Nikel Kaplanmış Farklı Malzemelerin Korozyon Davranuşlarının Karşılaştırılması
Bu çalışmada, nikel kaplanmış farklı malzemelerin korozyon davranışları karşılaştırıldı
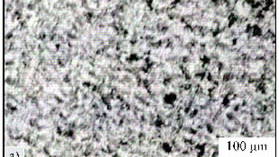
Bu çalışmada, nikel kaplanmış farklı malzemelerin korozyon davranışları karşılaştırıldı
Bu çalışmada, nikel kaplanmış farklı malzemelerin korozyon davranışları karşılaştırıldı. Bu amaçla, bir pirinç alaşımı (CuZn30) ve bir çelik (AISI 1020) malzeme üzerine elektrolitik yöntemle nikel kaplandı. Kaplanmamış ve nikel kaplanmış taban malzemelerin korozyon davranışları polarizasyon ve impedans teknikleri ile belirlendi. Kaplamaların yapısal özellikleri X-ışını difraksiyonu (XRD) kullanılarak karakterize edildi. Kaplamaların yüzey morfolojisi taramalı elektron mikroskobu (SEM) ile incelendi. Numunelerin yüzey sertlikleri Vickers sertlik testi ile tayin edildi. Yapılan nikel kaplamaların hem pirinç ve hem de çelik taban malzemelerin korozyon direncini artırdığı ve farklı taban malzeme kullanımının korozyon direncindeki artış miktarını etkilediği belirlendi. Ayrıca, her iki taban malzemenin sertliğinin de yapılan nikel kaplamalarla önemli miktarda arttığı gözlendi.
Anahtar Kelimeler: Elektrolitik kaplama, nikel, korozyon, taban malzeme
1. GİRİŞ
Kaplamalarla yüzey modifikasyonu; aşınma, korozyon ve oksitlenme gibi yüzey özelliklerini geliştirmek için uygulanan önemli bir adım olmuştur [1]. Kaplamalar, metal ve çevresi arasında bir engel oluşturarak ve/veya içerilerinde bulunan korozyonu engelleyici kimyasalların mevcudiyeti sayesinde bir taban malzemeyi koruyabilirler [2]. Yüzey modifikasyonu yapmak amacıyla taban malzeme üzerine istenen malzemelerin kaplanması için çeşitli ticari teknikler geliştirilmiştir [1]. Korozyon direncini artırmak için yaygın olarak kullanılan tekniklerden bazıları; boyama, kromatlama, anotlama, buhar fazından kaplama ve elektrolitik kaplamadır [3]. Elektrolitik kaplama, bir taban malzeme üzerine metalik bir kaplamanın en ucuz ve basit olarak yapıldığı tekniklerden biridir [2].
Elektrolitik nikel kaplama, yüzey özelliklerini iyileştirmek, korozyon direncini ve aşınma özelliklerini geliştirmek için birçok endüstri alanında oldukça yaygın olarak kullanılmaktadır [4–6]. Nikel kaplamalar genellikle kükürtsüz kaplamalardır ve mat görünümlüdür. Bu kaplamalar; korozyon ve aşınma direncini geliştirmek, manyetik özellikleri modifiye etmek, parlatma veya organik kaplama için yüzeyleri hazırlamak, elektronik uygulamalarda difüzyon bariyerleri olarak fonksiyon yapmak gibi amaçlar için kullanılabilirler. Nikel kaplamaların; kimyasal, nükleer, telekomünikasyon, elektronik ve bilgisayar endüstrilerinde mühendislik uygulamaları mevcuttur [7–8].
Nikel kaplamalar korozyon ve aşınmaya karşı dirençli bir yüzey oluşturduklarından dolayı, çeliklerin ve alaşımların korozyon ve aşınmadan korunması için birçok yıldır başarı ile kullanılmaktadır. Çeşitli endüstri uygulamaları ve ekonomik önemi nedeniyle, pirinç alaşımlarının korozyona karşı korunması oldukça ilgi çekici olmuştur. Bununla birlikte, pirinç alaşımları klorür içeren sulu çözeltiler ve atmosferde kolaylıkla korozyona uğramakta ve bu durum da pirincin kullanımını sınırlandırmaktadır [9]. Mühendislik uygulamalarında yaygın olarak kullanılan pirinç alaşımlarının korozyon direnci, üzerlerine elektrolitik yöntemle yapılacak nikel kaplamalarla geliştirilebilir. Ayrıca, elektrolitik yöntemle yapılan kaplamalarda, taban malzemenin bileşimi ve içyapısı korozyon direncini önemli derecede etkiyebilir [3]. Bu yüzden bu çalışmada, farklı taban malzeme kullanımının elektrolitik olarak yapılan nikel kaplamaların korozyon direncini ne şekilde etkilediği araştırılmıştır.
2. DENEYSEL ÇALIŞMA
Bu çalışmada kullanılan taban malzemeler, mühendislik uygulamalarında sıklıkla kullanılan CuZn30 pirinci ve AISI 1020 çeliğidir. Taban malzemelerin kimyasal bileşimleri Tablo 1 ve 2’de görülmektedir. CuZn30 pirinç taban malzemelerine, 730°C’de su verildi. AISI 1020 çelik taban malzemeler ise sırasıyla 930 ve 880°C’de normalize edildi. Taban malzemeler silindirik şekilli olup, 25 mm çapta ve 10 mm yüksekliktedirler. Kaplama işleminden önce, her iki taban malzeme de 600 ve 1200 nolu SiC zımpara kağıtlarında mekanik olarak zımparalandı, ardından 0.05µm tane boyutundaki alümina tozuyla Ra yüzey pürüzlülüğü yaklaşık 0.20 olacak şekilde parlatıldı ve önce etanol sonra da aseton ile çalkalandı.
Tablo 1. CuZn30 pirinç taban malzemesinin kimyasal bileşimi
(ağırlık)
Sn Pb Zn Ni Si Fe Cu
0.022 0.063 30.27 0.019 0.16 0.06 68.5
Tablo 2. AISI 1020 çelik taban malzemesinin kimyasal bileşimi
(ağırlık)
C Mn P S Fe
0.21 0.45 0.03 0.04 99.2
CuZn30 pirinç ve AISI 1020 çelik taban malzemeler, fonksiyonel kaplamalar yapmak için kullanılan nikel sülfamat çözeltilerinde elektrolitik yöntemle nikel kaplandı. Nikel kaplamadan önce kaplama tabakalarının adezyonunu iyileştirmek için bütün taban malzemelere alkalik temizleme ve aside daldırma işlemleri uygulandı. Çalışmada kullanılan kaplama koşulları ve banyo bileşimi Tablo 3’te verildi.
Kaplanmamış ve elektrolitik olarak kaplanmış numunelerin elektrokimyasal davranışları potansiyodinamik polarizasyon ve elektrokimyasal impedans spektroskopi (EIS) yöntemleriyle incelendi. Bütün numunelere ait testler, bir cam hücre içinde, oda sıcaklığındaki 3.5 NaCl çözeltisi içerisinde yapıldı. EIS ve polarizasyon eğrileri, bir AgCl/Ag referans elektrodu ve bir platin karşıt elektrot kullanılarak elde edildi. Çözeltiye maruz bırakılan alan 1 cm2 idi. Korozyon deneyleri GAMRY PCI4/750 marka bir potansiyostat/galvanostat kullanılarak gerçekleştirildi. Numuneler test çözeltisine daldırıldı ve açık devre potansiyeli (OCP) kararlı oluncaya kadar beklendi. Kararlı duruma ulaşılınca, OCP’nin yaklaşık -600mV aşağısındaki bir potansiyelden itibaren, 10 mA/cm2 anodik akım yoğunluğuna ulaşılıncaya kadar, 1 mV/s tarama hızıyla potansiyel taraması yapıldı. Korozyon davranışlarını incelemek için, OCP civarında EIS testleri de yapıldı. Korozyon deney sonuçları, polarizasyon, Nyquist ve Bode diyagramları ile verildi. Polarizasyon ve EIS testlerinden sonra numuneler görüntü analizi için ultrasonik olarak temizlendi.
Tablo 3. Elektrolit yöntemle yapılan nikel kaplamaların kaplama koşulları ve banyo bileşimi
Kaplama koşulları ve banyo bileşimi
Nikel sülfat
(NiSO4.6H2O) (g/l) 240
Nikel klorür
(NiCl2.6H2O) (g/l) 45
Borik asit
(H3BO3) (g/l) 50
pH 4.3
Katodik akım yoğunluğu
(A/m2) 0.05
Sıcaklık (°C) 55
Pirinç ve çelik taban malzemelerin kaplama yapılmadan önceki ve sonraki sertlik değerleri, PC Conrolled Buehler-Omnimet test cihazıyla Vickers sertliği cinsinden ölçüldü. Sertlik ölçümleri 0.5 g yük altında yapıldı. Kaplamaların yapısal özellikleri XRD kullanılarak incelendi. Kaplanmamış ve kaplanmış taban malzemelerin mikroyapı ve yüzey morfolojileri Nikkon Epithot marka bir optik mikroskop ve Jeol 6400 marka bir taramalı elektron mikroskobu kullanılarak incelendi.
3. ARAŞTIRMA BULGULARI VE TARTIŞMA
AISI 1020 çeliği ve CuZn30 pirinç taban malzemelerinin içyapıları, parlatma ve kimyasal dağlama işlemleri uygulandıktan sonra optik mikroskop ile incelendi. Gözlemlenen içyapılar Şekil 1’de verildi. Şekil 1a, ferrit, perlit ve metalik karbür içeren AISI 1020 çelik taban malzemenin içyapısını göstermektedir. Şekil 2 ise, çinkonun bakır içerisinde 39’a kadar gibi yüksek katı çözünürlüğüne sahip olması nedeniyle α-katı çözeltilerini içeren CuZn30 pirinç taban malzemesinin içyapısını göstermektedir.
Şekil 1. Taban malzemelerin içyapıları; a)AISI 1020 çeliği, b) CuZn30 pirinci
Kaplanmış malzemelerin XRD analizinde taban malzemelerden gelen difraksiyon piklerini ayırmak için, kaplanmamış malzemelerin de XRD analizleri yapılarak, kaplanmamış ve kaplanmış alaşımların XRD diyagramları birlikte verildi. Şekil 2 çeliğin ve Şekil 3 pirincin, kaplanmamış ve elektrolitik olarak nikel kaplanmış durumdaki XRD diyagramlarını göstermektedir. Bu şekillerde, hem AISI 1020 çeliğinde ve hem de CuZn30 pirincinde kaplama sonrasında (111), (200) ve (220) düzlemlerinde nikel kaplamaya ait piklerin oluştuğu görülmektedir. (111) pikinin rölatif yoğunluğunun diğer piklerden daha büyük olduğu da gözlenmektedir.
Şekil 2. Kaplanmamış ve nikel kaplanmış AISI 1020 çeliğinin XRD diyagramları
3.5 NaCl korozif çözeltisi ortamına maruz bırakılan kaplanmamış ve elektrolitik olarak nikel kaplanmış pirinç ve çelik malzemelerin potansiyodinamik polarizasyon ölçümlerinden elde
Şekil 3. Kaplanmamış ve nikel kaplanmış CuZn30 pirincinin XRD diyagramları
edilen polarizasyon diyagramları, sırasıyla Şekil 4 ve 5’te görülmektedir. Kaplanmamış ve nikel kaplanmış malzemelerin potansiyodinamik polarizasyon diyagramları, karşılaştırma yapılabilmesi amacıyla aynı eksen takımı üzerinde verilmiştir. Şekillerde aynı polarizasyon potansiyellerindeki akım yoğunlukları incelendiğinde, taban malzemeler üzerinde elektrolitik olarak oluşturulan nikel kaplamaların çözünme akımını önemli derecede azalttığı gözlenmektedir. Şekil 4, kaplanmamış ve nikel kaplanmış CuZn30 pirinç malzemesinin polarizasyon diyagramlarını göstermektedir. Kaplanmamış ve kaplanmış pirinç malzemelerin korozyon potansiyelleri (Ekor) karşılaştırıldığında, kaplanmamış durumdaki pirinç taban malzemesinin korozyon potansiyeli yaklaşık -552 mV iken, nikel kaplanmış pirinç malzemesinin korozyon potansiyeli yaklaşık -317 mV’a çıkmıştır. Dolayısıyla yapılan nikel kaplamalar CuZn30 pirinç malzemesinin korozyon potansiyelini daha pozitif potansiyellere doğru kaydırmıştır. Şekil 5 ise, kaplanmamış ve nikel kaplanmış AISI 1020 çelik malzemenin polarizasyon diyagramlarını göstermektedir. Şekilde görüldüğü gibi, kaplanmamış durumda yaklaşık -799 mV olan çelik taban malzemeye ait korozyon potansiyeli değeri de, nikel kaplama sonrasında daha pozitif potansiyel değerine (yaklaşık -358 mV) kaymıştır. Yapılan kaplamalarla korozyon potansiyellerinde daha pozitif değerlere doğru elde edilen bu artış, elektrolitik olarak uygulanan nikel kaplamanın her iki taban malzemenin de korozyon dayanımını artırdığını göstermektedir. Korozyon akım yoğunluğu (ikor) da korozyon çalışmalarında önemli bir parametre olarak yaygın şekilde kullanılmaktadır. Korozyon hızı, polarizasyon sırasında ölçülen korozyon akım yoğunluğu ile doğru orantılıdır. Kaplama öncesi CuZn30 pirinç ve AISI 1020 çelik taban malzemelerden elde edilen korozyon akım yoğunluğu değerleri sırasıyla yaklaşık 0.4 ve 4 μA/cm2 iken, yapılan nikel kaplamalar ile korozyon akım yoğunlukları daha küçük değerlere düştü. Kaplama sonrasında CuZn30 pirincinden elde edilen korozyon akım yoğunluğu değeri yaklaşık 0.01 μA/cm2 ve AISI 1020 çeliğinden elde edilen korozyon akım yoğunluğu değeri ise yaklaşık 0.6 μA/cm2 olarak belirlenmiştir. CuZn30 pirinç malzemesine ait anodik polarizasyon diyagramı incelendiğinde, nikel kaplanmış pirinç malzemede yaklaşık -210 ve +25 mV potansiyeller arasında pasife benzer davranış sergilendiği görülmektedir. Polarizasyon diyagramlarında elde edilen bütün bu bulgular, kullanılan taban malzemelerin korozyon dayanımlarının, üzerlerine uygulanan nikel kaplamalar ile artırıldığını ve dolayısıyla korozyon hızlarının azaltıldığını göstermektedir. Şekil 6’da korozyona uğramış nikel kaplı pirincin polarizasyon testinden sonraki SEM görüntüsü görülmektedir.
Şekil 5. Kaplanmamış ve nikel kaplanmış AISI 1020 çelik malzemesinin polarizasyon diyagramları
Şekil 6. Korozyona uğramış nikel kaplı pirincin polarizasyon testinden sonraki SEM görüntüsü
Bir malzemenin korozif bir ortama daldırılması sırasındaki korozyon potansiyeli ve polarizasyon direnci, devam etmekte olan korozyon reaksiyonu ile ilgili bilgi sağlayabilmektedir. Bununla birlikte, EIS çalışmalarıyla kaplama/çözelti ve taban malzeme/çözelti ara yüzeyi civarında buna ilave bilgi de elde edilebilir. Şekil 7 ve 8, kaplanmamış ve elektrolitik olarak nikel kaplanmış CuZn30 pirinci ve AISI 1020 çeliğinin impedans cevaplarını Nyquist diyagramları ile göstermektedir. Nyquist diyagramındaki reel eksenin yüksek frekanslardaki kesişimi elektrolit direnci, düşük frekanslardaki kesişimi ise yük transfer direnci olarak yorumlanır. Nyquist diyagramları her iki kaplanmamış ve nikel kaplanmış malzemede de tek bir yarım daire şekli gösterdi. Şekil 9 ve 10 incelendiğinde, elektrolitik olarak yapılan nikel kaplamaların hem pirinç ve hem de çelik malzemelerin korozyon dirençlerini artırdığı, bununla birlikte, farklı taban malzemeler kullanımının korozyon direncinde elde dilen artış miktarını önemli derecede etkilediği tespit edildi. EIS testleri ile, yapılan nikel kaplamaların, CuZn30 pirinç taban malzemesinin korozyon direncini AISI 1020 çelik taban malzemesininkine göre önemli derecede daha fazla artırdığı gözlemlendi. Kaplanmamış ve elektrolitik olarak nikel kaplanmış taban malzemelerin korozyon davranışları Bode diyagramları ile de incelendi ve bu diyagramlar Şekil 9 ve 10’da verildi. Bu şekillerde görüldüğü gibi, Nyquist diyagramlarındaki gibi, yapılan nikel kaplamaların, CuZn30 pirinç taban malzemesinin korozyon direncini AISI 1020 çelik taban malzemesininkine göre önemli derecede daha fazla artırdığı tespit edildi. Bu bulgular, elektrolitik nikel kaplamaların CuZn30 pirincine AISI 1020 çeliğine göre korozyona karşı daha iyi koruma sağladığını göstermektedir.
Şekil 7. Kaplanmamış ve elektrolitik olarak nikel kaplanmış CuZn30 pirincinden elde edilen Nyquist diyagramları
Kaplamadan önce ve kaplamadan sonra AISI 1020 çeliği ve CuZn30 pirincinden ölçülen sertlik değerleri Şekil 11’de görülmektedir. Şekil incelendiğinde, kaplamadan önce sertliği yaklaşık 183 VSD olan AISI 1020 çeliğinin sertliğinin yapılan kaplama sonrasında 320 VSD’e ulaştığı görüldü. Benzer şekilde kaplamadan önceki sertliği yaklaşık 117 VSD olan CuZn30 pirincinin sertliği yapılan kaplama sonrasında 295 VSD olarak elde edildi. Dolayısıyla, elektrolitik olarak yapılan nikel kaplamalar ile hem çelik ve hem pirinç malzemenin sertliğinde önemli miktarda artış elde edildi. Kaplamalarla sertlikte elde edilen bu artış, taban malzemeye göre daha sert olan kaplamaların plastik deformasyona karşı daha fazla direnç göstermesine dayandırılabilir.
Şekil 9. Kaplanmamış ve elektrolitik olarak nikel kaplanmış CuZn30 pirincinden elde edilen Bode diyagramları
Şekil 10. Kaplanmamış ve elektrolitik olarak nikel kaplanmış AISI 1020 çeliğinden elde edilen Bode diyagramları
Şekil 11. Kaplamadan önce ve kaplamadan sonra AISI 1020 çeliği ve CuZn30 pirincinden ölçülen sertlik değerleri
4. SONUÇLAR
CuZn30 pirinç ve AISI 1020 çelik taban malzemeleri üzerine elektrolitik olarak nikel kaplandı ve XRD diyagramlarından nikel kaplama tabakalarının (111), (200) ve (220) düzlemlerinde difraksiyon pikleri gösterdiği tespit edildi. Gerek potansiyodinamik polarizasyon ve gerekse EIS test sonuçları incelendiğinde, elektrolitik nikel kaplamaların hem CuZn30 pirinç ve AISI 1020 çelik malzemelerinin korozyon direncini artırdığı; bununla birlikte kaplama sonucu CuZn30 pirincinin korozyon direncindeki artış miktarının, AISI 1020 çeliğinin korozyon direncindeki artış miktarına göre önemli derecede daha fazla olduğu belirlendi. Ayrıca, her iki taban malzemenin sertlik değerlerinin, yapılan nikel kaplamalarla oldukça arttığı gözlendi.
5. KAYNAKLAR
[1] J.Jagielski, A.S.Khanna, J.Kucinski, D.S.Mishra, P.Racolta, P.Sioshansi, E.Tobin, J.Thereska, V.Uglov, T.Vilaithong, J.Viviente, S.Z.Yang, A.Zalar, “Effect of chromium nitride coating on the corrosion and wear resistance of stainless steel” Appl Surf Sci, cilt 156, 2000, s.47-64
[2] J.E.Gray, B.Luan, “Protective coatings on magnesium and its alloys — a critical review” J Alloys Compd, cilt 336, 2002, s.88-113
[3] Z. Zhenmin, W.Gao, “The effect of substrate on the electroless nickel plating of Mg and Mg alloys” Surf Coat Technol, cilt 200, 2006, s.3553-3560
[4] A.M. El-Sherik, U.Erb, “Synthesis of bulk nanocrystalline nickel by pulsed electrodeposition” J Mater Sci, cilt 30, 1995, s.5743-5749
[5] J.R. Tuck, A.M. Korsunsky, R.I. Davidson, S.J.Bull, D.M.Elliott “Modelling of the hardness of electroplated nickel coatings on copper substrates” Surf Coat Technol, cilt 127, 2000, s.1-8
[6] K.C.Chan, W.K.Chan, N.S.Qu “Effect of current waveform on the deposit quality of electroformed nickels” J Mater Process Technol, cilt 89–90, 1999, s.447-450
[7] M.H.Sohi, M.Jalali “Study of the corrosion properties of zinc–nickel alloy electrodeposits before and after chromating” J Mater Process Technol, cilt 138, 2003, s.63-66
[8] K.R.Baldwin, M.J.Robinson, C.J.E.Smith “The corrosion resistance of electrodeposited zinc-nickel alloy coatings” Corros Sci, cilt 35, 1993, s.1267-1272
[9] A.Asan, M.Kabasakaloglu, M.Işıklan, Z.Kılıç “Corrosion inhibition of brass in presence of terdentate ligands in chloride solution” Corros Sci, cilt 47, 2005, s.1534-1544
6. ÖZGEÇMİŞ
Doç. Dr. Mehmet GAVGALI
Atatürk Üniversitesi
Makina Mühendisliği Bölümü
25240 Erzurum/TÜRKİYE
Bitirdiği Okul: Selçuk Üniversitesi
Oda Sicil No : 27821
Telefon : +90 442 231-4854
Faks : +90 442 236-0957
Cep Telefonu : +90 536 834-9065
e-posta : [email protected]
Doç. Dr. Yaşar TOTİK
Atatürk Üniversitesi
Makina Mühendisliği Bölümü
25240 Erzurum/TÜRKİYE
Bitirdiği Okul: Atatürk Üniversitesi
Oda Sicil No : 53534
Telefon : +90 442 231-4858
Faks : +90 442 236-0957
Cep Telefonu : +90 532 226-4744
e-posta : [email protected]
. . .
İçerik sadece atıfta bulunularak yayınlanabilir: Sivas İş Dünyası. Editöryal görüş, yazarın görüşüne aykırı olabilir.