Paslanmaz çelik üretim aşamaları ve gündelik hayatımızda proses teknolojilerinde kullanılan malzeme grupları
Geçen sayımızda sizlere genel hatları ile “Paslanmaz Nedir?” sorusunun cevaplarını vermeye çalıştık, bu ayki sayının bize ayrılan bölümünde paslanmaz çelik üretim aşamaları ile gündelik hayatımızda proses teknolojilerinde kullanılan malzeme gruplarını ve birbirlerinde nasıl ayırt edilerek değerlendirme…
Geçen sayımızda sizlere genel hatları ile “Paslanmaz Nedir?” sorusunun cevaplarını vermeye çalıştık, bu ayki sayının bize ayrılan bölümünde paslanmaz çelik üretim aşamaları ile gündelik hayatımızda proses teknolojilerinde kullanılan malzeme gruplarını ve birbirlerinde nasıl ayırt edilerek değerlendirme sürecine alındıklarını inceleyeceğiz.
Paslanmaz çelik dünyada üretimi çok önemli seviyelerde günümüz sayısal verileri ışığında ulaştığı nokta aşağıdaki grafikte gösterilmiştir.
PASLANMAZ ÇELİK ÜRETİMİ
2 TÜM ÇELİK ÜRETİMİNİN 2’SİDİR.

Grafik özellikle bu denli önemli olan ve çok çeşitlilik arz eden bu çelik grubunun talep edilmesi durumundaki arz dengesi hakkında bir somut veri sunmaktadır. Üretim dünya geneline bakıldığında belli başlı ülkelerin dışında kıta dağılımları göstermektedir. En baştaki sayılabilecek Avrupa, Amerika, Güney Afrika, Hindistan ve Uzakdoğu’da ise Çin, Kore, Japonya sıralamaları gelmektedir. Bu tablolar ışığında genel itibarı ile Paslanmaz üretim segmentleri bu kıtalar ve ülkeler arasında ayrı bir dağılım gösterse de ülkelerin teknolojik olarak bu konu hakkında tarihsel ve bilgi teknolojileri yatırımları dahilinde ortak noktaları da bulunmaktadır. Paslanmaz malzeme veya paslanmaz çelik kullanım olgusu özellikle insan düşüncesinin genişliği kadar kendine ait bir kullanım saha genişliğini kazanmıştır. Biz bu yazıda başlıca kullanım alanlarında yer alan ürünlerin hem kendilerini tanımlayacağız, hem de bu tanımlar ışığında teknik özellikleri ve nasıl ayırt edilebilecekleri konusunda bilgiler vermeye çalışacağız. Paslanmaz çelik üretimi gereği pek çok üretim safhasından geçmektedir. Ana hammaddesi bir önceki yazımızda bahsettiğimiz üzere pek çok alaşım oluşumunu gerçekleştiren metal elementleridir. Bu elementler doğa’da bulunmasına karşın daha önce üretilen ve kullanım sahalarında sadece fonksiyonel olarak işlevini yitirmiş bir başka deyimle artık “hurda” olarak tanımlanabilecek materyallerin büyük bir bölümü de ana hammadde olarak değerlendirilebilir. Dünya geneline bakıldığında bu önem arz eden geri dönüşüm olgusu imalat aşamalarının en önemli başlangıç safhasını oluşturmaktadır. Üretim başlangıcında üretimi planlanan materyalin azami nispette 75’i hurda olarak bu prosesinin girdi birimi olarak yerini almaktadır.
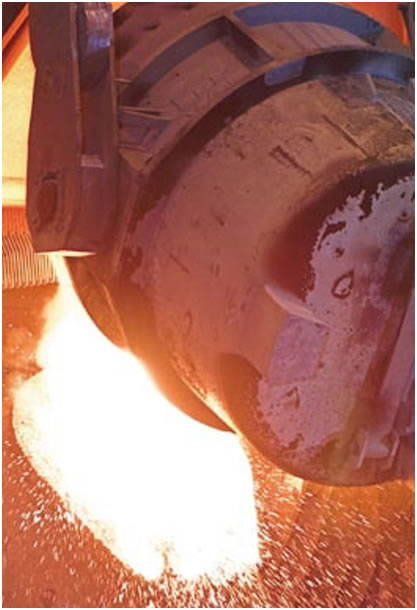
Yukarıdaki resimlerde yer alan aplikasyonlarda üretim sahalarından birkaç örnekleme görülmektedir. Paslanmaz üretimi anlaşılacağı üzere özellikle ileri teknoloji gereksinimi duyulan bir prosestir ki dünya genelinde sınırlı ülkelerde gerçekleştirilebilmesinin asıl nedeni budur.
Paslanmaz genel olarak hammadde kapsamı olarak bakıldığında sac veya kütük-külçe-gibi fiziksel formlarda üretilip proseste yer alan amaç üretimine doğru kanalize edilmektedir. Özellikle paslanmaz çelik için amaçlanan kullanım sahası bu hammaddelere verilecek nihai formların başlangıç adımını oluşturmaktadır. Bu bölümde proses teknolojilerinin en önemli ve başlangıç noktasını teşkil eden asli ürün saclar ve buna bağlı olarak klasifikasyonlarıdır. Dünyada fiziki üretime bağlı olarak değişik ebat ve formlarda paslanmaz çelik sac tanımları mevcutsa da aşağıdaki tablo genel hatları ile ürün odaklı spekleri açıklamada yardımcı olmaktadır.
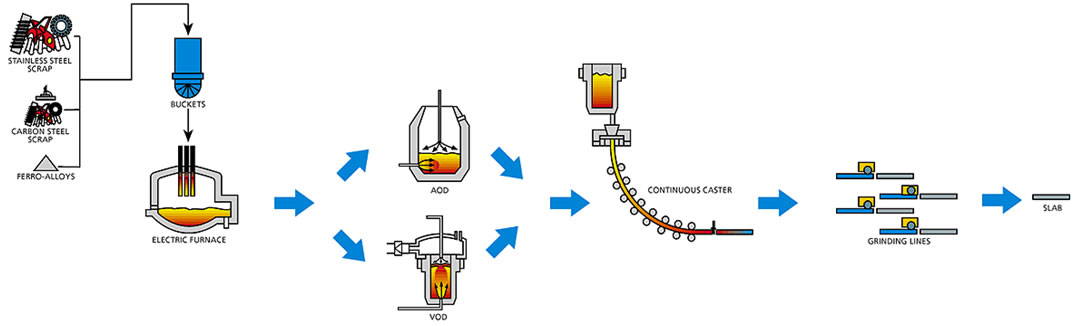
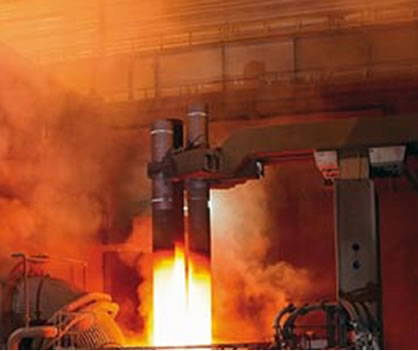
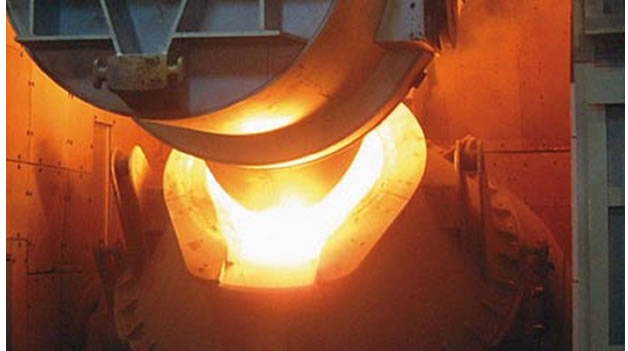
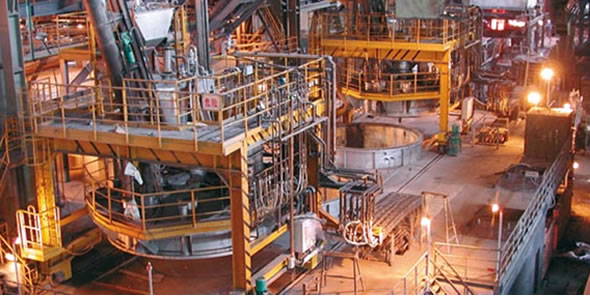
Paslanmaz Çeliklerin Yüzey Kaliteleri
EN 1088-2 ASTM SICAK HADDELENMİŞ
1D NO - 1 Sıcak haddelenmiş DKP edilmiş
1D Sıcak haddelenmiş, DKP edilmiş ve hafifçe soğuk redüksiyon uygulanmış, pasivize edilmiş, pürüzlü olabilecek yüzey kalitesi
SOĞUK HADDELENMİŞ
2D 2D Soğuk haddelenmiş, DKP edilmiş
2B 2B Soğuk haddelenmiş, DKP edilmiş ve skin pas uygulanmış, pasivize edilmiş(en çok kullanılan yüzey kalitesi)
2R BA Soğuk haddelenmiş, armosfer kontrollü dikey tip tav fırında tavlanmış
TAŞLANMIŞ
2J NO - 3 80-120 grain-tane- taşlanmış
2J NO - 4 150-400 grain-tane- taşlanmış
2J HL 150-250 grain-tane dikey-hair taşlanmış
DESENLİ
2M Emboss Soğuk haddelenmiş, taşlanmış
SERTLEŞTİRİLMİŞ
2H 1/4, 1/2, 3/4, 4/4 sert 2D yüzeyin 10-45 arasında çekme mukavemeti arttırılmış
ÖZEL YÜZEYLER
D1-Deri [2M] D3-Kare [2M] CH-Zemin [2M]
D2-Nokta [2M] D4-Çapraz Kare [2M]
taşlanmış, fırçalanmaş
Özellik olarak dünyada pekçok kalite değerinde paslanmaz çelik bulunmasına karşın Ostenitik grubun en önemli üyelerinden 304 ve 316 Paslanmaz çeliklerinin tüketimleri de bu malzeme gruplarının bir alt segmentini meydana getirmektedir.
AVRUPA TÜKETİMİ DÜNYA TÜKETİMİ
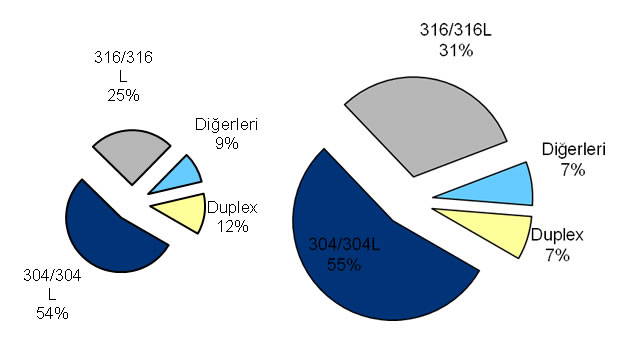
Bir alt not olarak vermek gerekirse grafiklerde bahsedilen Dublex ve Super Dublex yeni jenerasyon Paslanmaz Çelik konularına da ayrıca ileriki kısımlarda değinilecektir.
Bu aşamada genel olarak bir proseste en çok bahsi geçen ve kullanım sahasına sahip olan ürünleri genel olarak inceleyeceğiz, bu konuların başında borular ve buna bağlı olarak bağlantı elemanları yani fittingsler karşılık gelmektedir.
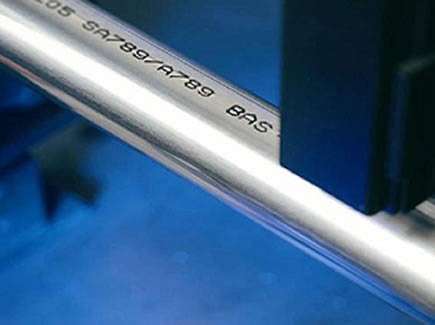
Paslanmaz Çelik borular başlıca iki ana grup altında incelenmektedir. Bunlardan birincisi ki bugün için dünyada 80 kullanım sahasına sahiptir, dikişli veya boyuna kaynaklı borular, ikincisi dikişsiz olarak yani çekme tabiri ile ifade edilen borulardır.
Kısaca çekme borular iki farklı üretim metodu ile imal edilirler birincisi sıcak olarak çekilme, ikincisi ise soğuk olarak yani mekaniksel gergi metodu ile imal edilme, aşağıda bu aşamaları kısaca özetleyen bir çizim dizaynı bulunmaktadır.
Üst resimde kırmızı olarak ifade edilen ekskürsiyon işleminde sıcak çekim metodu ifade edilmiştir. Alt kısım ise mekanik gergi metodu ile yapılan bir soğuk çekim uygulama örneğidir.
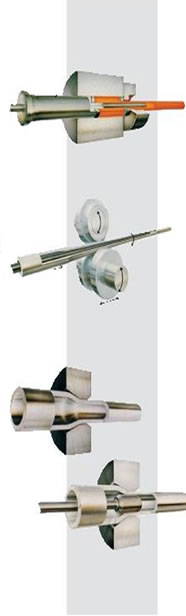
Tüm borular genel olarak içindeki element dağılımlarına bağlı olarak değişik malzeme kalitelerinden imal edilebilirler, yukarıdaki paragraflarda belirttiğimiz gibi en yaygın kullanım sahasına sahip AISI 304 AISI 316 gibi malzemeler ticari olarak piyasada daha kolay bulunabilme unsurlarını yerine getirmektedirler.
Dikişli borular esas olarak 2B saclardan imal edilmekle beraber daha önceden bir sac kesim servis merkezinden gelen rulo halinde ebatlandırılmış sacların aşağıdaki resimde bükülerek boyuna kaynak metodu ile birleştirilmesi ile elde edilirler.
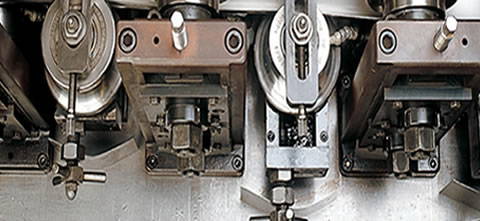
Proseslerde öngörülen akışkanların iletimi de bunlar, sıvılar, su, petrol ve benzer pek çok akışkanın sürtünme katsayısı en düşük silindir yüzeyli bir satıhtan geçmesini sağlamak maksadı ile imalatı yapılmış iletim araçlarıdır. Borulardaki en önemli konu, çalışma basıncı, sıcaklık ve istenen debi(birim zamandaki boru içerisinden geçen akışkan miktarı)ile birlikte belirlenen çap ve et kalınlığı(boru iç çeper kalınlığı)
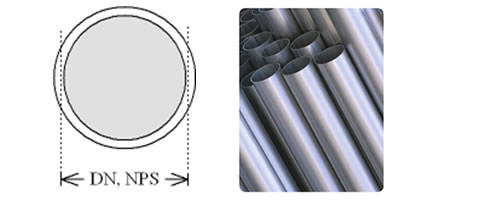
Boruların dış çapları metrik olarak mm cinsinden ifade edildiği gibi, inch karşılığı ISO 1127 standardının öngördüğü gibi DN, ND(Nominal Diameter), NW(Neck weld)gibi ifadeler ile izah edilebilmektedir. Ülkemiz de inch karşılığı anlamının yerine kullanılan “Parmak”-dume-iadesi de çok geniş bir kullanıcı kitlesine sahiptir. Boru et kalınlıklarının ifadesi için dünyada genel olarak iki tanım bulunmaktadır; bunları sıralayacak olursak Amerikan ANSI normu gereği et kalınlıkları Schedule(Türkçe karşılığı: tarife, liste)olarak sayısal verilerle ifade edilmektedirler. (Schedue 40S-SCH 40S)Bu ifade değerinin mutlak bir mm karşılığı da bulunmaktadır. Avrupa normunda ise boruların et kalınlıkları sadece mm cinsinden ifade edilmektedir. Bu ifadeler tanım olarak sadece borularla sınırlı olmayıp, diğer bağlantı elemanları yani fittingsler de kullanılmaktadır.
Tube-tubing nedir?
Tubing aslında bir borudur ancak hassas üretim toleransı ve genel olarak 25 mm’den yüksek olmayan dış çapı ve yine ortalama olarak 2-2, 5 mm’den fazla olmayan et kalınlığı ile boru sınıflamasından ayrılan bir grubu temsil eder. Yüksek basınca bağlı enstrümantasyon uygulamalarında kullanılagelen tubing için hassas borulama teknolojisi olarak bir tanımlama yapmak olasıdır.
Aşağıdaki tabloda Tubinglerin imalat dış çap ve et kalınlıkları görülmektedir. Mavi skala mevcut dünya üzerindeki üretim noktaları göstermektedir.
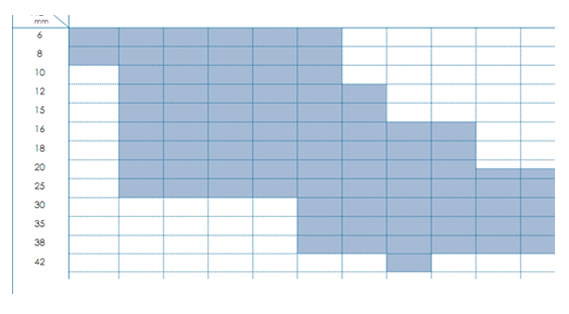
Boru ve tubingler, imalat bakımından dikişli (welded WLD) ve dikişsiz (seamless-SMLS)olarak üretilmektedir. Kaynaklı borular dikişli borulardır. İmalat için gerekli hammadde rulo(coil) sac ve kaynak metodudur. Kaynak metotlarını sıralayacak olursak;
TIG KAYNAKLI (PROSES BORULARI İÇİN EN İYİ KAYNAK METODUDUR)
LASER KAYNAK(HIZLI ÜRETİM, HATA ORANI FAZLADIR)
HF-HIGH FREKANS-KAYNAK(DEKORASYON AMAÇLI UYGULAMALAR İÇİNDİR)
Olarak ifade edilirler.
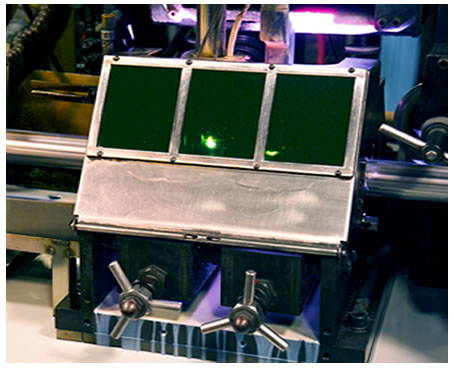
T. I. G Kaynak ünitesi yukarıdaki resimde görülmektedir.
Kullanım öğelerine göre boru çaplarının çap dağılımları aşağıda gösterilmiştir.
DIŞ ÇAP YAPISI ET KALINLIK YAPISI
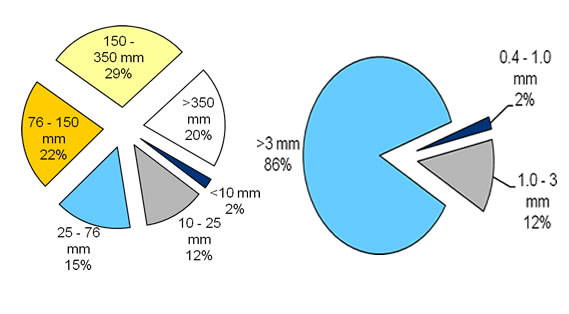
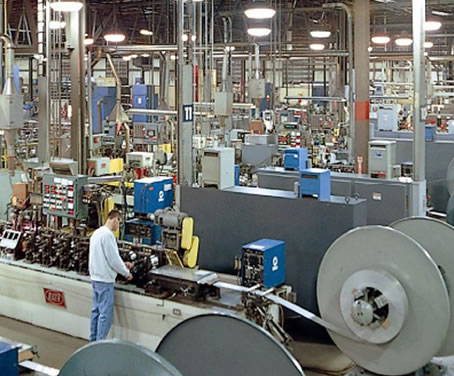
Dikişli Boru üretim tesisi tüm hatları ile görülmektedir.
Borular üretim aşamalarında pek çok proses donanımın kontrolünde hatlarda ilerlemelerini sürdürürler, özellikle borunun iç cidarlarında yapılan işlemler gıda teknolojilerinde önemli esas kaidelerini yerine getirmektedir.
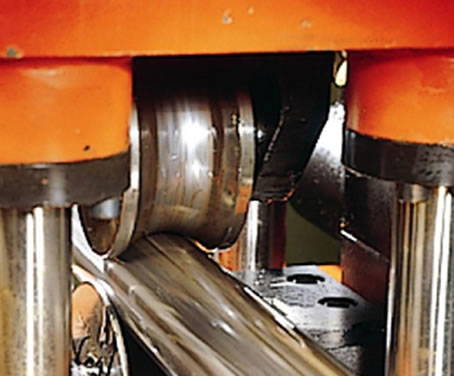
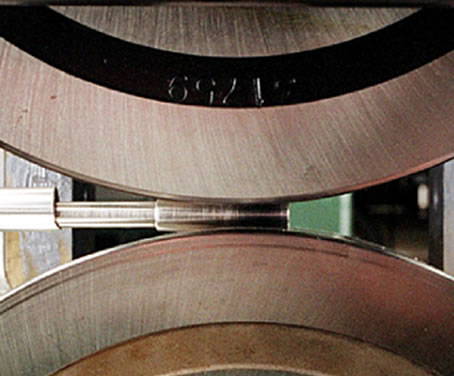
Aşağıdaki resimde bu açık bir biçimde görülmektedir;
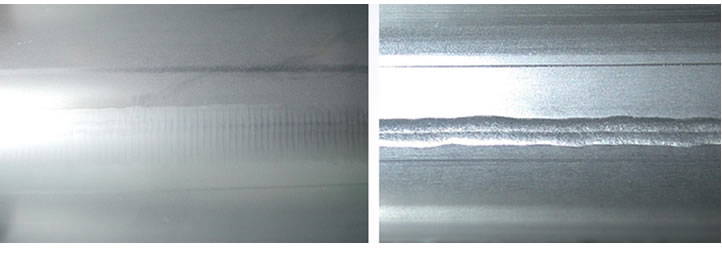
Amaç her zaman borularda yüzeyin ve buna bağlı olan ilgili sektörün tüm gereksinimlerini karşılamaktır, imalat aşaması tamamlanmış bir borunun yüzey resmi mikro inceleme neticesinde aşağıdaki gibi görülmektedir;
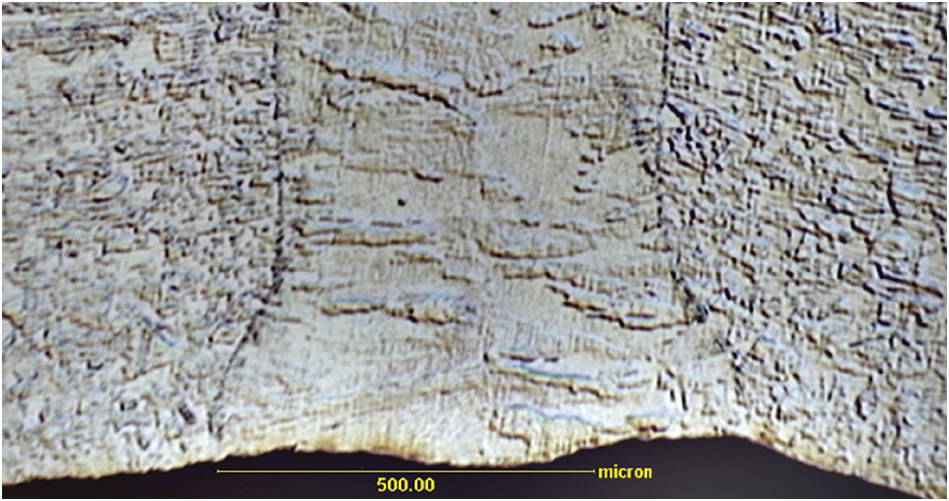
Borular en son aşamada boy kesime, kalibre ve yüzey fırçalama işlemine gitmeden önce kullanım sahasına göre ısıl işleme tabi de tutulabilir;
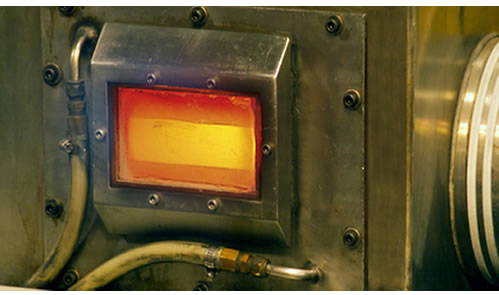
Yukarıda 1060°C’de saniyede 5mm²’lik bir yüzey alanı kontüne olarak hareket etmektedir.
Aşağıda ise kalibre ünitesi ile boru en son çap tolerans sınıfına getirilir;
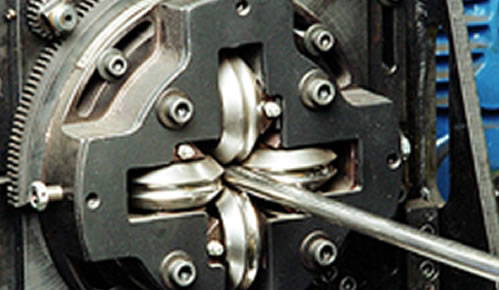
Boru üretimi artık günümüzde çok amaçlı ve otomasyon sürecinde yer alan tüm sistemlerin tek bir skada merkezli olarak kontrolü esasına dayanmaktadır,
Bir Eddy Current sistem çözümü
Üretimin her aşaması en detaylı kısımları da dâhil olmak üzere etüd edilerek çok hassas endüktif kontrollerle -ki bu standartlarda eddy current(girdap akımı)testleri olarak tanımlanmaktadır-üretimin kalite kontrol süreci takip edilmiş olur. Özellikle bugün için kullanım oranı 80 olarak verilen dikişli borulardaki mevcut et kalınlığına bağlı olarak çekme borularla aynı basınç değerlerinin elde edildiği ve z=1 kaynak faktörü ile sertifikalarında ifade edilerek önemli bir ilerleme sağlanmıştır.
Önümüzdeki sayıda boruların ölçülendirilmeleri ve çok önem arz eden toleransları konusunda detaylı bilgilerimizi okurlarımıza vermeye çalışacağız.