Alüminyum akü raflarının işlenmesi
Alüminyum akü rafları üretimi için yeni yüzey frezeleme takımı
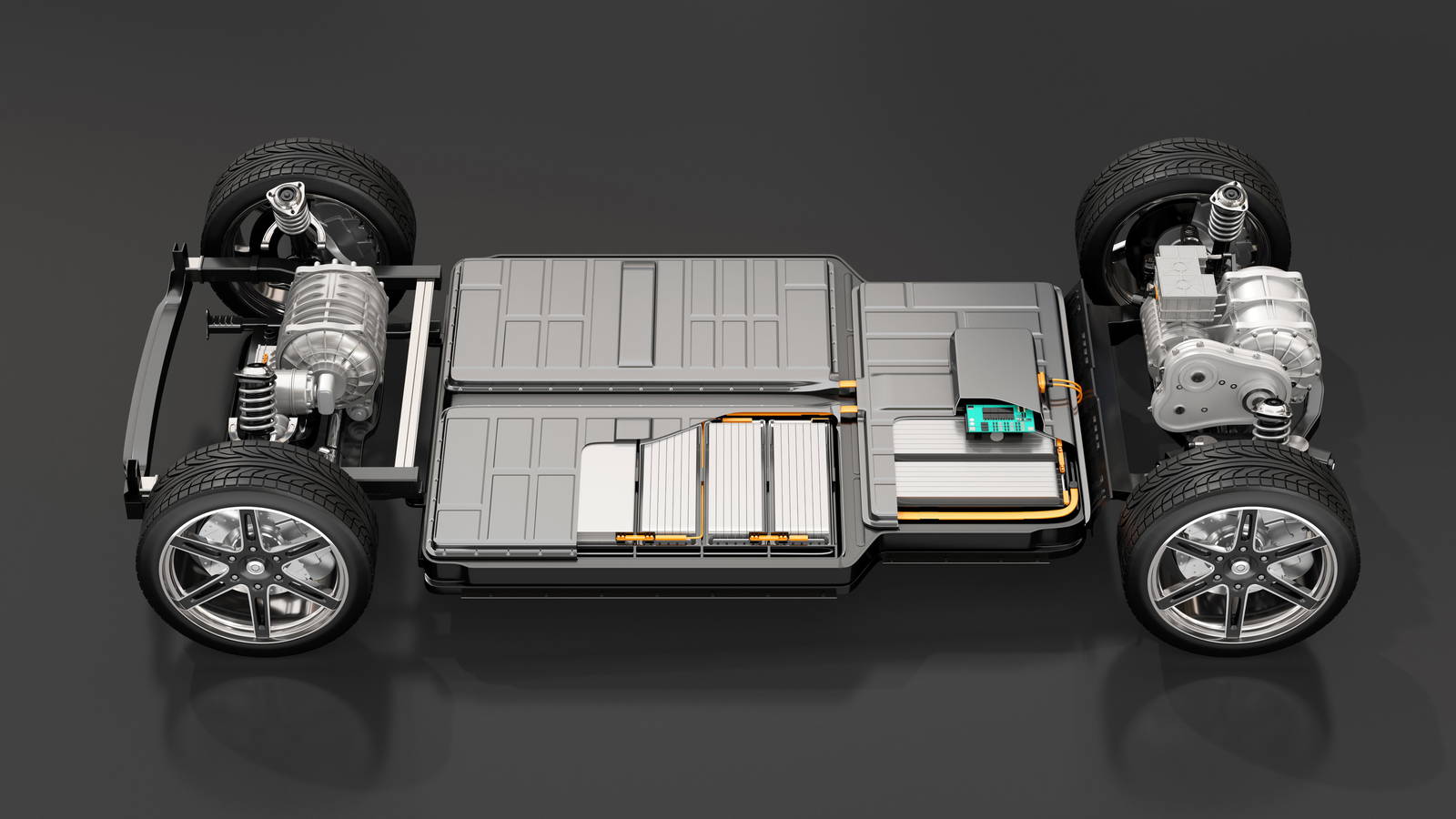
Alüminyum akü rafları üretimi için yeni yüzey frezeleme takımı
Otomotiv sanayi orijinal ekipman üreticileri (OEM'ler), akü hücreleri üretimine giderek daha fazla dahil oluyor ve fiziki olarak araç montaj tesislerine dönüşüyor. McKinsey & Company'nin raporuna göre OEM'leri fark edilir kılan temel farklılıklar akü teknolojisi, dayanıklılık ve performans özellikleri olacaktır. Burada, talaşlı imalat uzmanı Sandvik Coromant'ın Otomotiv Sanayi Alüminyum Bölümü Global Yöneticisi Fernando Oliveira, yeni konsept M5F90 yüzey frezeleme takımının OEM'lere rakiplerinin önüne geçmesine yardım etmede nasıl önem taşıyabileceğini açıklıyor.
Akü sistemleri önümüzdeki yıllarda da gelişimine devam edecek, yeni çalışmalara ve biçimlere ihtiyaç duyulacaktır. Bu durum, OEM'lerin daha karmaşık tasarımları baz alan ağa yakın biçimli akü sistemi parçalarını üretmesini gerektirecektir. Bu tasarımlar işlenirken, takım tezgahı üzerindeki darbeyi azaltarak parça biçiminin korunmasını sağlayacak etkili ve daha hafif kesici takımlar gerekecektir.
Akü üretimine daha fazla dahil olan OEM'lerin rolü de gittikçe gelişiyor ve McKinsey & Company bunu “OEM'lerin raf ve modüllerden hücre üretimine kadar geriye dönük entegrasyonu” şeklinde ifade ediyor Aynı zamanda, şarj başına maksimum araç menzili ile daha uzun mesafeler kat eden daha hafif ve daha etkili elektrikli araçlar (EV'ler) üretme yarışı da devam ediyor.
Ayrıca, üreticilerin bu daha karmaşık parçaları en yüksek kalitede ve yüksek verimlilikle üretmesi gerekir. Üreticiler, parça başına maliyeti düşük tutarken bunu nasıl başarabilir? Bu sorunun yanıtı, iyi erişilebilirliğe sahip, hızlı takım değişikliklerine izin verecek kadar hafif ve daha etkili kesici takımlara dayanıyor.
CO2 emisyonlarının azaltılması
Üreticiler "ağırlık azaltmaya" yöneliyor ve bu da daha iyi yakıt verimliliği ve yol tutuşu elde etmenin bir yolu olarak daha hafif otomobil ve kamyon üretimlerini gerektiriyor.
McKinsey & Company'nin Lightweight, heavy impact adlı diğer bir araştırmasında, "Ağırlık azaltma çalışmalarının CO2 emisyonlarının belirli ölçüde azaltılmasına yardımcı olabileceği (tasarruf edilen kilogram başına yaklaşık 0,08 g CO2 azaltma)" hesaplanmıştır "Bir OEM'in araç ağırlığını 100 kg azaltmayı başarması halinde, 100 km'de yaklaşık 8,5 g CO2 tasarrufu sağlanır" sonucuna varılmıştır
Dünyadaki en hafif metallerden biri olan alüminyum, yaygın olarak kabul görmüş bir ağırlık azaltma çözümüdür. Alüminyum, demirden neredeyse üç kat daha hafiftir ve demirden daha düşük mukavemete sahip olmasına rağmen yine de çok güçlü ve korozyona dayanıklıdır. Tasarım mühendisliği açısından bakıldığında, geleneksel döküm demir parçaların yerine alüminyum alaşımların kullanılması sayesinde motor bloğu toplam ağırlığının %40-55'e kadar azaltılabileceği keşfedilmiştir.
Alüminyumun diğer bir avantajı da geri dönüştürülebilir özellikte olması ve mekanik özelliklerinde herhangi bir hasar oluşturmadan veya değişiklik yapılmadan eritilip tekrar kullanılabilmesidir. Aslında, bugün hâlâ şimdiye kadar üretilen tüm alüminyumun yaklaşık %75'i kullanılmaktadır ve bu, OEM'lerin sürdürülebilirlik stratejilerinde malzemenin kullanışlı olduğunun kanıtıdır.
Küçük yüzeyler
Standart bir Avrupa yapımı binek otomobilinin güç aktarma sistemi yaklaşık 80 kilogram alüminyum içerir, bu nedenle bu parçalar (motor, şanzıman, süspansiyon parçaları, muhafazalar gibi) ağırlık azaltma çalışmaları için belirgin bir ilgi odağıdır. Ayrıca, alüminyum akülerde de kullanılabilir: AB-Çin Enerji İşbirliği Platformu (ECECP), lityum iyon (Li-ion) akülere "ucuz, hafif ve güçlü" bir alternatif olarak alüminyum-hava (AI-hava) aküleri tavsiye etmektedir.
Burada, alüminyum akü raflarına odaklanalım. Bu parçalar, genellikle daha fazla diş, delik ve diğer özellikleri içeren daha küçük yüzeylere sahiptir. Diğer bir önemli husus, kamyonlara özellikle de yerleşik alanların dışında sürülen ve uzunluğu iki metreye kadar ulaşan daha büyük modellere yönelik elektrikli akü raflarıdır.
Akü rafları için çeşitli takım tezgahları ve frezeleme, çerçeveleme ve diğer uygulamalar gerekir. Ancak daha büyük akü rafları için büyük takımlar gerekmez ve bunun yerine daha fazla özellik, diş ve delik içeren daha küçük yüzeylerden oluşan takımlar kullanılır. Bu nedenle, parçaları gerekli kalite ve toleranslarda üretebilen kenar ve yüzey frezeleme takımlarına veya raybalara ihtiyaç duyulur.
Titreşimlerin ortadan kaldırılması
Sandvik Coromant, akü raflarının işlemesinde parçaları çapak, çizik veya çentiklenme olmadan işlemeye yönelik tasarlanmış M5F90 yüzey freze kesicisi de dahil olmak üzere M5 özel otomotiv sanayi alüminyum frezeleme takımları serisinin kullanılmasını tavsiye eder. Kesici, ince duvarlı alüminyum parçaları işlemeye yönelik tasarlanmıştır ve bunu başarmak için 25–80 mm veya 0,98-3,15 inç çapa sahip küçük kesici gövdesi ile donatılmıştır. M5F90 ayrıca sert lehimlenmiş Çok Kristalli Elmas (PCD) uçlar içerir, bu nedenle ayar gerektirmez ve çok daha az salgı sağlar. Bu özellik, yüksek ilerleme hızları sağlarken kesme titreşimlerini de ortadan kaldırır.
Bir örnekte, bir alüminyum akü tablasını işlemek için M5F90 kullanıldı. Yeni konsept yüzey frezeleme takımı için ideal bir uygulamaydı, çünkü takımın yeni döküm alüminyum parçaların ilk işleme kademesinde yüzeyleri çapaksız olarak tek bir işlemle temizlemek için kullanılmasını gerektiriyordu.
Ölçüleri, yaklaşık 980 x 600 x 130 milimetre (mm) idi. Genel olarak, parça işlenirken yekpare karbür matkaplar, yekpare karbür parmak frezeler, yüksek hız çeliği (HSS) kılavuzlar, sert lehimlenmiş PCD raybalar, sert lehimlenmiş PCD frezeleme takımları ve son olarak M5F90 kesici dahil olmak üzere 48 takım kullanıldı. Alüminyum parça, HSK 63 yüksek hızlı takım tutucu ile donatılmış 5 eksenli bir işleme merkezinde işlendi.
M5F90'ın sert lehimlenmiş PCD kesici uçları, radyal ve teğetsel olarak her iki yönde kademeli kesme kenarlarına sahiptir. Bu özellik, güç tüketimini düşürerek daha yüksek kesme parametreleri ile çalışmaya izin verir, bu da çapakları ortadan kaldırır ve işleme sırasında titreşimleri azaltır. İkinci bir avantajı da iyileştirilmiş takım ömrü ile güvenilir performans sağlamaya yardımcı olması ve işlenen parça sayısını artırmasıdır.
Sonunda, akü tablası işleme uygulaması M5F90'ın önemli bir avantajını ortaya çıkardı. Spesifik olarak, tek bir işlemde kaba talaş işleme ve ince talaş işlemeyi mümkün kılarak zaman tasarrufu sağlar. Bu, alüminyum akü tablasının işlenmesi sırasında ortaya çıkmıştır; parça 20,3 dakikada işlenmiştir. Bu gelişmiş takım performansı sayesinde, OEM'ler kendilerini rakiplerinden ayırırken akü sistemlerinin üretimine daha fazla müdahil olabilir.
Sandvik Coromant'ın alüminyum işleme için takımlama çözümleri hakkında daha fazla bilgi edinmek için web sitesini ziyaret edin.
. . .
İçerik sadece atıfta bulunularak yayınlanabilir: Sivas İş Dünyası. Editöryal görüş, yazarın görüşüne aykırı olabilir.