Isı girdisinin (Q) hesaplanmasında ise diger formül kullanıldı (U:Gerilim, I:Akım, n:Verimlilik Katsayısı, V:Üretim Hızı).
Sekil 2. Gaz Tungsten Ark Kaynak Yöntemiyle Yapılan Kaplama sleminin Sematigi
Sekil 3. Farklı Üretim Parametrelerinde Elde Edilen Kaplama Numunelerinin Makro Görünüsü
Metalografik incelemeler için kaplamakaynak boncuklarına dikey konumlarda kesilerek alınan numuneler, standart metalografik islemlerden geçirilerek, ferrik klorid asit çözeltisinde (25 gram FeCl3, 15 ml HCl ve 100 ml saf su) daglanmıslardır. Numunelerin mikroyapıları, optik mikroskop ve taramalı elektron mikroskobu (SEM) ile incelenerek, faz ve karbürlerin tespiti için enerji dagılımlı spektograf (EDS) ve X ısını difraktogramından faydalanılmıstır. 3. Sonuçlar ve Tartısma Optik resimleri genel olarak incelendiginde FeCrC tozlarının ergimeleri artan akıma baglı olarak artmıstır. Sekil 4, 5 ve 6’da görüldügü gibi düsük akımdaki topaklasmalar oldukça fazladır. Topaklasmanın olusması, yeterli sürenin kaynaklanmamasından dolayı meydana gelmektedir. Üretim hızları yaklasık olarak birbirlerine yakın olmasına ragmen akımın düsük olması nedeniyle ergime tam gerçeklesememektedir. Buda tam olarak çözünmeyen FeCrC tozlarının varlıgına neden olmaktadır. Ayrıca aynı sekiller incelendiginde artan akıma baglı olarak dentritik kollarının olusmaya basladıgı görülmektedir. Bu tespitimiz Sekil 7a, 7b ve 7c’deki kaplama-kaynak boncuklarına bakıldıgında da desteklenmektedir.
Sekil 4. 105 Amperde Yapılan GTA Kaplaması
Sekil 5. 115 Amperde Yapılan GTA Kaplaması
Sekil 6. 125 Amperde Yapılan GTA Kaplaması Gaz Tungsten Ark Kaynak Yöntemiyle AISI 304 Paslanmaz Çelik Yüzeyinde Üretilen M7C3 Takviyeli Kompozit Kaplamaların Mikroyapısı 597 (a)105 Amper (b)115 Amper (c)125 Amper Sekil
Sekil 8 ve 9’daki optik mikroskop görüntülerine bakıldıgında 135 amperde yapılan kaplamadaki dentrit kollarının daha düzenli oldugu görülmektedir.
Sekil 9’da optik resmi verilen 145 amperlik GTA kaplamanın yüksek ampere baglı olarak denritik kollarının homojen olmadıgı ve kısmen bozuldugu görülmektedir. Sekil 10a ve 10b’deki kaplama-kaynak boncuklarına bakıldıgında ise 135 amperde yapılan GTA kaplamasının daha düzenli oldugu görülmektedir. Ancak 145 amperde yapılan kaplamın yüksek akıma baglı olarak ergimenin daha fazla oldugu ve kaplamakaynak boncukların ise yok denecek kadar az oldugu tespit edilmistir.
Sekil 8.135 Amperde Yapılan GTA Kaplaması
Sekil 9. 145 Amperde Yapılan GTA Kaplaması
Sekil 10. Kaplama-Kaynak Boncuklarının Üstten Makro Görüntüsü
Optik mikroskop resimlerinin ve kaplamakaynak boncuklarının makro görüntülerinin incelemeleri sonucu 1,5 mm derinligindeki AISI 304 paslanmaz çelik üzerindeki FeCrC tozunu GTA kaplama ile en uygun 135 amperlik akımla yapılacagı tespit edildi. Bu dogrultuda X4 numunesinde olusan intermetalik fazların ve olusan karbürlerin tespiti yapıldı. Sekil 11’de görüldügü gibi X4 numunesinin kaplama sınırı görüntüsü bulunmaktadır. Bu bölge incelendiginde AISI 304 paslanmaz çelik tarafından ergimeye baglı olarak malzeme difüzyonu kaplama bölgesine taraf olusmaktadır. Kaplama bölgesinin sınırından alınan EDS analizi de bunu dogrulamaktadır. EDS analizinin açık gösterimi Tablo 3’te görülmektedir. Tablo 3. X4 Numunesinin EDS Analizi
X4 numunesinin SEM görüntüleri incelendiginde ise M7C3 karbürlerinin oldukça fazla oldugu izlendi. FeCrC tanelerinin üretim hızının yüksek olmasına baglı olarak tanelerin bazıları ergiyik banyo içinde erimeden kalmıstır. Buna baglı olarak üretim hızının yüksek olması ve FeCrC tanelerinin çoklugu nedeniyle ergimenin tam manasıyla gerçeklesememesi sonucunda çesitli karbürler seklinde çökelme olusmaktadır
[12]. Bu nedenle GTA kaplama yöntemiyle sertlestirme yapılan bölgede verilen enerji girdisi ve üretin hızına baglı olarak yeterli sürenin eksikligi nedeniyle kaynak banyosunda ergime ve yeniden kristallesme tam manasıyla olusmadıgı kanaatine varılabilir. Zaten Sekil 12 incelendiginde ise homojen olarak bir karbür olusumu oldugu anlasılmaktadır. Olusan bu karbürlerin türünü belirlemek için X4 numunesine XRD analizi yapılmıstır. XRD analizi 30 kV ve 15 mA’de CuKa radyasyonu kullanılarak Rigaku Geigerflex X-ısını difraktometresi ile elde edilmistir. XRD sonucu Sekil 13’te gösterilmistir.
Sekil 11. X4 Numunesinin Kaplama Sınır Bölgesi ve EDS Analizi Sekil 12. X4 Numunesinin Karbürlü Bölgelerin SEM Görüntüsü
Sekil 13. X4 Numunesinin Karbürlü Bölgelerinin XRD Analizi 4. Genel Sonuçlar AISI 304 ostenitik paslanmaz çelik üzerine farklı miktar, akım ve üretim hızlarında GTA kaynak yöntemiyle FeCrC tozunun yüzey kaplamasında sonuç olarak; en uygun yüzey modifikasyonunun 135 A’lik akımda yapılan kaplama oldugu, kaplama sınır bölgesinde malzeme difüzyonunun oldugu, denritik yapının eldesi için uygun kaynak akımının gerektigi, karbürlerin olustugu ve bu karbür türünün M7C3 tipi (M=Fe,Cr) karbürler oldugu ve olusan karbürlerin malzemedeki dagılımının homojen oldugu, tespit edilmistir.
Sonuç olarak; kaplama yapılan AISI 304 ostenitik paslanmaz çelik malzemesinin katılasma hızına baglı olarak elde edilen yapının, malzemenin kullanım alanlarına göre genisletilebilecegi düsünülmektedir.
5. Kaynaklar
[1] Hwan, S., Park C., Sato, Y.S., Kokawa, H., Okamoto, K., Hirano, S., Inagaki, M., (2004), “Corrosion resistance of friction stir welded 304 stainless steel”, Scripta Materialia, (51)101-105. [2] Tsay, L.W., Liu, Y.C., Young, M.C., Lin, D.Y., (2004), “Fatigue crack growth of AISI 304 stainless steel welds in air and hydrogen”, Materials Science and Engineering A, 374, (1-2), 204-210. [3] Riviere, J.P., Meheust, P., Villain, J.P., (2002), “Wear resistance after low-energy high-flux nitrogen implantation of AISI 304L stainless steel”, Surface and Coatings Technology, (158-159), 647- 652. [4] Buytoz, S., Yildirim, M.M., Eren, H., (2005), “Microstructural and microhardness characteristics of gas tungsten are synthesized Fe–Cr–C coating on AISI 4340”, Materials Letters, (59), 607-614. [5] Buytoz, S., (2006), “Microstructural properties of M7C3 eutectic carbides in a Fe–Cr–C alloy”, Materials Letters, (60), 605-608. [6] Nagarathnam, K., Komvopoulos, K., (1995), Metall Mater. Trans A, (26), 2131–2139. [7] Buytoz, S., (2004), Fırat üniv Fen Bil.Enst., Doktora Tezi. [8] Zhong, M., Liu, W., Zhang, H., (2006), Corrosion and wear resistance characteristics of NiCr coating by laser alloying with powder feeding on grey iron liner”, Wear, (260), 1349-1355. [9] Buytoz, S., (2006), “Microstructural properties of SiC based hardfacing on low alloy steel”, Surface and Coating Technology, (200), 3734-3742. [10] Maratray, F., (1971), AFS Trans., (79), 121-24. [11] Parks, J.L., (1978), AFS Trans., (86), 93-102. [12] Lou D., Hellman, J., Luhulima, D., Liimatainen, J.,. Lindroos, V.K, (2003), “Interactions between tungsten carbide (WC) particulates and metal matrix in WC-reinforced composites”, Materials Science and Engineering A, (340), 155–162.
. . .
İçerik sadece atıfta bulunularak yayınlanabilir: Sivas İş Dünyası. Editöryal görüş, yazarın görüşüne aykırı olabilir.