Semente Edilmiş 8620 Kalite Çeliğin Özellillerine
Sementasyon, mil ve dişli çark gibi kullanım sırasında yüksek zorlamalara maruz kalan makine parçalarının
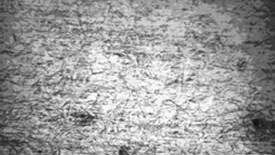
Sementasyon, mil ve dişli çark gibi kullanım sırasında yüksek zorlamalara maruz kalan makine parçalarının
Sementasyon, mil ve dişli çark gibi kullanım sırasında yüksek zorlamalara maruz kalan makine parçalarının yüzey özelliklerinin iyileştirilmesi, yüksek yüzey sertliği, yorulma dayanımı ve aşınma direnci elde etmek için kullanılan yaygın bir ısıl işlem yöntemdir. Düşük karbonlu çeliklerden ( 0.25C) üretilen makine parçaları, sementasyon ile yüksek karbonlu sert bir yüzey ( 0.8-0.9C) ve düşük karbonlu tok bir merkeze sahip olmaktadır. Aynı zamanda, yüzey ve merkezin, farklı hızlarda soğumaları ve oluşan mikroyapıların farklı olması, genellikle yüzeyde basma, merkezde ise çekme kalıntı gerilmeleri oluşturmaktadır. Yüzeyde oluşan basma kalıntı gerilmeleri, eğme ve burma zorlamalarında faydalı olmaktadır. Sementasyon işlemi, aşınma direnci, eğme ve burma yorulma dayanımı ile temas yorulma dayanımının yüksek olmasını da sağlamaktadır [1].
Sementasyon ve sertleştirme işlemleri sonunda tamamen martensite dönüşmeden yapıda kalan östenit fazı, kalıntı östenit olarak bilinir. Dolayısıyla sementasyon ve sertleştirme yapılmış çeliklerin mikroyapıları, büyük ölçüde temperlenmiş martensit ve kalıntı östenitten meydana gelmektedir. Isıl işlemden sonra parçanın kullanımı sırasında çeşitli mekanik etkilerle martensite dönüşen kalıntı östenit, gevrekliği arttırıcı bir faktör olarak mekanik özellikleri büyük ölçüde etkileyebilmektedir [1,2].
Genellikle ısıl işlem uygulanmış halde kullanıma sunulan alaşımlı çeliklerde, ısıl işlemin bir kademesi olarak uygulanan sıfıraltı işlemi, kalıntı östenit hacim oranını azaltıcı ve bu sayede malzemenin özelliklerini önemli ölçüde etkileyici bir işlem olarak bilinmektedir. Sıfıraltı işlemi, esas olarak, malzemenin sertleştirme sonrası -50C ile mutlak sıfır değeri olan -273C aralığına soğutulması, bu ortamda malzemenin tamamında östenitin martensite dönüşmesine yetecek bir süre tutulması ve daha sonra bu ortamdan çıkarılarak oda sıcaklığına ısıtılması kademelerini içerir. İşlem sonunda malzemeye temperleme işlemi uygulanabilmektedir. Prosesin karışıklığı, soğutma, bekletme ve ısıtma parametrelerinin (sıcaklık ve zaman) doğru olarak belirlenebilmesi ve uygulanabilmesinden kaynaklanmaktadır [3]. Konvansiyonel yöntemlerle yapılan sıfıraltı işlemler, -100C’den yüksek sıcaklıklarda gerçekleştirilmekte ve bu sıcaklığın su verilen bir çelikte östenitin tamamen martensite dönüşmesini sağladığı kabul edilmektedir [4].
Bu çalışmada, önemli bir endüstriyel çelik kalitesi olan 8620 çeliğine, ısıl işlem sürecinde uygulanan sıfır altı işlemi ve temperlemenin, mikroyapı ve kalıntı östenit hacim oranı ile sertlik, darbe direnci ve aşınma direncine etkisinin incelenmesi amaçlanmıştır.
2. DENEYSEL ÇALIŞMALAR
Deneysel çalışmalarda kimyasal bileşimi Tablo 1’de verilen AISI 8620 kalite çelikten hazırlanan 10 x 10 x 55 mm3 boyutundaki numuneler kullanılmıştır.
Tablo 1: İncelenen 8620 kalite çeliğin kimyasal bileşimi.
Kimyasal Bileşim, ağ.
C Mn Si Cr Mo Ni P S
0.27 0.80 0.33 0.47 0.19 0.55 0.022 0.015
Sementasyon işlemi sonunda 8620 kalite çeliğin yüzeyindeki karbon oranı 0.98 olarak belirlenmiş olup, bu değer sementasyon öncesine göre yüzeydeki karbon miktarının 3.5 kattan fazla arttığını göstermektedir.
Isıl işlem aşamasında numunelere, 550C’de 60 dakika süreyle yapılan ön ısıtmayı takiben 930C’de asetilen ortamında 24 dakika sementasyon (karbürizasyon) uygulanmış, daha sonra yine bu sıcaklıkta 120 dakika bekletilen numuneler, 860°C’ye soğutulmuş, bu sıcaklıkta 20 dakika bekletildikten sonra da 80°C’deki yağa daldırılarak sertleştirilmiştir. Sertleştirmeyi takiben -70C’de 60 dakika süreyle sıfıraltı işleme tabi tutulan numuneler daha sonra 180C’de 120 dakika temperlenmiştir. Numuneler uygulanan işleme göre, yalnızca sertleştirme işlemi uygulananlar, sertleştirme ve sıfıraltı işlemi uygulananlar ve sertleştirme, sıfıraltı ve temperleme işlemi uygulananlar şeklinde 3 gruba ayrılmıştır.
Mikroyapısal inceleme için standart yöntemlerle zımparalanıp parlatılan numuneler 2 Nital ile dağlandıktan sonra optik mikroskopla incelenmiştir. Mikroyapıdaki kalıntı östenit hacim oranı X-ışınları yöntemiyle belirlenmiştir. Bu amaçla MoK (= 0.07093 nm) radyasyonu kullanan GBC marka X-ışını difraktometresiyle, 20 kV gerilim, 28.5 mA akım şiddeti ve 15-45 arasındaki 2 açılarında X-ışını difraksiyon paternleri elde edilmiştir. Kalıntı östenit hacim oranı, ASTM E975-03 standardına göre, ferrit (200), ferrit (220), östenit (220) ve östenit (311) pikleri dikkate alınarak ve Doğrudan Karşılaştırma Metodu kullanılarak hesaplanmıştır [5,6].
Numunelerin merkez sertliği Rockwell C deneyi ile yüzeyden merkeze doğru sertlik dağılımı ise elmas piramit uç ve 200 g yük kullanılarak Vickers sertlik deneyiyle belirlenmiştir. Numunelerin tokluğunun bir ölçüsü olan darbe direnci değerleri ise oda sıcaklığında yapılan, çentiksiz ve standart V çentikli Charpy darbe deneyleri ile belirlenmiştir. Her gruptan en az 3 numunenin ortalaması, deney sonucu olarak alınmıştır.
Isıl işlem uygulanmış numunelerin aşınma deneyi, aşındırıcı olarak 10 mm çaplı alümina bilya kullanan karşıt hareketli aşınma deney cihazında, kuru ortamda ve oda sıcaklığında yapılmıştır. Karşıt hareket genliğinin 12 mm olduğu deneylerde toplam çevrim sayısı 5000 olarak alınmış, dolayısıyla numunelerin aşınma deneylerindeki toplam kayma mesafesi 120 m olarak belirlenmiştir. Aşınma deneyleri sonunda, Dektak 6M model bir yüzey profilometresi ile aşınma izinin profili belirlenmiştir. Şematik olarak Şekil 1’de verilen aşınma iz profili üzerinde yapılan iz derinliği ve genişliği ölçümleri ve eşitlik (1) kullanılarak aşınma iz alanı hesaplanmıştır.
Şekil 1. Aşınma deneyi sonunda numune üzerinde oluşan aşınma izinin profilinin şematik görünümü.
(1)
Burada,
: Aşınma izinin alanı,
: İz genişliği,
: İz derinliği olarak tanımlanmıştır.
Her numune için aşınma deneyindeki karşıt hareket genliği eşit olduğu için, iz profilinden hesaplanan aşınma iz alanı, malzemenin aşınan miktarının bir ölçüsü olarak alınmıştır. Aşınma iz alanlarının tersi, aşınma direnci olarak ifade edilmiştir. 8620 kalite çeliğin sertleştirilmiş durumdaki aşınma direnci 1 olarak alınmış ve diğer numunelerin aşınma direnci, sertleştirilmiş durumdaki 8620 kalite çeliğin aşınma direncine bölünerek relatif aşınma direnci elde edilmiştir. Farklı ısıl işlem uygulanmış çelik numunelerin aşınma davranışı, relatif aşınma direnci yaklaşımıyla ifade edilmiştir.
3. DENEYSEL SONUÇLAR VE DEĞERLENDİRMELER
Farklı ısıl işlemlerin uygulandığı 8620 kalite çeliğin optik mikroyapı fotoğrafları Şekil 2’de görülmektedir. Çeliğin sertleştirilmiş haldeki mikroyapısı genel olarak martensit ve bir miktar beynitten ibaret olup, sertleştirme işleminden sonra yapılan sıfıraltı işlemi, mikroyapıda çok belirgin bir morfolojik değişime neden olmamıştır. Sertleştirilmiş haldeki mikroyapılarda bir miktar kalıntı östenitin varlığı beklenmekle birlikte, bu fazın optik mikroskopla ayırt edilmesi oldukça güçtür. Öte yandan sıfıraltı işlemiyle kalıntı östenitin martensite dönüşmesi, optik mikroyapı fotoğraflarından kolaylıkla belirlenemeyecek bir mikroyapısal dönüşümdür. Isıl işlemin son kademesi olarak uygulanan temperleme işlemi ise, mikroyapılarda nispeten belirgin bir fark meydana getirmiştir. Gerek sertleştirilmiş gerekse sertleştirildikten sonra sıfıraltı işlemi uygulanmış mikroyapılarda gözlenen beynit morfolojisi, temperlenmiş numunelerde gözlenmemektedir.
Şekil 2. (a) Sertleştirme, (b) Sertleştirme + Sıfıraltı işlem ve (c) Sertleştirme+Sıfıraltı işlem +Temperleme uygulanan 8620 kalite çeliğin optik mikroyapı fotoğrafları.
Kalıntı östenit hacim oranını belirlemeye yönelik yapılan X-ışını difraksiyonu çalışmalarıyla belirlenen XRD paternlerini temsilen, sertleştirilmiş haldeki numunenin XRD paterni Şekil 3’de, XRD paternlerinden hesaplanan kalıntı östenit hacim oranları ise Şekil 4’de verilmiştir. Sertleştirme sonunda 16 ile en yüksek kalıntı östenit hacim oranı elde edilmiş, sertleştirmeyi takiben yapılan sıfıraltı işlemi, kalıntı östenit hacim oranını yaklaşık 38 oranında azaltmıştır. Isıl işlemin son kademesi olarak yapılan temperleme işlemiyle, kalıntı östenit hacim oranı, sertleştirme sonrasına göre yaklaşık 40 azalmıştır. Bunun nedeni muhtemelen kalıntı östenitin temperleme aşamasında ferrit ve sementit fazlarına dönüşmüş olmasıdır.
Şekil 4. Uygulanan ısıl işlemlerin kalıntı östenit hacim oranına etkisi.
8620 kalite çeliğin merkezinin sertliğine ısıl işlemin etkisi Şekil 5’de verilmiş olup, ölçülen sertlik değerleri literatürde verilen değerlerle uyumludur.
Şekil 5. 8620 kalite çeliğin merkezinin sertliğine ısıl işlemin etkisi.
Sıfıraltı işlem ile 8620 kalite çeliğin merkezinin sertliği, kalıntı östenitin martensite dönüşmesi ve sıfıraltı işlem sırasında meydana gelen karbür çökelmesi mekanizmasından dolayı çok düşük bir artış göstermiş, öte yandan temperleme ile sertlik, sertleştirilmiş duruma göre 8 oranında azalarak uygulanan ısıl işlemler arasındaki en düşük sertlik değeri elde edilmiştir. Temperleme sonucu oluşan temperlenmiş martensit yapısının sertliği düşürücü etkisinin, kalıntı östenitin martensite dönüşmesi ve karbür çökelmesi sonucu kazanılan sertlik artışından daha yüksek olduğu anlaşılmaktadır. Öte yandan 8620 kalite çelik, sementasyon işlemine tabi tutulduğundan, bu çelikte yüzeyden merkeze doğru mikrosertlik taraması yapılmış ve sonuçlar Şekil 6’da verilmiştir.
Şekil 6. Sementasyon uygulanmış 8620 kalite çeliğin yüzeyinden merkezine doğru sertlik dağılımı.
Sementasyon işlemi uygulanan 8620 kalite çeliğin sertliği yüzeyden merkeze doğru sürekli olarak azalmaktadır. Yüzeyde en yüksek sertlik, sıfıraltı işlemi sonucu, en düşük sertlik ise temperleme işlemi sonucu elde edilmiştir. Bu yönüyle mikrosertlik sonuçları makro sertlik ölçümleriyle uyumludur. Ancak yüzeyden itibaren mesafe arttıkça, her üç ısıl işlem için de birbirine daha yakın sertlik değerleri elde edilmiştir. Yüzey sertliğinin bir ölçüsü olarak, 500 HV sertliği sağlayan yüzeyden itibaren mesafe (etkin sertlik derinliği) yaygın şekilde kullanılan bir değerdir. Bu çalışmada her üç ısıl işlemle de 500HV0.2 sertlik değeri, yüzeyden yaklaşık 475 m mesafede elde edilmiş olup, her üç ısıl işlemle de aynı etkili sertlik derinliğinin elde edildiğini söylemek mümkündür.
Isıl işlem uygulanan 8620 kalite çeliğin çentikli ve çentiksiz darbe deneyi sonuçları Şekil 7’de verilmiştir. 8620 kalite çeliğin sertleştirilmiş haldeki darbe direnci, sıfıraltı işlemle çok az miktarda artmış, temperleme işlemi sonucu ise yaklaşık 23 azalmıştır. Sıfıraltı işlem sonucu, darbe direncinin bir miktar artması, kalıntı östenitin martensite dönüşmesi sonucu yapının homojenliğinin artmasıyla ilişkilendirilebilir. Temperleme sonucundaki düşme ise, bu aşamada martensitten karbürlerin ayrışması ve/veya kalıntı östenitin ferrit ve sementite ayrışması olabilir. Şekil 5 ve Şekil 7 beraber değerlendirildiğinde, 8620 kalite çeliğe uygulanan sıfıraltı işlemin, tokluk ve sertlik değerlerinde önemli değişikliğe sebep olmadığı görülmektedir.
Şekil 7. 8620 kalite çeliğin çentikli ve çentiksiz darbe direnci değerlerinin uygulanan ısıl işleme göre değişimi.
Farklı ısıl işlem uygulanmış numunelerin relatif aşınma dirençleri Şekil 8’de görülmektedir. Buna göre, 8620 kalite çelikte en yüksek aşınma direnci, sertleştirilmiş durumda elde edilmiş, bu numunenin aşınma direnci, sıfıraltı işlemi ve temperleme sonucu sırasıyla yaklaşık 70 ve 80 oranında azalmıştır.
Şekil 8. 8620 kalite çeliğin relatif aşınma direncinin uygulanan ısıl işleme göre değişimi.
4. SONUÇLAR
Sementasyon ve sertleştirme işlemlerinden sonra 8620 kalite çeliğin yapısındaki kalıntı östenit hacim oranı 16 olarak belirlenmiştir. Sertleştirme sonrası uygulanan sıfıraltı işlem, kalıntı östenit hacim oranını 38 oranında, ısıl işlemin son kademesi olarak uygulanan temperleme ise 40 oranında azaltmıştır. Sıfıraltı işlem, sertlik ve darbe direncinde önemli bir değişime neden olmamış, ancak temperleme ile sertlik, sertleştirilmiş duruma göre 8 oranında, çentikli ve çentiksiz darbe direnci ise yaklaşık 2 oranında azalmıştır. 8620 kalite çelikte sıfıraltı işlem ve temperleme işlemi sonrasında elde edilen relatif aşınma direnci, sertleştirme sonrası elde edilen aşınma direncine göre sırasıyla 70 ve 80 oranında azalmıştır.
5. KAYNAKLAR
[1] Parish, G, “Carburizing: Microstructures and Properties”, ASM International, Metals Park OH, 1999.
[2] Krauss G., “Microstructure and Performance of Carburized Steel, Part II : Austenite, Part III: Austenite & Fatigue Special Papers”, 5-15 ASM International , Metals Park OH, 1995.
[3] Fuerst, J.D., “Cryotreatment”, Panacea or Black Magic, 1996.
[4] Yu, L., Feng, X., Metal Heat Treatment, 1991,1, 24.
[5] ASTM E975-03, “Standard Practice for X-Ray Determination of Retained Austenite in Steel with Near Random Crystallographic Orientation”, ASTM International, Pennsylvania, 1997.
[6] Cullity, B.D., “Elements of X-ray diffraction”, Addison-Wesley, MA, 1978.
. . .
İçerik sadece atıfta bulunularak yayınlanabilir: Sivas İş Dünyası. Editöryal görüş, yazarın görüşüne aykırı olabilir.