Sünger Demirin Ergitilmesi Sonrası Metal Formun Ve Curufun Karakterizyonu
Kocaeli Üniversitesi, Metalurji ve Malzeme Müh., Umuttepe Yerleşkesi, 41380, Kocaeli
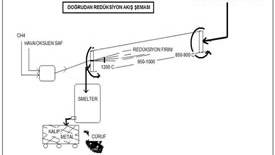
Kocaeli Üniversitesi, Metalurji ve Malzeme Müh., Umuttepe Yerleşkesi, 41380, Kocaeli
Kocaeli Üniversitesi, Metalurji ve Malzeme Müh., Umuttepe Yerleşkesi, 41380, Kocaeli
Özet
Bu çalışmada, atık malzemesi olan hadde tufalinin gaz ve katı indirgeyiciler kullanılarak indirgenmesi ve böylece sünger demirin üretimi üzerinde durulmuştur. Sünger demirin ergitme işlemi sonrası katı metal ve curuf oluşumu irdelenmiştir ve metal ve curufun karakterizasyonu yapılmıştır. Metal ve curuf üzerine tarama elektron mikroskobu ile görüntüleme ve enerji dispersif spektrometre ile elementel analiz gerçekleştirilmiştir. Curuf bileşenleri elementel içeriklerine göre tanımlanmıştır.
Anahtar kelimeler : Sünger demir, indirgeme, curuf, karakterizasyon
CHARACTERIZATION OF METAL FORM AND SLAG AFTER SPONGE IRON MELTING
Abstract
In this study, the reduction of oxide layer as waste material by using gas and solid reductants and consequently the production of sponge iron were emphasized. The formation of solid metal and slag after melting process of sponge iron was considered and characterization of metal and slag was done. Imaging by scanning electron microscope and elemental analysis by energy dispersive spectrometre were performed on metal and slag. Slag components were defined according to their elemental content.
Key words : Sponge iron, reduction, slag, characterization
1. Giriş
Demir çelik sektörü ülke ekonomilerinin kalkınmasında lokomotif sektörler içinde yer almaktadır. Yapılan çalışmaların büyük bir kısmı, demir-çelik üretim teknolojisinde radikal değişimlerden ziyade var olan tesislerin optimum şekilde çalıştırılması üzerinedir [1, 2]. Üretim sonrası nihai demir-çelik ürünlerinin, kullanım şartlarına ve hedeflenen koşullara bağlı olarak birçok üstün fiziksel ve kimyasal özelliklere de sahip olması arzulanır [3, 4]. Çelik üretimi için birden çok proses geçmişten günümüze kullanılmıştır. Bu prosesler basit bir şekilde iki gruba ayrılabilir: (a) cevherden çelik üretimi ve (b) hurdadan çelik üretimi. Ekonomiklik kriteri olarak enerji sarfiyatı söz konusu iken hurdadan çelik üretimi şüphesiz vazgeçilmez bir tekniktir. Ancak günümüz çeliklerinde yüksek kalite, homojen mikroyapı ve ideal mekanik özelliklerin sağlanabilmesi amacı ile daha da yüksek maliyet gerektiren yöntemlere başvurulmuştur. Bununla birlikte yüksek kalite çeliklerin üretimi sırasında atık malzemelerin (curuf, hadde tufali vb.) açığa çıkması ve yüksek tonajlarda olması önemli bir ekonomik kayıp olup aynı zamanda metalurjik ve çevre problemidir. Atık malzemeden geri kazanım yolu ile sünger demirin eldesi ve bu malzemenin çelik üretimine katkı sağlayarak ekonomik anlam kazanması da günümüz araştırma konuları arasında yer almaktadır [5].
Katı ve gaz indirgeyicilerin, cevher başta olmak üzere curuf ve hadde tufali gibi atık malzemeler ile belirli sıcaklık aralıklarında çoklu reaksiyonları sonrasında gözenekli yapılı sünger demir oluşumu söz konusudur. Üretilen sünger demirin ergitilmesi ve tekrar curuf ayrımının sağlanarak yüksek demir içerikli metal bileşeni olarak çelik üretimine bir hammadde olarak tedarik edilmesi, kaliteli çeliğe giden çevrimde önemli bir unsurdur [6, 7]. Demir-çelik üretiminin büyük bir kısmı yüksek fırın ve elektrik ark fırın teknolojisi ile sağlanmaktadır. Birçok çelik üreticisi, sünger demiri elektrik ark fırınlarına şarj malzemesi olarak kullanmaktadır [8]. Artan hurda fiyatları da göz önüne alınacak olursa kaliteli çelik üretiminde hurdanın yerini sünger demir almaktadır. Direkt redüklenmiş sünger demir ve sıcak briketlenmiş sünger demir günümüzde birçok ülke tarafından yüksek fırın şarj malzemesi olan pelet ve sinterin yerine kullanılmaya başlanmıştır [9, 10].
Bu çalışmada, katı ve gaz indirgeyici karışıı ile redüklenmiş hadde tufalinden başlangıçta sünger demir üretimi gerçekleştirilmiş olup sünger demirin ergitilmesi sonrası metal ve curuf ayrışımı yapılmıştır. Katı metal formu ve curuf üzerine yapılan mikroanalitik çalışmalar redükleme, ergitme, katılaşma ve curuf bileşenleri hakkında genel sonuçların belirlenmesine katkı sağlamıştır.
2. Deneysel Çalışma
2.1. Malzeme ve Yöntem
Deneysel çalışmada, demir-çelik tesisi atığı olan hadde tufali, karbon (kömür) ve hidrojen gazı (H2) ile birlikte döner fırın içerisinde redükte edilmiştir. Redüksiyon sonrası elde edilen sünger demir, elektrik ark sistemiyle ısıtılan bir ergitme sisteminde ergitilmiş curuf giderimi sonrası kalıplara dökülmüştür. Bu işlemler sonrasında ise katı metal formu ve curuf üzerine mikroanalitik bir çalışma gerçekleştirilmiştir.
Döner fırına şarj malzemesi olarak hadde tufali, curuf yapıcılar ve kömür ilave edilmiştir. 1 ton şarja yüklenen hammaddelere ait yüzde () değerleri Tablo 1’de verilmiştir. Curuf yapıcı içeriği ise bentonit, kireç taşı ve dolomit olup 20 kg olarak şarja ilave edilmiştir ve ilgili yüzde () değerleri Tablo 2’de verilmiştir. Proses için hammadde olan tufalin, gerekli tane boyutuna indirilebilmesi için değirmende kuru öğütme yapılmış olup, proses de kullanılan tufalin tane boyutu 400-500 µm arasındadır. Gaz redüktant olarak kullanılan hidrojenin kaynağı LNG doğal gazdır. LNG’nin yanma ile parçalanması sonrası oluşan gaz karışımında ise minimum 95 H2 gazı mevcuttur. Redükleme işlemi, Şekil 1’de şematik olarak verilen bir düzenekte gerçekleştirilmiş olup proses işletme basıncı 101325-110200 Pa arasında ölçülmüştür. İndirgenme ile oluşan sünger demir 1200-1400 °C sıcaklıklarına elektrik ark sistemiyle ısıtılıp ergitilmekte ve sonrasında metal ile curuf fazları ayrıştırılmaktadır.
Tablo1. Şarj hammaddeleri ve şarjın miktarı ile yüzdesel içeriği.
Şarj
Hammadde
Tufal 76.38
Kömür 22.06
Curuf Yapıcı 1.550
Tablo 2. Curuf yapıcı bileşenlerin miktarı ve yüzdesel içeriği.
Curuf yapıcılar
Bileşen
Bentonit 10
Kireç Taşı 50
Dolomit 40
Şekil 1. Doğrudan redüksiyon akış şeması ile prosesin modellenmesi.
Hadde tufali üzerine özellikle demirin tayini için ise X-ışınları floresans (XRF) analizi yapılmıştır. Şekil 2’de bu analize ait spektrum ve Tablo 3’de spektrum üzerinden alınan elementel dağılım yüzdesel olarak verilmiştir. Yüzdesel elementel dağılım göz önüne alınacak olunursa, demir ve oksijen içeriğinin oldukça yüksek olduğu ve özellikle Mn, Si ve Cr gibi kompleks oksit oluşuturucu elementlerin de tufal içerisinde var olduğu belirlenmiştir.
Şekil 2. Hadde tufaline ait XRF analizi.
Tablo 3. XRF analizinin elementel dağılımı.
Element Konstantrasyon-
Fe 69.1
Mn 0.66
Si 0.11
Cr 0.10
O 30.13
2.2. Metal Formu Üzerine Mikroanalitik Çalışma
Redüksiyon proseslerinde -metalizasyon oldukça önemli bir kavramdır. Deneysel çalışmada elde edilen sünger demir içeriğindeki metalik demir sistemin verimini ve hammaddenin indirgenebilirliğinin bir göstergesidir. Elde edilen sünger demirin ergitilip, curufun ayrılmasıyla elde edilen metalik ürünün tarama elektron mikroskop (SEM) görüntüsü ve elementel dağılıma ilişkin enerji dispersif spektrometre (EDS) ile belirlenen spektrum Şekil 3a ve b’de verilmişir. SEM görüntüsündeki siyah bölgeler kömürden gelen karbonca zengin bölgeleri göstermekte olup alansal EDS spektrumu karbon oranını 5 olarak göstermektedir. Başlangıç XRF analizinde demir miktarı 69.1 olarak tayin edilmiştir. Ancak indirgenen hadde tufalinin reaksiyon ürünü olan sünger demirin ergitme sonrası katılaştırılmış formu 86.5 miktarında demir içermektedir. Bu ise prosesleme koşullarında redükleme koşullarının iyi bir seviyede olduğunu ve metalizasyon derecesinin yüksek olduğunu işaret etmektedir.
2.3. Curuf Üzerine Mikroanalitik Çalışma
Ergitilen sünger demirden ayrıştırılan curufun SEM görüntüsü ve alansal spektrum örneği Şekil 4a ve b’de verilmiştir. Katılaşmış curufta beyaz kontrast ile köşeli ve iğnesel morfolojide baskın bir bileşenin ve çoğunlukla daha koyu kontrastlarda gözlenen ikincil bir bileşenin var olduğu gözlenmektedir (Şekil 4a). Tüm bu bileşenler curufun doğası (yapısı) gereği farklı oksit esaslı bileşenlerdir. Şekil 4b’de verilen EDS spektrumu yapıdaki oksitlerin büyük çoğunluğunun demir oksitten oluştuğunu ve yapıda ayrıca ağırlık yüzdeleri de dikkate alınarak Al, Si ve Ca içerikli kompleks oksitlerin var olabileceğini işaret etmektedir.
Daha yüksek büyütmeli SEM görüntüsünde curufun farklı bölgelerinde yapılan EDS analizleri Şekil 5’ de verilmiştir. Açık kontrastta ve ana matriksi gösteren 1. bölgeden alınan analiz spektrumu, yüksek demir ve oksijen içeriğiyle tipik bir demir oksit yapısının varolduğunu ve stokiometrisi göz önüne alındığında Wüstit (FeO) fazının baskın bir şekilde curufu oluşturduğu belirlenmiştir. Koyu konrastlı 2. bölgeden alınan analizde ise yapı silisyum ve kalsiyumca zengin olan bir oksit yapısını sergilemektedir. Silisyum çeliklerde bilindiği üzere bir taraftan katı ergiyik sertleştirici olarak görev alırken, diğer taraftanda özellikle döküm koşullarında iyi bir deoksidant olup curuf yapıcı element olarak da katkı sağlar. Kalsiyum katkısı ile gerçekleştirilen kalsiyum işlemleme ise özellikle yüksek kalite çeliklerin üretiminde gerekli olan ve çeliğin minimum seviyede empürite içermesine aktif katkı sağlayan bir proseslemedir. Matriks içerisinde 3. bölgenin ise ilgili elementel dağılımınında bir göstergesi olarak bakırca zengin tipik bakır oksit yapısı olduğu görülmektedir. 4. bölge reaksiyona kısmen girmeyerek sistemde çeşitli empürite atomları ile birlikte bulunabilen oldukça ince bir kömür taneciğini göstermektedir.
(a)
(b)
Şekil 3. (a) Hadde tufalinin indirgenmesi ile hammadde haline getirilen sünger demirin ergitilmesi sonrasında elde edilen döküm örneğine ait SEM görüntüsü, (b) görüntüsü verilen alana ait elementel dağılımı gösteren EDS spektrumu.
(a)
(b)
Şekil 4. Sünger demirin ergitilmesi sonrası curufuna ait SEM görüntüsü, (b) görüntüsü verilen alana ait elementel dağılımı gösteren EDS spektrumu.
(a)
(b)
(c)
(d)
(e)
Şekil 5. (a) Curufa ait SEM görüntüsü ve matriks içerisinde işaretlenmiş (b) 1. bölgenin, (c) 2. bölgenin, (d) 3. bölgenin, (e) 4. bölgenin EDS analizleri.
3. Sonuçlar
Deneysel çalışmada, katı ve gaz indirgeyiciler birlikte kullanılarak, döner bir fırında redükleme işlemi sonrası sünger demir üretilmiştir. Sünger demirin ergitilmesi ile birlikte katı metal formu ve curuf üzerine yapılan mikroanalitik çalışmalar ile redükleme ve ergitme potansiyelinin yanı sıra özellikle metal-curuf ayrışım potansiyeli de değerlendirilmiştir. Böylelikle yüksek kalite çelik üretiminde alternatif bir ham madde olarak sünger demirin etkinliği irdelenmiştir.
Katılaşan metal formun çoğunlukla yüksek demir içermesi, redükleme koşulları ile birlikte sünger demirin yüksek metalizasyon karakteristiği gösterdiğini işaret etmektedir. Empürite içeriğinin düşük oranda olması ise bu gözlemleri destekleyecek niteliktedir. Çalışma kapsamında, curuf karakterizasyonu da yapılmış olup curuf içerisinde çoğunlukla demir esaslı oksitlere ek olarak bakır oksit ve demir-aluminyum-kalsiyum-silisyum kompleks oksit yapıları belirlenmiştir. Redükleme ile birlikte tam olarak reksiyona girmeyen ve yüksek karbon içeriğine sahip kömür tanecikleri curuf içerisinde yer alıp ana metal formundan uzaklaştırılmıştır. Bu durumda metalin curuftan rafinasyonunun ideal konumda olduğu gözlenmiştir. Yapılan mikroanalitik çalışma, gerek redükleme koşullarının gerekse de ergitme sonrası metal-curuf ayrışımının başarılı bir şekilde gerçekleştirilmesi halinde çelik üretiminde hammadde olarak sünger demir proseslemesi ve kullanılabilirliği üzerine önemli yaklaşımlar sunmaktadır.
Kaynakça
[1] Türkiyede Demir Çelik Sektörü [online], www.kobifinans.com/sektor
[2] Manning, C. P., Fruehan, R. J., ‘Emerging Technologies for Iron and Steelmaking’, Journal of the Minerals, Metals and Materials Society, 53(10), p. 20-23, 2001.
[3] Dobrzański, L. A., Kowalskiand, M., Madejski, J., ‘Methodology of the mechanical properties prediction for the metallurgical products from the engineering steels using the artificial intelligence methods’, Journal of Materials Processing Technology, 164-165, p.1500-1509, 2005.
[4] Johnson, A. A., Storey, R. J., ‘The impact fatigue properties of iron and steel’, Journal of Sound and Vibration, 308(3-5) , p.458-466, 2007.
[5] Takla, N. D., ‘Utilization of sponge iron in electric arc furnaces’, Direct from MIDREX 2nd Quarter, p.3-6, 1999.
[6] Sponge iron industry, Comprehensive Industry Documents Series : COINDS/66/2006-07, Central Pollution Control Board Ministry of Environment & Forests, March, 2007.
[7] http://www.midrex.com/uploads/documents/MIDREXStatsBook2008.pdf
[8] Gojić, M., Koźuh, S., ‘Development of direct reduction processes and smelting reduction processes for the steel production’, Chemistry in Industry, 55(1), p.1-10, 2006.
[9] Li, J., Barati, M., ‘Kinetics and mechanism of decarburization and melting of direct-reduced iron pellets in slag’, Metallurgical and Materials Transactions B, 40(1), p.17-24, 2008.
[9] Kaushik, P., Fruehan, R. J., ‘Behavior of direct reduced iron and hot briquetted iron in the upper blast furnace shaft: Part II. A model of oxidation’, Metallurgical and Material Transaction B, 37(5), p.727-732, 2006.
[10] Anameric, B., Kawatra, S. K., ‘Properties and features of direct reduced iron’, Mineral Processing & Extractive Metallurgy Review, 28, p.59-116, 2007.
. . .
İçerik sadece atıfta bulunularak yayınlanabilir: Sivas İş Dünyası. Editöryal görüş, yazarın görüşüne aykırı olabilir.