Gedikin Dev Projesi Hızla Tamamlanıyor
GEDİK Holding, döküm ve kaynak alanındaki üretim kapasitesini ve ürün çeşitliliğini artırmak üzere Sakarya Hendek
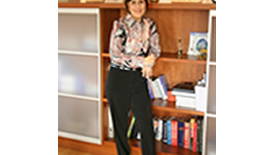
GEDİK Holding, döküm ve kaynak alanındaki üretim kapasitesini ve ürün çeşitliliğini artırmak üzere Sakarya Hendek
GEDİK Holding, döküm ve kaynak alanındaki üretim kapasitesini ve ürün çeşitliliğini artırmak üzere Sakarya Hendek 2. Organize Sanayi Bölgesi’nde satın aldığı 261.700 metrekare arsa üzerinde kurduğu yeni tesisi hızla tamamlıyor.
Proje kapsamında inşa edilen Gedik Döküm ve Vana’nın yeni dökümhanesi bu yaz devreye alınacak.
Gedik Döküm ve Vana bu yeni tesisle birlikte modern üretim süreçleri, tam donanımlı laboratuarları, dünya standartlarındaki ürün kalitesi, bilgi birikimi ve insan kaynağını da arkasına alarak yurtiçi ve yurtdışında pazar büyütmeyi hedefliyor.
Kapasite ağırlıkla ihracata yönelik olacak
25 bin metrekaresi kapalı olmak üzere, 50 bin metrekare alan üzerine inşa edilen yeni dökümhane, şirketin 5000 ton/yıl olan yıllık kum döküm kapasitesini 30.000 ton/yıl’a çıkaracak. Döküm kapasitesinin bir kısmı Türkiye’nin en köklü vana markası TERMO’nun üretiminde kullanılacak. En gelişmiş kum döküm teknolojilerinin kullanılacağı Hendek tesisiyle artacak olan üretim kapasitesi, ağırlıkla ihracata yönelik olacak.
Gedik Holding Yönetim Kurulu Başkanı Hülya Gedik, yeni tesis ile ilgili çalışmalarının yanı sıra tüm vana ve döküm ürünlerinde Ar-Ge bazlı çalışmalara da ağırlık verdiklerini, yeni yatırım ile artacak kapasite ile yüksek teknolojili ürünlere yoğunlaşacaklarını söyledi. Dış pazarlarda kaliteli vana ve döküm (kum ve hassas) ürünleri ile enerji, petro-kimya, savunma ve otomotiv sektörlerine hizmet vermeye odaklandıklarını söyleyen Hülya Gedik, “stratejik ortaklık” prensibi ile hareket ettiklerini, 2011’in ikinci yarısından itibaren yeni tesislerinde ağırlıkla dış pazara yönelik özgün yeni ürünleri piyasaya sunacaklarını ifade etti.
1982’de hassas dökümü Türkiye’ye getiren Gedik Döküm ve Vana, SIRMETAL markasıyla yurt içi ve yurt dışına başta savunma sanayi olmak üzere tekstil, otomotiv, tıp, makine, vana, pompa ve elektronik sanayindeki birçok firmanın döküm ihtiyaçlarına yönelik çözümler sunuyor. Gedik Döküm, hassas dökümün bir ileri seviyesi olan yüksek sıcaklıklara dayanıklı özel malzemeleri ve sağlık sektöründe kullanılan malzemeleri dökme teknolojilerini de Hendek tesisine geçtiğinde hayata geçirecek.
Gedik Döküm ve Vana yeni projelerle ilklere imza atmaya devam ediyor
Türkiye’nin en bilinen vana markalarından TERMO’nun üretimini yaparak ulusal ve uluslararası pazarlara hizmet veren Gedik Döküm ve Vana bu sektörde çok geniş bir ürün çeşitliliğine sahip bulunuyor. Firma son olarak MİLGEM (Milli Gemi) projesi için değişik boyutlarda ürettiği VG normlarında bronz vanalarla Türkiye’de yine bir ilke imza attı ve Türk Loydu’ndan “Tip Onay Belgesi” alan tek firma oldu.
Halen 40 bar basınca dayanıklı dövme çelik gövdeli yüksek basınçlı vanalar üreten Gedik Döküm ve Vana, Alman teknolojik çözüm ortağı ile 100 bar ve üzeri basınçlar için de vanalar üretmek üzere Ar-Ge çalışmalarını tamamladı. Enerji santrallerinde kullanılan ve şu anda yurtdışından yüksek fiyatlarla ithal edilen ürünlerin yerine geçecek bu vanalarla, Türkiye’nin bu ürünlerle dışa bağımlılığının azaltılması hedefleniyor.
2011’de tüm bayilerine ve müşterilerine TERMO-MANKENBERG markalı yeni tip basınç düşürücü vanalar sunmaya başlayan firma bir sonraki aşamada Amerikan Petrol Enstitüsü (API) ve ASME normunda doğalgaz ve petrol vanalarını üretmeyi hedefliyor.
Yeni dökümhane ile ilgili bilgiler
Gedik’in Hendek’teki yeni tesisinde gri dökme demir, küresel grafitli dökme demir, karbon ve alaşımlı çelikler, bakır esaslı (bronz) dökümler yapılacak. Üretilen parçalar vana, pompa, doğalgaz sanayi, makine sanayi ve otomobil sanayisinde kullanılacak.
Projede üretim teknolojisi için seçilen cihazlar ve sistem dizaynı tüm üretim adımlarını birbirine entegre edecek ve her adımda kalite kontrolü sağlanacak şekilde tasarlandı.
Tesiste üretim iki derecesiz ve bir dereceli olmak üzere üç hat üzerinden gerçekleştirilecek. İlk etapta derecesiz kalıplama hatları, ileriki bir tarihte ise dereceli kalıplama hattı devreye alınacak.
İlk olarak devreye girecek olan 150 kalıp/saat kapasiteli Sinto FBO X kalıplama makinesi satın alındı. Bu hattın çalışmasına takiben, 100 kalıp/saat kapasiteli Sinto FBO III derecesiz kalıplama hattı kurulacak. Bu makinalarda 0.2- 50 kg arasında ağırlığı olan döküm parçaları üretilecek.
Toplam 250 kalıp/saatlik bu iki hattın sıvı maden ihtiyacını, Inductotherm firmasından alınan 2 ve 3 ton/saat kapasiteli dual-track endüksiyon ocakları sağlayacak. Bu ocaklar 2011’in ilk ayında montajları yapılarak devreye alınacak.
Sinto hatlarının 50 ton/saat olan kum ihtiyacını Eirich R18 ve Webac Speedmullor 75B kum mikserleri karşılayacak. Kum soğutucusu olarak Simpson firmasından satın alınan MC-50 MultiCooler kum soğutucu cihazı kullanılacak. Kumun döküme uygunluğunun tayini içinde Hartley 18Mk2/2552 test ünitesi alındı. Her iki cihaz kum hazırlama binasının tüm kontrollerini sağlayacak.
Projelendirmesi biten ve temel çalışmaları yapılan kum hazırlama binasında bu cihazların montajı kış şartları nedeni ile Mart 2011’de başlayacak.
Sinto hatlarının devreye alınmasından sonra, projesi yapılmış 120 kalıp/saat kapasiteli dereceli kalıplama hattı satın alma işlemi tamamlanacak. Bu hattın sıvı maden ihtiyacı 10 ton/saat, kum ihtiyacı ise 100 ton/saat olacak. Dereceli kalıplama hattının işletmeye alınması üretim hacmini ciddi oranda artıracak ve bu kapasite özellikle ihracat hedefli çalışacak.
Sinto FBO III ve FBO X hatlarından çıkan dökümler, General Kinematics firmasından alınan modern kalıp bozucu, soğutucu ve sarsak sistemine alınacak. Bu sistemde dökülen parçaların yolluklarını kırma, kum ayrıştırma, temizleme ve soğutma işlemleri yapılacak.
Yeni sistemde yer alan 1800mm iç çapta, 6800 mm uzunluğunda ve 55 ton/saat kapasiteye sahip ‘Vibro-Drum’, kalıp kumu ve döküm parçalarını birbirinden ayırmanın yanı sıra parça ve kum soğutucu olarak da çalışıyor. Üretim aşamasında olan ve General Kinematics’ten alınan bu cihazların Hendek fabrikasına montajı Şubat 2011’ de gerçekleştirilecek.
Bu işlemin devamı olan temizleme ve taşlama sistemlerinin projelendirmesine ise devam ediliyor. Ayrıca proje aşamasında olan çelikhanenin yeni kalıplama sistemi için çeşitli firmalarla temaslar sürüyor.
1200 metrekarelik alan işleme atölyesi için ayrılacak, burada modern torna ve CNC makinalarında işlenen parçalar son ölçülerinde müşteriye sevk edilecek.
. . .
İçerik sadece atıfta bulunularak yayınlanabilir: Sivas İş Dünyası. Editöryal görüş, yazarın görüşüne aykırı olabilir.